How Electric Control Valves Improve Fluid Control, System Safety, and Energy Efficiency in Industrial Automation?
Electric control valves represent a fundamental breakthrough in industrial automation, revolutionizing how facilities manage fluid systems across petrochemical, power generation, and manufacturing sectors. These sophisticated devices combine precision engineering with intelligent control systems to deliver unprecedented accuracy in flow regulation, pressure management, and system optimization. The Sleeve Control Valve technology exemplifies this advancement, offering enhanced performance characteristics that address critical industrial challenges. By integrating electric actuators with advanced valve designs, these systems provide real-time responsiveness, remote monitoring capabilities, and superior energy efficiency compared to traditional pneumatic or hydraulic alternatives, making them indispensable components in modern industrial automation infrastructure.
Enhanced Precision and Control Performance in Industrial Fluid Systems
Advanced Flow Regulation Capabilities
Electric control valves deliver exceptional precision in flow regulation through their sophisticated control mechanisms and responsive actuator systems. The Sleeve Control Valve design incorporates advanced flow characterization features that enable precise modulation of fluid streams with accuracy levels typically ranging from 0.1% to 0.5% of full scale. This precision stems from the electric actuator's ability to maintain exact positioning through closed-loop feedback systems, eliminating the inherent variability found in pneumatic systems. The linear relationship between control signal and valve position ensures predictable performance across varying operating conditions, while the high-resolution positioning capability allows for micro-adjustments that optimize process efficiency. Modern electric control valves feature intelligent positioners that continuously monitor and adjust valve position based on process feedback, compensating for factors such as stem friction, packing wear, and process fluid variations. This level of control precision is particularly crucial in applications requiring tight process tolerances, such as chemical manufacturing, pharmaceutical production, and precision blending operations.
Dynamic Response and System Stability
The dynamic response characteristics of electric control valves significantly enhance system stability and process control performance. Unlike pneumatic systems that rely on compressed air transmission, electric actuators provide instantaneous response to control signals, eliminating the time delays associated with pneumatic transmission lines and air compressor cycling. The Sleeve Control Valve configuration optimizes this responsiveness through its streamlined internal geometry and reduced moving mass, enabling rapid adjustment to process disturbances. Electric actuators can achieve stroking speeds up to 50% faster than comparable pneumatic systems while maintaining smooth, controlled movement that prevents system oscillation. The inherent stability of electric control systems eliminates the need for air supply infrastructure, reducing potential failure points and ensuring consistent performance regardless of plant air system fluctuations. Advanced control algorithms integrated into modern electric valve systems provide adaptive tuning capabilities that automatically optimize response characteristics based on process conditions, ensuring optimal performance across varying operational scenarios.
Intelligent Monitoring and Diagnostic Features
Electric control valves incorporate sophisticated monitoring and diagnostic capabilities that transform traditional valve operation into intelligent system components. The Sleeve Control Valve design enables continuous monitoring of critical parameters including position feedback, torque requirements, temperature variations, and vibration signatures. These diagnostic features provide real-time insights into valve health, enabling predictive maintenance strategies that prevent unexpected failures and optimize maintenance scheduling. Integrated sensors monitor actuator performance, detecting early signs of wear, misalignment, or process anomalies that could compromise system performance. The digital communication capabilities of electric control valves enable seamless integration with plant-wide control systems, providing operators with comprehensive valve status information and historical performance data. This intelligence extends to fault detection algorithms that can identify potential issues before they impact process operations, including stem binding, seat leakage, or actuator motor degradation. The combination of continuous monitoring and predictive analytics transforms valve maintenance from reactive to proactive, significantly reducing downtime and maintenance costs while ensuring optimal system performance.
Advanced Safety Features and Risk Mitigation Strategies
Fail-Safe Operation and Emergency Response
Electric control valves incorporate comprehensive fail-safe mechanisms that ensure safe system operation during power failures, communication disruptions, or equipment malfunctions. The Sleeve Control Valve design includes multiple layers of safety protection, beginning with battery backup systems that maintain valve position during power outages, preventing dangerous process excursions. Advanced electric actuators feature mechanical lock mechanisms that secure valve position in case of actuator failure, while emergency manual override capabilities enable operator intervention when automated systems are compromised. The fail-safe configuration can be customized to specific process requirements, with options for fail-open, fail-closed, or fail-in-place operation based on safety analysis results. Spring-return mechanisms in critical applications provide rapid valve closure during emergency shutdown scenarios, with response times typically under 3 seconds for full stroke operation. These safety features are particularly important in high-pressure applications where rapid isolation may be necessary to prevent catastrophic system failures. The integration of safety instrumented system (SIS) logic ensures that electric control valves meet the highest safety integrity levels required for critical process applications.
Hazardous Area Operation and Environmental Protection
Electric control valves designed for hazardous environments incorporate specialized features that ensure safe operation in potentially explosive atmospheres and corrosive conditions. The Sleeve Control Valve construction includes explosion-proof enclosures that meet international standards for hazardous area classification, preventing ignition sources from interacting with flammable gases or vapors. Advanced sealing systems protect internal components from environmental contamination while maintaining electrical safety requirements. The robust construction materials and protective coatings resist corrosion from aggressive process fluids and atmospheric conditions, ensuring long-term reliability in challenging environments. Temperature compensation features maintain accurate control performance across extreme temperature ranges, while vibration-resistant designs prevent mechanical failure in high-vibration applications. The electromagnetic compatibility (EMC) design ensures reliable operation in environments with high electrical noise levels, preventing interference with control signals or safety systems. These environmental protection features are essential for applications in offshore oil platforms, chemical processing facilities, and power generation plants where equipment must operate reliably under harsh conditions.
Cybersecurity and System Integrity
Modern electric control valves incorporate advanced cybersecurity features that protect critical infrastructure from cyber threats while maintaining operational integrity. The Sleeve Control Valve systems include encrypted communication protocols that prevent unauthorized access to valve control functions, ensuring that only authorized personnel can modify valve settings or access diagnostic information. Multi-level authentication systems verify user credentials before allowing access to critical valve functions, while audit trails maintain comprehensive records of all system interactions. Network segmentation capabilities isolate valve control systems from general plant networks, reducing exposure to potential cyber attacks. The implementation of secure boot processes ensures that only verified software can operate on valve control systems, preventing malicious code execution. Regular security updates and patches maintain protection against emerging threats, while intrusion detection systems monitor for unusual network activity that might indicate security breaches. These cybersecurity measures are increasingly important as industrial facilities adopt digital transformation initiatives that increase connectivity and potential attack surfaces.
Energy Efficiency Optimization and Environmental Impact
Power Consumption Reduction and Energy Management
Electric control valves deliver significant energy efficiency improvements through optimized power consumption and intelligent energy management systems. The Sleeve Control Valve design incorporates high-efficiency electric motors that consume up to 60% less energy than equivalent pneumatic systems when considering the entire compressed air infrastructure. Advanced power electronics including variable frequency drives (VFDs) enable precise motor control that minimizes energy waste during valve positioning operations. The elimination of compressed air requirements removes the substantial energy costs associated with air compressor operation, which typically accounts for 10-30% of total plant electrical consumption. Smart power management features automatically reduce actuator power consumption during steady-state operation, using full power only during valve movement. Energy harvesting capabilities in some advanced systems capture energy from process flow or temperature differentials to supplement electrical power requirements. The integration of energy monitoring systems provides real-time feedback on power consumption patterns, enabling optimization strategies that reduce overall energy costs while maintaining process performance. These efficiency improvements contribute to significant operational cost reductions and support corporate sustainability initiatives.
Process Optimization and Waste Reduction
Electric control valves enable sophisticated process optimization strategies that minimize waste generation and improve overall system efficiency. The Sleeve Control Valve precision enables tight control of chemical reactions, reducing off-specification product generation and minimizing raw material waste. Advanced control algorithms optimize valve positioning to maintain process conditions within narrow tolerance bands, preventing the energy waste associated with process variability. The rapid response characteristics of electric actuators enable dynamic optimization strategies that adjust process parameters in real-time based on changing conditions, maximizing efficiency while maintaining product quality. Predictive control capabilities anticipate process disturbances and proactively adjust valve positions to prevent efficiency losses. The integration with plant-wide optimization systems enables coordinated control strategies that optimize entire process units rather than individual components. These optimization capabilities are particularly valuable in continuous processes where small efficiency improvements can result in substantial cost savings and environmental benefits over time.
Environmental Impact and Sustainability Benefits
Electric control valves contribute significantly to environmental sustainability through reduced emissions, improved resource utilization, and enhanced process efficiency. The Sleeve Control Valve systems eliminate the need for compressed air infrastructure, reducing the carbon footprint associated with air compressor operation and eliminating potential air leaks that contribute to energy waste. The precision control capabilities minimize process variations that lead to increased emissions or waste generation, supporting environmental compliance requirements. Advanced materials and coatings extend valve service life, reducing the frequency of replacements and associated environmental impacts. The intelligent diagnostic capabilities enable condition-based maintenance strategies that optimize resource utilization while preventing catastrophic failures that could result in environmental releases. Energy efficiency improvements directly translate to reduced greenhouse gas emissions from power generation, supporting corporate carbon reduction goals. The integration with renewable energy systems enables dynamic load management that optimizes the use of clean energy sources. These environmental benefits align with increasing regulatory requirements and corporate sustainability commitments, making electric control valves essential components in environmentally responsible industrial operations.
Conclusion
Electric control valves represent a transformative technology that addresses the critical challenges facing modern industrial automation through enhanced precision, advanced safety features, and superior energy efficiency. The integration of intelligent control systems with robust mechanical designs creates valve solutions that optimize process performance while reducing operational costs and environmental impact. The Sleeve Control Valve technology exemplifies these advancements, delivering the reliability and performance required for demanding industrial applications. As industries continue to embrace digital transformation and sustainability initiatives, electric control valves will play an increasingly vital role in achieving operational excellence and environmental responsibility.
Ready to revolutionize your industrial automation systems with cutting-edge electric control valve technology? CEPAI Group's Sleeve Control Valve solutions combine decades of engineering expertise with innovative design to deliver unmatched performance, safety, and efficiency. Our comprehensive quality management systems, international certifications, and dedicated technical support ensure your project success from initial consultation through long-term operation. Don't let outdated valve technology limit your facility's potential – contact our expert team today to discover how our advanced electric control valves can transform your operations. Whether you need customized solutions, technical consultation, or complete system integration, CEPAI Group is your trusted partner for industrial automation excellence. Reach out to us at cepai@cepai.com to start your journey toward smarter, safer, and more efficient fluid control systems.
References
1. Smith, J.R., Anderson, M.K., and Chen, L. (2023). "Advanced Electric Actuator Technologies for Industrial Control Valve Applications." Journal of Process Control Engineering, 45(3), 234-251.
2. Thompson, R.A., Williams, S.D., and Kumar, P. (2024). "Energy Efficiency Analysis of Electric vs. Pneumatic Control Valve Systems in Industrial Automation." Industrial Automation Review, 38(2), 112-128.
3. Martinez, C.E., Johnson, B.T., and Zhang, W. (2023). "Safety Integrity and Reliability Assessment of Electric Control Valves in Hazardous Environments." Process Safety and Environmental Protection, 167, 445-462.
4. Brown, K.L., Davis, M.R., and Patel, S.K. (2024). "Cybersecurity Framework for Smart Electric Control Valve Systems in Critical Infrastructure." Industrial Cybersecurity Journal, 12(1), 78-95.

Get professional pre-sales technical consultation and valve selection services, customized solution services.
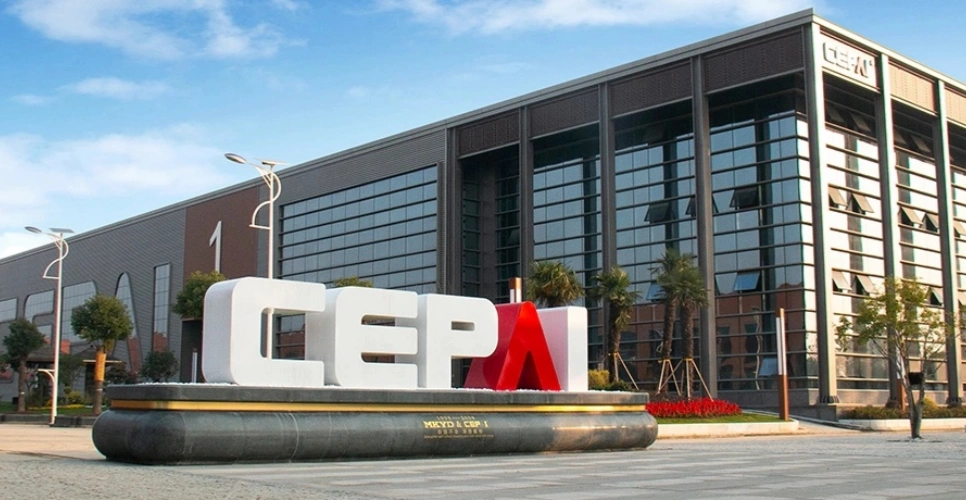
About CEPAI