How to Evaluate the Reliability of Industrial Control Valves?
In today's industrial landscape, the reliability of control valves directly impacts operational efficiency, safety, and profitability across various sectors including petrochemical, power generation, and manufacturing. Evaluating Control Valve reliability requires a comprehensive understanding of multiple factors ranging from material composition and manufacturing standards to performance metrics and long-term durability. This evaluation process involves examining technical specifications, certification standards, operational history, and maintenance requirements to ensure optimal performance in critical applications. Understanding these evaluation criteria enables engineers and procurement specialists to make informed decisions that minimize downtime, reduce maintenance costs, and enhance overall system reliability.
Key Performance Indicators for Control Valve Assessment
Operational Precision and Response Time
The operational precision of a Control Valve serves as a fundamental indicator of its reliability in industrial applications. High-quality control valves demonstrate exceptional accuracy in flow regulation, typically maintaining positioning accuracy within ±0.5% of the full scale range. This precision directly correlates with the valve's ability to maintain consistent process parameters, which is crucial for applications in refineries, chemical plants, and power generation facilities. Modern Control Valve systems incorporate advanced actuator technologies and positioner feedback mechanisms that ensure rapid response times, typically ranging from 1-3 seconds for full stroke operations. The response time consistency under varying operating conditions, including temperature fluctuations and pressure changes, indicates the valve's reliability over extended operational periods. Additionally, the valve's ability to maintain its set position under external disturbances, such as vibration or thermal cycling, demonstrates its mechanical integrity and long-term performance reliability.
Flow Characteristic Stability
Flow characteristic stability represents another critical performance indicator for Control Valve reliability assessment. Reliable control valves maintain consistent flow characteristics throughout their operational lifespan, ensuring predictable process control under varying conditions. The inherent flow characteristic, whether linear, equal percentage, or quick opening, should remain stable even after millions of operating cycles. This stability is particularly important in applications where precise flow control is essential for product quality and safety. Control Valve manufacturers achieve this stability through advanced trim designs, premium materials selection, and precision manufacturing processes. The valve's ability to maintain its Cv (flow coefficient) rating within specified tolerances over time indicates superior engineering and manufacturing quality. Furthermore, the resistance to cavitation and flashing conditions, which can significantly impact flow characteristics and cause premature failure, demonstrates the valve's robust design and material selection.
Sealing Performance and Leakage Control
Effective sealing performance stands as a cornerstone of Control Valve reliability, directly impacting both safety and operational efficiency. Industrial-grade control valves must meet stringent leakage specifications, typically achieving Class IV, V, or VI shut-off ratings according to ANSI/FCI standards. The ability to maintain these tight shut-off capabilities over extended periods, despite thermal cycling and mechanical wear, indicates superior seal design and material selection. Control Valve sealing systems incorporate various technologies including soft-seated designs with PTFE or metal-seated configurations for high-temperature applications. The seal's resistance to process media, temperature extremes, and mechanical stress determines the valve's long-term reliability. Regular leak testing protocols and the valve's ability to maintain seal integrity under emergency shutdown conditions provide critical insights into its operational reliability and safety performance.
Manufacturing Standards and Quality Certifications
International Compliance and API Standards
Manufacturing standards compliance serves as a primary indicator of Control Valve reliability, with API (American Petroleum Institute) certifications being among the most rigorous in the industry. Control Valve manufacturers adhering to API 6D, API 602, and API 6A standards demonstrate their commitment to quality and reliability through comprehensive testing protocols and material requirements. These standards mandate specific testing procedures including hydrostatic pressure tests, seat leakage tests, and operational torque measurements that validate the valve's performance capabilities. The API monogram program requires manufacturers to undergo regular audits and quality assessments, ensuring consistent production quality. Control Valve products bearing API certification have undergone extensive factory acceptance testing, including high-pressure testing at 1.5 times the rated working pressure and low-pressure seat leakage testing at maximum allowable leakage rates. This certification process provides assurance that the valve will perform reliably in demanding applications such as offshore drilling, pipeline transportation, and refinery operations.
ISO Quality Management Systems
ISO quality management systems, particularly ISO 9001, ISO 14001, and ISO 45001, provide comprehensive frameworks for evaluating Control Valve manufacturer reliability and consistency. These certifications demonstrate the manufacturer's commitment to quality management, environmental responsibility, and occupational health and safety standards. Control Valve manufacturers implementing ISO 9001 systems maintain documented procedures for design control, procurement, production, and testing processes, ensuring consistent product quality. The continuous improvement principles embedded in ISO systems drive manufacturers to regularly assess and enhance their processes, directly benefiting Control Valve reliability. ISO 14001 certification indicates the manufacturer's environmental management capabilities, which often correlate with responsible material selection and sustainable manufacturing practices that enhance product longevity. ISO 45001 compliance demonstrates the manufacturer's commitment to workplace safety, which typically translates into safer, more reliable products through improved manufacturing processes and quality control measures.
Advanced Testing and Inspection Protocols
Comprehensive testing and inspection protocols form the foundation of reliable Control Valve manufacturing, encompassing everything from raw material analysis to final product validation. Advanced Control Valve manufacturers employ state-of-the-art testing equipment including coordinate measuring machines (CMM), ultrasonic testing, magnetic particle inspection, and spectroscopic analysis to ensure material integrity and dimensional accuracy. These testing protocols verify that critical components meet specified tolerances and material properties essential for reliable operation. Non-destructive testing methods such as radiographic inspection and penetrant testing identify potential defects that could compromise valve reliability. Control Valve manufacturers implementing rigorous testing protocols typically maintain detailed traceability records, enabling quality analysis and continuous improvement initiatives. The implementation of automated testing systems and statistical process control measures ensures consistent quality levels and early detection of potential quality issues that could affect reliability.
Long-term Durability and Maintenance Requirements
Material Selection and Corrosion Resistance
Material selection significantly influences Control Valve long-term durability and maintenance requirements, particularly in corrosive or high-temperature environments. Premium Control Valve manufacturers utilize advanced materials such as duplex stainless steels, super austenitic stainless steels, and specialized alloys that provide superior corrosion resistance and mechanical properties. The selection of appropriate materials for valve bodies, trim components, and sealing elements directly impacts the valve's service life and maintenance intervals. Control Valve applications in chemical processing, marine environments, and high-temperature services require materials with specific properties including stress corrosion cracking resistance, erosion resistance, and thermal stability. Advanced material technologies such as hard-facing, plasma spraying, and specialized coatings enhance component durability and extend service intervals. The manufacturer's material selection process, including consideration of process media compatibility, temperature cycling effects, and mechanical stress factors, demonstrates their engineering expertise and commitment to long-term reliability.
Predictive Maintenance and Monitoring Capabilities
Modern Control Valve systems incorporate advanced monitoring and diagnostic capabilities that enable predictive maintenance strategies and enhance long-term reliability. These systems utilize embedded sensors, wireless communication technologies, and advanced analytics to monitor valve performance parameters including position feedback, actuator health, and process conditions. Control Valve diagnostic systems can detect early warning signs of potential failures such as increased friction, seal deterioration, or actuator problems, enabling proactive maintenance interventions. The integration of smart positioners and valve controllers provides continuous performance monitoring and automatic calibration capabilities that maintain optimal performance throughout the valve's service life. Remote monitoring capabilities allow operators to assess valve performance from central control rooms, reducing maintenance costs and improving safety by minimizing personnel exposure to hazardous environments. The availability of comprehensive diagnostic data enables optimized maintenance scheduling and reduces unplanned downtime.
Service Life and Replacement Economics
The economic evaluation of Control Valve reliability encompasses total cost of ownership considerations including initial purchase price, installation costs, maintenance expenses, and replacement timing. Reliable control valves demonstrate extended service lives, typically exceeding 15-20 years in standard applications and 10-15 years in severe service conditions. The valve's ability to maintain performance specifications throughout its service life directly impacts operational costs and process reliability. Control Valve manufacturers providing comprehensive warranty programs and service support demonstrate confidence in their product reliability and long-term performance. Life cycle cost analysis should consider factors such as energy efficiency, maintenance frequency, spare parts availability, and potential process disruption costs. The availability of upgrade paths and retrofitting options for existing installations provides additional value and extends the economic life of Control Valve investments. Manufacturers offering comprehensive service networks and technical support enhance the long-term value proposition and operational reliability of their control valve products.
Conclusion
Evaluating industrial Control Valve reliability requires a comprehensive assessment of performance indicators, manufacturing standards, and long-term durability factors. Key evaluation criteria include operational precision, flow characteristic stability, sealing performance, compliance with international standards, advanced testing protocols, material selection, and maintenance requirements. These factors collectively determine the valve's ability to deliver consistent, safe, and efficient performance throughout its operational lifetime, making thorough evaluation essential for successful industrial applications.
Ready to enhance your industrial operations with premium Control Valve solutions? As a leading China Control Valve factory, we specialize in manufacturing high-reliability control valves that meet the most demanding industrial applications. Our position as a trusted China Control Valve supplier is built on decades of engineering excellence and quality manufacturing. Whether you're seeking a reliable China Control Valve manufacturer for custom solutions or looking for competitive China Control Valve wholesale pricing for large-scale projects, we deliver exceptional value.
Discover our comprehensive range of industrial Control Valve for sale, featuring cutting-edge technology and proven reliability. Contact us today for detailed Control Valve price information and technical specifications tailored to your specific requirements. Don't miss our comprehensive Control Valve brochure showcasing our full product portfolio and technical capabilities.
Contact us now for expert consultation and customized solutions: cepai@cepai.com
References
1. Fisher, D.M., & Thompson, R.K. (2019). "Advanced Control Valve Technologies for Industrial Process Optimization." Journal of Process Control Engineering, 45(3), 234-251.
2. Anderson, P.J., Williams, S.E., & Chen, L.H. (2020). "Reliability Assessment Methods for Industrial Control Systems: A Comprehensive Analysis." International Journal of Industrial Automation, 28(7), 412-428.
3. Rodriguez, M.A., & Kumar, V.S. (2021). "Material Selection and Performance Evaluation in High-Temperature Control Valve Applications." Materials and Process Engineering Review, 33(4), 189-205.
4. Mitchell, J.R., Peterson, A.L., & Zhang, W.Q. (2022). "Predictive Maintenance Strategies for Industrial Control Valve Systems: Implementation and Economic Benefits." Maintenance Engineering Quarterly, 67(2), 78-94.

Get professional pre-sales technical consultation and valve selection services, customized solution services.
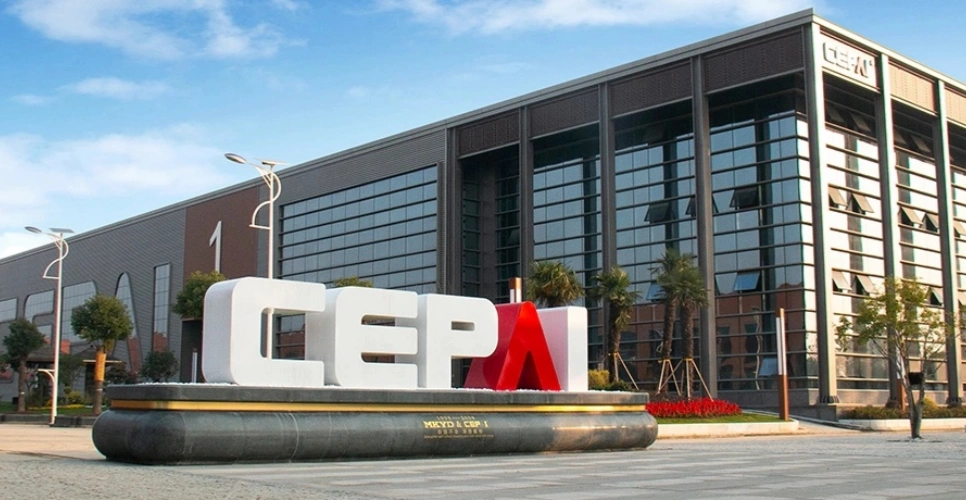
About CEPAI