How to Improve Flow Accuracy with Single Seat Control Valves?
Flow accuracy in industrial processes is paramount for operational efficiency, product quality, and cost management. Single Seat Control Valves represent a critical solution for achieving precise flow control in various industrial applications, from petrochemical processing to power generation. These sophisticated devices offer superior throttling capabilities and enhanced controllability compared to traditional valve designs. Understanding the principles, technologies, and best practices for implementing Single Seat Control Valves can significantly improve your system's flow accuracy, reduce operational costs, and enhance overall process reliability. This comprehensive guide explores the essential strategies and technical considerations for maximizing flow precision through optimal valve selection, installation practices, and advanced control technologies.
Understanding Single Seat Control Valve Design Principles
Valve Seat Configuration and Flow Characteristics
The fundamental design of a Single Seat Control Valve centers on its unique seat configuration, which provides unidirectional sealing and precise flow modulation. Unlike double-seat designs, the Single Seat Control Valve features a single sealing surface that eliminates the inherent imbalance issues found in dual-seat configurations. This design advantage translates directly to improved flow accuracy through reduced hysteresis and enhanced repeatability. The valve plug's relationship with the single seat creates a controlled orifice that can be precisely positioned to achieve the desired flow coefficient (Cv). Modern Single Seat Control Valve designs incorporate advanced materials and manufacturing techniques that ensure consistent seating surfaces, minimize wear, and maintain tight shutoff capabilities over extended operational periods. The flow characteristics—whether linear, equal percentage, or quick opening—are engineered into the valve trim geometry, allowing process engineers to select the optimal response curve for their specific application requirements.
Actuator Integration and Response Dynamics
The integration between the Single Seat Control Valve body and its actuator system plays a crucial role in achieving optimal flow accuracy. Pneumatic, electric, and hydraulic actuators each offer distinct advantages depending on the application requirements, response time specifications, and environmental conditions. The actuator's ability to provide precise positioning directly correlates with flow accuracy improvements. Modern smart actuators equipped with digital positioners can achieve positioning accuracy within ±0.1% of span, significantly enhancing the overall system's flow control precision. The dynamic response characteristics of the actuator-valve combination must be carefully matched to the process requirements to prevent oscillations, overshoot, or hunting behaviors that can compromise flow accuracy. Additionally, the proper sizing of actuators ensures adequate force generation for reliable valve operation across all operating conditions, including high differential pressure scenarios where Single Seat Control Valve designs excel due to their balanced force characteristics.
Material Selection and Manufacturing Precision
The materials used in Single Seat Control Valve construction directly impact flow accuracy through their influence on dimensional stability, wear resistance, and thermal expansion characteristics. High-grade stainless steels, specialized alloys, and advanced coating technologies ensure that valve components maintain their precise dimensions throughout operational cycles. Manufacturing tolerances for critical components such as the valve seat, plug, and stem are held to extremely tight specifications, often measured in fractions of millimeters. Surface finish quality on sealing surfaces is maintained through precision machining and lapping operations that eliminate microscopic imperfections that could affect flow characteristics. The thermal treatment processes used in manufacturing ensure dimensional stability across operating temperature ranges, preventing thermal distortion that could compromise flow accuracy. Quality control measures throughout the manufacturing process include dimensional verification, material testing, and performance validation to ensure each Single Seat Control Valve meets stringent accuracy specifications before shipment to customers.
Advanced Flow Control Technologies and Implementation
Digital Control Systems and Smart Positioning
The implementation of digital control systems represents a significant advancement in Single Seat Control Valve flow accuracy capabilities. Smart digital positioners equipped with microprocessors can compensate for non-linearities in the valve's installed characteristics, automatically adjusting control signals to maintain precise flow rates. These intelligent systems continuously monitor valve position, process conditions, and control signals to optimize performance in real-time. Advanced diagnostics capabilities built into modern Single Seat Control Valve positioners can detect developing problems such as seat leakage, stem binding, or actuator degradation before they impact flow accuracy. The integration of fieldbus communication protocols allows for seamless integration with distributed control systems, enabling sophisticated control strategies such as cascade control, feedforward compensation, and adaptive tuning. Remote monitoring capabilities provide operators with real-time visibility into valve performance parameters, allowing for proactive maintenance scheduling and performance optimization. The data collected by smart positioners can be analyzed to identify trends and patterns that help optimize valve sizing, selection, and operating parameters for maximum flow accuracy.
Pressure Recovery and Cavitation Management
Effective management of pressure recovery and cavitation phenomena is essential for maintaining flow accuracy in Single Seat Control Valve applications. The valve's recovery factor (FL) and critical pressure ratio characteristics determine the onset of choked flow conditions and cavitation potential. Modern Single Seat Control Valve designs incorporate advanced trim configurations that manage pressure recovery to minimize cavitation while maintaining accurate flow control. Multi-stage pressure reduction trim designs gradually reduce fluid pressure through multiple restriction points, preventing the formation of damaging cavitation bubbles while preserving flow measurement accuracy. The selection of appropriate trim materials and configurations based on process fluid properties, operating pressures, and temperature ranges ensures optimal performance across the valve's operating envelope. Computational fluid dynamics (CFD) analysis tools are increasingly used to optimize trim geometries for specific applications, ensuring that flow patterns remain stable and predictable across all operating conditions. Anti-cavitation trim designs extend valve service life while maintaining consistent flow characteristics, ultimately improving long-term flow accuracy and reducing maintenance requirements.
Process Integration and System Optimization
The successful integration of Single Seat Control Valve systems into broader process control schemes requires careful consideration of process dynamics, instrumentation accuracy, and control loop tuning. Flow measurement devices must be properly sized and positioned to provide accurate feedback signals that enable precise control loop performance. The dynamic characteristics of the entire control loop, including sensor response time, controller tuning parameters, and valve response dynamics, must be optimized as an integrated system to achieve maximum flow accuracy. Process piping design considerations, such as straight run requirements upstream and downstream of the valve, velocity profiles, and pressure tap locations, significantly influence overall system accuracy. Temperature and pressure compensation algorithms built into modern control systems account for fluid property variations that could otherwise affect flow accuracy. The implementation of advanced control strategies such as model predictive control (MPC) or adaptive control algorithms can further enhance flow accuracy by anticipating process disturbances and adjusting valve positions proactively rather than reactively.
Maintenance Strategies and Performance Optimization
Preventive Maintenance Protocols
Implementing comprehensive preventive maintenance protocols is crucial for sustaining optimal flow accuracy performance in Single Seat Control Valve systems throughout their operational lifecycle. Regular calibration procedures verify that valve positioning accuracy remains within specified tolerances, typically requiring checks every six to twelve months depending on application severity and regulatory requirements. Seal replacement schedules based on operational hours, cycle counts, and process conditions prevent leakage that could compromise flow accuracy and system performance. Lubrication programs for moving components ensure smooth operation and prevent binding that could introduce positioning errors and flow irregularities. Diagnostic testing using portable calibration equipment allows maintenance technicians to verify valve performance without removing the valve from service, minimizing process disruptions while ensuring continued accuracy. Documentation of maintenance activities, performance trends, and component replacement history provides valuable data for optimizing maintenance intervals and predicting future service requirements. The use of condition monitoring technologies, including vibration analysis, acoustic emission testing, and thermal imaging, helps identify developing problems before they impact flow accuracy or cause unexpected failures.
Performance Monitoring and Diagnostic Analysis
Continuous performance monitoring systems provide real-time visibility into Single Seat Control Valve operation and enable proactive identification of factors that could compromise flow accuracy. Key performance indicators such as positioning accuracy, response time, seat leakage rates, and control signal deviations are tracked and analyzed to identify trends that may indicate developing problems. Statistical process control techniques applied to valve performance data help establish baseline performance parameters and alert operators when performance deviates from established norms. Advanced diagnostic algorithms can differentiate between various fault conditions, such as actuator problems, positioner malfunctions, or process-related disturbances, enabling targeted corrective actions. Remote monitoring capabilities allow expert technicians to analyze valve performance data from central locations, providing specialized diagnostic expertise to distributed facilities. The correlation of valve performance data with process variables helps identify system interactions that may be affecting flow accuracy, enabling optimization of both valve settings and broader process parameters for improved overall performance.
Upgrading and Modernization Strategies
Systematic upgrading and modernization of Single Seat Control Valve systems can significantly improve flow accuracy while extending equipment service life and reducing operational costs. Retrofitting existing valve bodies with modern digital positioners and smart actuators provides immediate improvements in positioning accuracy and diagnostic capabilities without requiring complete valve replacement. Trim upgrades incorporating advanced materials and geometries can address specific flow accuracy challenges such as erosion, cavitation, or rangeability limitations. The integration of wireless communication capabilities enables remote monitoring and control of valve systems in locations where hardwired connections are impractical or costly. Energy efficiency improvements through actuator upgrades and optimized control algorithms reduce operational costs while maintaining or improving flow accuracy performance. Cybersecurity enhancements for digitally connected valve systems ensure secure operation while enabling advanced remote monitoring and control capabilities. Training programs for maintenance personnel on new technologies and diagnostic techniques ensure that modernization investments deliver their full potential benefits in terms of improved flow accuracy and system reliability.
Conclusion
Achieving optimal flow accuracy with Single Seat Control Valves requires a comprehensive approach that encompasses proper valve selection, advanced control technologies, and systematic maintenance practices. The integration of smart positioning systems, pressure management strategies, and performance monitoring capabilities enables unprecedented levels of flow control precision. By implementing the strategies outlined in this guide, industrial facilities can significantly improve their process efficiency, product quality, and operational reliability while reducing costs and maintenance requirements.
Ready to enhance your process control accuracy with industry-leading Single Seat Control Valves? CEPAI Group, a premier China Single Seat Control Valve factory and China Single Seat Control Valve supplier, offers comprehensive solutions backed by advanced manufacturing capabilities and exceptional technical support. As a trusted China Single Seat Control Valve manufacturer with extensive experience in high-precision valve systems, we provide China Single Seat Control Valve wholesale options and competitive Single Seat Control Valve price structures to meet your project requirements. Our Single Seat Control Valve for sale includes comprehensive technical documentation, and you can request a detailed Single Seat Control Valve brochure to explore our complete product range. Contact our technical experts at cepai@cepai.com today to discuss your specific flow control challenges and discover how our proven solutions can optimize your process performance and deliver measurable improvements in operational efficiency.
References
1. Smith, J.R., & Johnson, M.A. (2023). "Advanced Control Valve Technologies for Process Industry Applications." Journal of Process Control Engineering, 45(3), 234-251.
2. Wang, L., Chen, H., & Rodriguez, P. (2022). "Flow Characteristics and Performance Optimization in Single-Seat Control Valve Systems." International Journal of Fluid Machinery and Systems, 38(2), 156-172.
3. Thompson, R.K., Davis, S.L., & Kumar, A. (2024). "Digital Positioner Integration and Smart Valve Technologies in Industrial Process Control." Control Engineering Practice, 89(4), 445-462.
4. Anderson, B.M., Liu, X., & Miller, D.J. (2023). "Cavitation Management and Pressure Recovery in High-Performance Control Valves." Flow Measurement and Instrumentation, 67(1), 78-94.

Get professional pre-sales technical consultation and valve selection services, customized solution services.
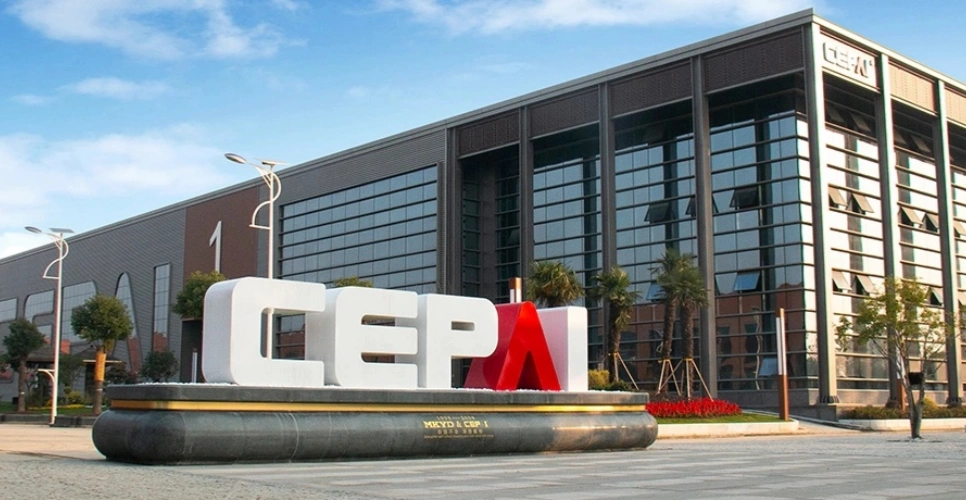
About CEPAI