Comparing Valve Materials for Corrosion Resistance
When selecting industrial valves for critical applications, understanding how different materials respond to corrosive environments becomes paramount for operational reliability and cost-effectiveness. Corrosion resistance directly impacts the lifespan, performance, and safety of Control Valve systems across petrochemical, oil and gas, and power generation industries. The choice of valve materials determines not only the initial investment but also long-term maintenance costs, system downtime, and overall process efficiency. This comprehensive analysis examines the corrosion resistance characteristics of various valve materials, providing essential insights for engineers and procurement specialists making informed decisions about Control Valve selection in challenging operating environments.
Material Categories and Their Corrosion Resistance Properties
Carbon Steel Valves in Corrosive Applications
Carbon steel remains one of the most widely used materials in valve manufacturing due to its excellent mechanical properties, cost-effectiveness, and proven performance in many industrial applications. However, when evaluating carbon steel Control Valve options for corrosive environments, several critical factors must be considered. Carbon steel exhibits varying degrees of corrosion resistance depending on the specific grade, heat treatment, and environmental conditions. In mildly corrosive environments with proper protective coatings, carbon steel Control Valve systems can provide reliable service for extended periods. The material's high strength-to-weight ratio makes it particularly suitable for high-pressure applications where mechanical integrity is paramount. The corrosion mechanisms affecting carbon steel valves include uniform corrosion, pitting corrosion, and galvanic corrosion when in contact with dissimilar metals. Understanding these mechanisms is crucial for proper Control Valve selection and maintenance strategies. Carbon steel's susceptibility to oxidation in the presence of moisture and oxygen requires careful consideration of operating conditions, protective coatings, and cathodic protection systems. Modern carbon steel alloys incorporate various alloying elements to enhance corrosion resistance while maintaining cost-effectiveness, making them viable options for many Control Valve applications where complete corrosion immunity is not required. Environmental factors such as temperature, pH levels, and the presence of chlorides significantly influence carbon steel's corrosion behavior in Control Valve applications. In alkaline environments, carbon steel can form protective oxide layers that provide reasonable corrosion resistance. However, in acidic or chloride-rich environments, accelerated corrosion can occur, potentially compromising valve integrity and performance. Proper material selection based on comprehensive corrosion analysis ensures optimal Control Valve performance throughout the intended service life.
Stainless Steel Alloys for Enhanced Protection
Stainless steel alloys represent a significant advancement in corrosion-resistant materials for Control Valve applications, offering superior performance compared to carbon steel in most corrosive environments. The chromium content in stainless steel forms a passive oxide layer that provides excellent protection against various corrosive agents. Different grades of stainless steel, including 304, 316, 317, and duplex stainless steels, offer varying levels of corrosion resistance depending on their alloy composition and microstructure. Control Valve manufacturers often specify stainless steel for applications involving chemical processing, marine environments, and food-grade applications where corrosion resistance is critical. The austenitic stainless steel grades, particularly 316 and 316L, demonstrate exceptional resistance to pitting and crevice corrosion due to their molybdenum content. These materials are particularly suitable for Control Valve applications in chloride-containing environments, such as seawater service or chemical processing involving halogenated compounds. The low carbon variants (316L) provide additional benefits by reducing the risk of carbide precipitation and intergranular corrosion, making them ideal for welded Control Valve constructions. Understanding the relationship between alloy composition and corrosion resistance enables engineers to select the most appropriate stainless steel grade for specific service conditions. Duplex stainless steels combine the benefits of austenitic and ferritic microstructures, providing enhanced strength and corrosion resistance compared to standard austenitic grades. These advanced materials are particularly valuable in Control Valve applications involving high-pressure, high-temperature, or highly corrosive conditions. The balanced microstructure provides superior resistance to stress corrosion cracking and chloride-induced pitting, making duplex stainless steels excellent choices for offshore oil and gas applications where Control Valve reliability is paramount. Proper heat treatment and fabrication techniques are essential to maintain the optimal microstructure and corrosion resistance properties in duplex stainless steel valves.
Specialty Alloys and Exotic Materials
For the most demanding corrosive environments, specialty alloys and exotic materials provide superior corrosion resistance that justifies their higher initial cost through extended service life and reduced maintenance requirements. Nickel-based superalloys, such as Inconel and Hastelloy, demonstrate exceptional resistance to high-temperature oxidation, sulfidation, and corrosion in aggressive chemical environments. These materials are frequently specified for Control Valve applications in petrochemical processing, power generation, and aerospace industries where extreme service conditions exceed the capabilities of conventional stainless steels. Titanium and titanium alloys offer outstanding corrosion resistance in chloride environments, seawater, and many organic and inorganic acids, making them excellent choices for specialized Control Valve applications. The material's high strength-to-weight ratio and biocompatibility make it particularly suitable for pharmaceutical and biotechnology applications where product contamination must be avoided. However, titanium's susceptibility to hydrogen embrittlement and its relatively high cost require careful consideration during Control Valve design and selection processes. Proper understanding of titanium's corrosion mechanisms and limitations ensures successful implementation in appropriate applications. Corrosion-resistant alloys (CRAs) such as 904L, 254 SMO, and various nickel-chromium-molybdenum alloys provide intermediate solutions between standard stainless steels and exotic superalloys. These materials offer enhanced corrosion resistance compared to conventional stainless steels while maintaining reasonable cost-effectiveness for Control Valve applications in moderately aggressive environments. The selection of CRAs requires comprehensive understanding of the specific corrosive agents present in the application, as different alloys excel in different corrosive environments. Proper material testing and qualification procedures ensure optimal Control Valve performance throughout the intended service life.
Environmental Factors Affecting Material Selection
Temperature and Thermal Cycling Effects
Temperature plays a crucial role in determining the corrosion behavior of valve materials and significantly influences Control Valve material selection decisions. Elevated temperatures generally accelerate corrosion reactions, potentially reducing the effectiveness of protective oxide layers and increasing the risk of various corrosion mechanisms. The relationship between temperature and corrosion rate follows complex kinetics that vary depending on the material composition, environmental conditions, and specific corrosive agents present. Understanding these relationships is essential for proper Control Valve specification in high-temperature applications such as power generation, petrochemical processing, and steam systems. Thermal cycling introduces additional challenges for Control Valve materials through differential thermal expansion, thermal stress, and the potential for protective oxide layer cracking. Repeated heating and cooling cycles can compromise the integrity of passive films on stainless steels and other corrosion-resistant materials, potentially exposing the underlying metal to corrosive attack. The design of Control Valve systems must account for thermal expansion differences between various components to prevent stress concentration and potential failure points. Material selection should consider not only the maximum operating temperature but also the frequency and magnitude of thermal cycling expected during service. High-temperature corrosion mechanisms, including sulfidation, carburization, and metal dusting, require specialized materials and protective strategies for Control Valve applications in extreme environments. These mechanisms can rapidly degrade conventional materials, leading to premature failure and safety concerns. The selection of appropriate high-temperature alloys, protective coatings, and design strategies ensures reliable Control Valve operation in challenging thermal environments. Regular monitoring and inspection protocols help identify early signs of high-temperature corrosion before critical failures occur.
Chemical Environment and pH Considerations
The chemical composition of the process fluid represents one of the most critical factors in Control Valve material selection for corrosion resistance. Different materials exhibit varying degrees of compatibility with specific chemicals, and understanding these relationships is essential for preventing premature failure and ensuring safe operation. Acidic environments can rapidly attack many common valve materials, particularly carbon steels and some stainless steel grades, requiring careful material selection based on the specific acids present and their concentrations. Control Valve applications in chemical processing industries often involve multiple corrosive agents simultaneously, complicating material selection decisions. pH levels significantly influence the corrosion behavior of valve materials, with most metals exhibiting minimum corrosion rates within specific pH ranges. Stainless steels generally perform well in neutral to slightly alkaline conditions but may experience accelerated corrosion in strongly acidic or alkaline environments. The presence of oxidizing agents, such as nitric acid or hydrogen peroxide, can enhance the corrosion resistance of some materials while accelerating the corrosion of others. Understanding the complex interactions between pH, oxidizing conditions, and material composition enables engineers to select appropriate Control Valve materials for specific chemical environments. Chloride-containing environments present particular challenges for many valve materials due to their aggressive nature and tendency to cause localized corrosion phenomena such as pitting and stress corrosion cracking. The concentration of chlorides, temperature, and presence of other ions all influence the severity of chloride-induced corrosion in Control Valve applications. Materials with high molybdenum content, such as 316 stainless steel and super duplex stainless steels, demonstrate superior resistance to chloride-induced corrosion and are often specified for seawater service and chemical processing applications involving chlorinated compounds. Proper material testing in simulated service conditions provides valuable data for making informed Control Valve material selection decisions.
Mechanical Stress and Flow Dynamics
Mechanical stress significantly influences the corrosion behavior of valve materials through various mechanisms, including stress corrosion cracking, corrosion fatigue, and erosion-corrosion. Control Valve applications often involve high-pressure conditions, flow-induced vibrations, and mechanical loading that can accelerate corrosion processes and reduce service life. The combination of tensile stress and specific corrosive environments can lead to stress corrosion cracking, a particularly dangerous failure mode that can occur at stress levels well below the material's yield strength. Understanding the relationship between mechanical stress and corrosion enables proper Control Valve design and material selection to prevent premature failures. Flow dynamics within Control Valve systems create complex stress patterns and can influence corrosion behavior through several mechanisms. High-velocity flows can remove protective oxide layers, exposing fresh metal surfaces to corrosive attack in a process known as erosion-corrosion. Turbulent flow conditions can increase mass transfer rates of corrosive species to the metal surface, potentially accelerating corrosion reactions. The design of Control Valve internals must consider flow patterns, velocity profiles, and potential areas of flow stagnation that could promote localized corrosion. Computational fluid dynamics analysis helps optimize valve designs to minimize erosion-corrosion risks while maintaining required flow characteristics. Cavitation represents a specific flow-related phenomenon that can cause severe damage to Control Valve components through both mechanical and electrochemical mechanisms. The formation and collapse of vapor bubbles create intense local pressures and temperatures that can remove protective films and create reactive metal surfaces. The selection of cavitation-resistant materials and appropriate Control Valve designs helps prevent cavitation damage in applications involving high pressure drops or volatile fluids. Regular inspection and monitoring protocols help identify early signs of cavitation damage before catastrophic failures occur.
Industry-Specific Material Requirements
Oil and Gas Sector Specifications
The oil and gas industry presents some of the most challenging corrosive environments for Control Valve applications, requiring specialized materials and design approaches to ensure reliable operation and safety. Hydrogen sulfide (H2S) environments, commonly encountered in sour gas and crude oil applications, pose significant challenges due to the risk of sulfide stress cracking and hydrogen-induced cracking. NACE MR0175/ISO 15156 standards provide comprehensive guidelines for material selection in H2S-containing environments, specifying acceptable materials, hardness limits, and qualification requirements for Control Valve applications. Understanding these industry standards is crucial for proper material selection and ensuring compliance with safety regulations. Carbon dioxide (CO2) corrosion represents another major concern in oil and gas Control Valve applications, particularly in systems handling wet CO2 or CO2-containing hydrocarbons. The formation of carbonic acid in the presence of water can cause severe corrosion of carbon steel components, requiring the use of corrosion-resistant alloys or appropriate inhibition strategies. The selection of materials for CO2 environments depends on factors such as partial pressure, temperature, water content, and the presence of other corrosive species. Corrosion-resistant alloys such as 316 stainless steel, duplex stainless steels, and nickel-based alloys are commonly specified for Control Valve applications in CO2-rich environments. Seawater and produced water applications in offshore oil and gas operations require specialized material considerations due to the high chloride content and potential for microbiologically influenced corrosion. Super duplex stainless steels and nickel-based alloys are frequently specified for Control Valve applications in these environments due to their superior resistance to chloride-induced pitting and stress corrosion cracking. The presence of bacteria and other microorganisms can accelerate corrosion processes and require additional considerations for material selection and system design. Proper biocide treatment and material selection strategies help ensure reliable Control Valve operation in these challenging environments.
Chemical Processing Industry Standards
The chemical processing industry encompasses a wide range of corrosive environments, each requiring specific material considerations for Control Valve applications. Strong acids, bases, and organic solvents present unique challenges that require careful material selection based on compatibility charts, corrosion testing data, and industry experience. Many chemical processes involve elevated temperatures and pressures that can accelerate corrosion reactions and limit material options. The selection of appropriate Control Valve materials requires comprehensive understanding of the process chemistry, operating conditions, and potential upset conditions that could expose valves to more severe environments than normal operation. Fluorinated compounds and hydrofluoric acid represent particularly challenging environments for Control Valve materials due to their aggressive nature and ability to attack most common engineering materials. Specialized alloys such as Monel, Inconel, and fluoropolymer-lined valves are often required for these applications. The handling of chlorinated organic compounds requires materials that resist both chemical attack and stress corrosion cracking, often necessitating the use of high-nickel alloys or specialized stainless steel grades. Understanding the specific mechanisms of chemical attack helps engineers select appropriate Control Valve materials and design strategies for these challenging applications. Pharmaceutical and biotechnology applications impose additional requirements for Control Valve materials beyond corrosion resistance, including biocompatibility, cleanability, and regulatory compliance. Stainless steel grades 316L and 904L are commonly specified for these applications due to their corrosion resistance and FDA acceptance. The surface finish and design of Control Valve components must facilitate cleaning and sterilization procedures while preventing contamination of the process stream. Specialized surface treatments and electropolishing techniques help achieve the required surface quality for pharmaceutical Control Valve applications.
Power Generation and Utilities Applications
Power generation facilities present diverse corrosive environments for Control Valve applications, ranging from high-temperature steam systems to cooling water circuits and flue gas handling systems. Steam systems require materials that resist high-temperature oxidation, erosion, and potential contaminants in the steam such as chlorides and sulfates. Chrome-moly steels and stainless steels are commonly specified for steam Control Valve applications, with material selection depending on steam temperature, pressure, and purity levels. The design of steam valves must also consider thermal cycling effects and the potential for water hammer conditions that could cause mechanical damage. Cooling water systems in power plants often use seawater, river water, or treated water that can contain various corrosive species including chlorides, sulfates, and biological organisms. The selection of Control Valve materials for cooling water applications requires consideration of water chemistry, temperature, flow velocity, and the presence of biocides or other chemical treatments. Stainless steels, bronze alloys, and specialized corrosion-resistant alloys are commonly used depending on the specific water chemistry and operating conditions. Proper material selection helps prevent fouling, corrosion, and biological growth that could impair Control Valve performance. Flue gas desulfurization (FGD) systems present extremely challenging environments for Control Valve materials due to the presence of sulfur compounds, chlorides, and acidic conditions at elevated temperatures. These systems require specialized materials such as high-nickel alloys, duplex stainless steels, or fiber-reinforced plastic (FRP) materials that can withstand the aggressive chemical environment. The selection of appropriate Control Valve materials for FGD applications requires comprehensive understanding of the specific process chemistry and operating conditions to ensure reliable long-term performance.
Conclusion
The selection of appropriate materials for corrosion resistance in Control Valve applications requires comprehensive analysis of operating conditions, environmental factors, and industry-specific requirements. This evaluation must balance initial material costs against long-term reliability, maintenance requirements, and safety considerations. Modern advances in metallurgy and surface treatments continue to expand the available options for challenging applications, while standardized testing methods and industry guidelines provide frameworks for making informed decisions. Successful Control Valve material selection ultimately depends on understanding the specific corrosion mechanisms involved and selecting materials that provide adequate resistance while meeting performance and economic requirements.
As a leading China Control Valve factory, CEPAI Group leverages decades of expertise in material science and valve engineering to provide optimal solutions for corrosive environments. Our comprehensive range of corrosion-resistant Control Valve options, manufactured in our state-of-the-art facilities, ensures reliable performance across diverse industrial applications. Whether you're seeking a trusted China Control Valve supplier for challenging chemical processing applications or a reliable China Control Valve manufacturer for offshore oil and gas projects, our technical team provides expert guidance in material selection and valve design.
Our commitment to quality and innovation, backed by extensive certifications and testing capabilities, positions CEPAI as your preferred China Control Valve wholesale partner. From standard Control Valve for sale options to custom-engineered solutions, we deliver exceptional value through superior materials, precision manufacturing, and comprehensive technical support. For detailed specifications, competitive Control Valve price information, or to request our comprehensive Control Valve brochure, please contact our technical sales team at cepai@cepai.com. Let our expertise in corrosion-resistant materials help you achieve optimal performance and reliability in your most challenging applications.
References
1. Fontana, Mars G. "Corrosion Engineering: Principles and Practice." 4th Edition. Materials Engineering Series, McGraw-Hill Education, 2018.
2. Davis, Joseph R. "Corrosion of Weldments." ASM International Handbook Series, Materials Park, Ohio, 2019.
3. Ahmad, Zaki. "Principles of Corrosion Engineering and Corrosion Control." Elsevier Science & Technology, Butterworth-Heinemann, 2020.
4. Revie, R. Winston and Uhlig, Herbert H. "Corrosion and Corrosion Control: An Introduction to Corrosion Science and Engineering." 5th Edition, John Wiley & Sons, 2017.

Get professional pre-sales technical consultation and valve selection services, customized solution services.
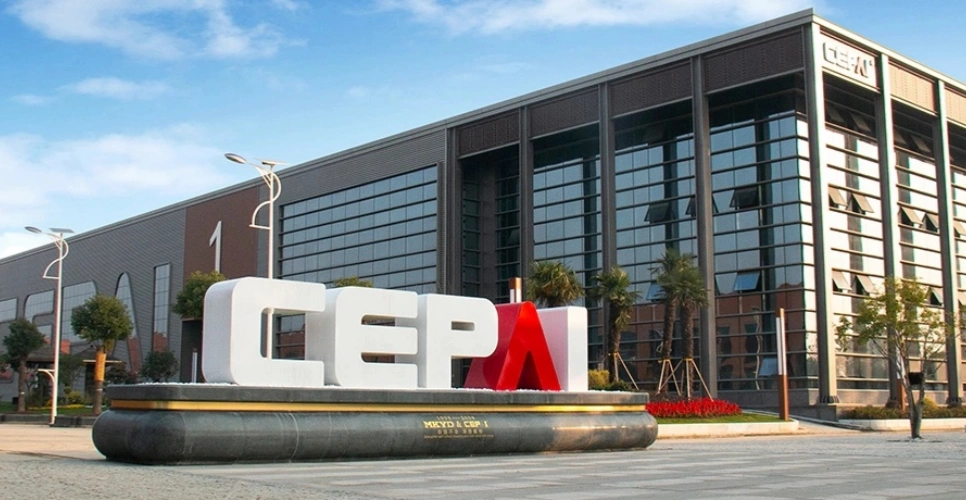
About CEPAI