Dealing with Pressure Surges in Valve Design
Pressure surges represent one of the most critical challenges in modern industrial valve applications, particularly in oil and gas, petrochemical, and power generation facilities. These sudden pressure fluctuations can cause catastrophic system failures, equipment damage, and safety hazards if not properly managed through sophisticated valve design principles. Understanding how to effectively address pressure surges through advanced Control Valve engineering is essential for maintaining system integrity, operational efficiency, and personnel safety. Modern valve manufacturers must integrate multiple design strategies, from material selection and geometric optimization to advanced flow control mechanisms, ensuring their products can withstand extreme pressure variations while maintaining precise control performance across diverse industrial applications.
Understanding Pressure Surge Mechanisms in Industrial Applications
Hydraulic Transients and Water Hammer Effects
Hydraulic transients, commonly known as water hammer effects, occur when fluid velocity changes rapidly within piping systems, creating pressure waves that propagate throughout the network. These phenomena are particularly prevalent in systems utilizing Control Valve assemblies for flow regulation, where sudden valve closure or opening can generate significant pressure spikes. The magnitude of these pressure surges depends on several factors including fluid velocity, pipe characteristics, system configuration, and valve operating speed. Modern industrial facilities must account for these transient conditions during system design phases to prevent equipment failure and ensure operational safety. The mathematical relationship governing pressure surge magnitude follows the Joukowsky equation, where pressure increase equals the product of fluid density, wave speed, and velocity change. In practical applications, this means that high-velocity systems with rapid valve actuation can experience pressure surges exceeding several times normal operating pressure. Control Valve designers must therefore incorporate features such as variable opening speeds, soft-seated designs, and pressure relief mechanisms to mitigate these effects. Advanced computational fluid dynamics modeling now enables engineers to predict and analyze transient behavior during valve design phases, allowing for optimization of internal geometries and operating characteristics to minimize surge generation while maintaining required control performance specifications.
Cavitation-Induced Pressure Fluctuations
Cavitation represents another critical mechanism contributing to pressure surge generation in valve systems, occurring when local fluid pressure drops below vapor pressure, creating vapor bubbles that subsequently collapse violently when pressure recovers. This phenomenon is particularly problematic in Control Valve applications where high-velocity jets and pressure reduction stages create ideal conditions for cavitation inception. The collapse of cavitation bubbles generates intense pressure pulses that can exceed 10,000 psi locally, causing severe damage to valve internals and creating system-wide pressure disturbances. Modern Control Valve designs incorporate sophisticated anti-cavitation features including staged pressure reduction, flow conditioning elements, and specialized trim geometries to prevent cavitation occurrence. Multi-stage pressure letdown systems distribute pressure drops across multiple restriction points, ensuring that local pressures remain above critical cavitation thresholds throughout the valve. Advanced materials such as stellite-faced components and ceramic coatings provide enhanced resistance to cavitation damage when complete elimination is not feasible. Predictive cavitation analysis using computational fluid dynamics enables designers to optimize valve geometries for specific applications, ensuring reliable operation across the full range of process conditions while maintaining precise control characteristics.
Thermal Shock and Rapid Temperature Changes
Thermal shock conditions create unique challenges for Control Valve systems, particularly in applications involving rapid temperature changes that can induce significant pressure variations through thermal expansion and contraction effects. Steam systems, cryogenic applications, and high-temperature processes frequently experience these conditions, requiring specialized valve designs capable of accommodating thermal stresses while maintaining leak-tight performance. The interaction between thermal effects and mechanical stresses can amplify pressure surge magnitudes, creating complex loading conditions that standard valve designs may not adequately address. Control Valve manufacturers must consider thermal expansion coefficients, material compatibility, and stress concentration factors when designing valves for thermal shock applications. Advanced materials such as duplex stainless steels, nickel-based alloys, and specialized coatings provide enhanced thermal cycling resistance while maintaining mechanical integrity under extreme conditions. Flexible connection designs, expansion joints, and thermal barrier coatings help isolate valve components from severe thermal gradients, reducing stress concentrations and extending service life. Computational thermal-structural analysis enables optimization of valve geometries and material selection for specific thermal environments, ensuring reliable operation throughout expected service conditions.
Advanced Design Strategies for Surge Mitigation
Multi-Stage Pressure Reduction Systems
Multi-stage pressure reduction represents the most effective approach for managing extreme pressure differentials while minimizing surge generation in Control Valve applications. This design philosophy distributes total pressure drop across multiple restriction stages, ensuring that velocity increases and pressure gradients remain within acceptable limits at each stage. Advanced multi-stage designs incorporate variable geometry trim elements, allowing for optimization of pressure distribution based on specific operating conditions and flow requirements. The implementation of multi-stage Control Valve systems requires careful consideration of inter-stage volumes, flow conditioning elements, and pressure recovery characteristics. Each stage must be designed to operate within its optimal performance envelope while contributing to overall system surge mitigation objectives. Modern computational fluid dynamics tools enable detailed analysis of inter-stage flow patterns, pressure distributions, and velocity profiles, allowing designers to optimize stage configurations for maximum effectiveness. Adjustable trim designs permit field optimization of pressure distribution, accommodating variations in process conditions and system requirements without requiring valve replacement. Progressive pressure reduction through multiple stages also provides enhanced process control capabilities, allowing for finer regulation of downstream conditions and improved system response characteristics. Control Valve systems incorporating intelligent multi-stage designs can automatically adjust pressure distribution based on operating conditions, optimizing performance while minimizing surge generation. This adaptive capability is particularly valuable in applications with varying process conditions, where fixed-geometry designs may not provide optimal performance across the full operating range.
Dynamic Response Optimization and Actuator Integration
The dynamic response characteristics of Control Valve systems play a crucial role in surge mitigation, with actuator selection, sizing, and control algorithm optimization directly affecting pressure transient generation. Modern electric and pneumatic actuators offer precise control over valve positioning speed and acceleration profiles, enabling implementation of surge-minimizing operating strategies. Variable-speed actuation capabilities allow valves to open and close at rates optimized for specific system conditions, reducing pressure surge magnitudes while maintaining required control performance. Advanced Control Valve actuator systems incorporate feedback control algorithms that monitor system pressure and automatically adjust valve positioning rates to minimize transient generation. These intelligent systems can detect developing surge conditions and modify valve operation in real-time, preventing potentially damaging pressure excursions. Integration with plant-wide control systems enables coordinated valve operation strategies that consider system-wide effects and optimize overall performance rather than individual valve characteristics. Predictive control algorithms utilize system modeling and real-time data to anticipate surge-generating conditions and proactively adjust Control Valve operation to prevent their occurrence. Machine learning techniques enable continuous optimization of control strategies based on historical performance data and changing system characteristics. These advanced capabilities represent the future of surge mitigation technology, offering unprecedented levels of system protection and performance optimization through intelligent valve operation strategies.
Advanced Materials and Manufacturing Technologies
The selection of appropriate materials and manufacturing processes is fundamental to creating Control Valve systems capable of withstanding extreme pressure surge conditions while maintaining long-term reliability and performance. Advanced metallurgy techniques, including powder metallurgy, additive manufacturing, and specialized heat treatments, enable production of valve components with superior mechanical properties and fatigue resistance. These manufacturing advances allow for creation of complex internal geometries optimized for flow control and surge mitigation that would be impossible using conventional manufacturing methods. Specialized alloy systems, including duplex stainless steels, nickel-based superalloys, and titanium alloys, provide enhanced strength-to-weight ratios and superior corrosion resistance in demanding applications. Control Valve components manufactured from these advanced materials exhibit improved fatigue life and resistance to pressure cycling effects, ensuring reliable operation throughout extended service periods. Surface enhancement techniques such as shot peening, laser hardening, and specialized coatings further improve component durability and resistance to wear and corrosion effects. Additive manufacturing technologies enable production of Control Valve internal components with optimized flow passages and integrated features that improve surge mitigation performance. These manufacturing capabilities allow for creation of complex three-dimensional geometries that provide superior flow conditioning and pressure distribution characteristics compared to conventionally manufactured components. The ability to integrate multiple functions into single components reduces assembly complexity while improving performance and reliability characteristics.
Implementation Best Practices and System Integration
Comprehensive System Analysis and Design Optimization
Effective pressure surge mitigation requires comprehensive analysis of entire piping systems rather than isolated Control Valve considerations, as surge propagation and amplification effects depend heavily on system configuration, pipe routing, and component interactions. Modern system analysis techniques utilize advanced computational fluid dynamics modeling to predict transient behavior and optimize valve placement, sizing, and operating strategies for maximum surge mitigation effectiveness. These analyses consider factors including pipe diameter variations, fitting losses, elevation changes, and fluid properties to develop accurate models of system dynamic behavior. Control Valve selection and configuration must be optimized based on comprehensive system analysis results, considering not only steady-state performance requirements but also transient behavior characteristics. This holistic approach ensures that valve designs complement overall system surge mitigation strategies rather than creating additional sources of pressure disturbances. Integration of surge analysis results with valve selection criteria enables specification of optimal valve characteristics for each application, maximizing both control performance and surge mitigation effectiveness. Advanced system modeling capabilities enable evaluation of various surge mitigation strategies, including surge tank sizing, pipe routing optimization, and Control Valve operating procedure development. These tools allow engineers to compare alternative design approaches and select optimal configurations based on comprehensive performance criteria including capital costs, operating expenses, reliability considerations, and maintenance requirements. The ability to predict system behavior under various operating scenarios enables development of robust designs that perform effectively across the full range of expected conditions.
Real-Time Monitoring and Predictive Maintenance
Implementation of comprehensive monitoring systems enables real-time detection of developing surge conditions and provides early warning of potential equipment problems before catastrophic failures occur. Modern Control Valve installations incorporate advanced sensor technologies including pressure transducers, accelerometers, acoustic emission detectors, and flow measurement devices to continuously monitor system performance and detect anomalous conditions. These monitoring systems provide valuable data for optimizing valve operation strategies and identifying maintenance requirements before performance degradation becomes critical. Predictive maintenance algorithms analyze monitoring data to identify trends and patterns that indicate developing problems with Control Valve systems or associated equipment. Machine learning techniques enable development of sophisticated fault detection algorithms that can distinguish between normal operational variations and conditions that may lead to equipment failure. These capabilities allow maintenance activities to be scheduled based on actual equipment condition rather than arbitrary time intervals, improving reliability while reducing maintenance costs. Integration of monitoring data with plant-wide control systems enables automatic adjustment of Control Valve operation strategies based on changing system conditions and performance characteristics. This adaptive capability ensures optimal performance throughout equipment service life while minimizing surge generation and associated system stresses. Real-time optimization of valve operation based on current system conditions represents the ultimate goal of intelligent surge mitigation systems.
Training and Operational Procedures
Effective surge mitigation requires comprehensive training programs for operations and maintenance personnel, ensuring that they understand the principles of surge generation and the importance of proper Control Valve operation procedures. Training programs must cover both theoretical aspects of surge phenomena and practical operational techniques for minimizing surge generation during normal and emergency operating conditions. Regular refresher training ensures that personnel maintain current knowledge of best practices and newly developed mitigation techniques. Operational procedures must be developed specifically for each Control Valve application, considering unique system characteristics and potential surge generation scenarios. These procedures should specify proper valve operation sequences, emergency shutdown procedures, and maintenance requirements to ensure optimal surge mitigation performance throughout equipment service life. Documentation of operating procedures and their technical basis provides valuable reference material for operations personnel and supports consistent implementation of best practices. Emergency response procedures must address potential surge-related incidents, including equipment failure modes, system isolation requirements, and recovery strategies. Control Valve systems should be designed with appropriate isolation capabilities and emergency operating procedures to minimize consequences of surge-related failures and enable rapid system recovery. Regular emergency response training ensures that personnel can respond effectively to surge-related incidents when they occur.
Conclusion
Dealing with pressure surges in valve design requires a comprehensive approach that integrates advanced engineering principles, sophisticated materials technology, and intelligent control strategies. Modern Control Valve systems must be designed to withstand extreme pressure variations while maintaining precise control performance across diverse industrial applications. The implementation of multi-stage pressure reduction, dynamic response optimization, and advanced materials technology provides effective solutions for managing surge-related challenges in demanding industrial environments.
Ready to enhance your system's pressure surge protection? As a leading China Control Valve factory and trusted China Control Valve supplier, CEPAI Group offers cutting-edge solutions engineered for extreme conditions. Our China Control Valve manufacturer capabilities include custom designs optimized for surge mitigation applications. Whether you need China Control Valve wholesale solutions or individual units, we provide comprehensive Control Valve for sale options with competitive Control Valve price structures. Request your detailed Control Valve brochure today to discover how our advanced engineering capabilities can protect your critical systems. Contact our technical specialists at cepai@cepai.com for personalized consultation and surge mitigation solutions tailored to your specific requirements.
References
1. Thorley, A.R.D., "Fluid Transients in Pipeline Systems: A Guide to the Control and Suppression of Fluid Transients in Liquids in Closed Conduits," Professional Engineering Publishing, 2004.
2. Wylie, E.B. and Streeter, V.L., "Fluid Transients in Systems," Prentice Hall Civil Engineering and Engineering Mechanics Series, 1993.
3. Tullis, J.P., "Hydraulics of Pipelines: Pumps, Valves, Cavitation, Transients," John Wiley & Sons, 1989.
4. Chaudhry, M.H., "Applied Hydraulic Transients," Van Nostrand Reinhold Company, 1987.

Get professional pre-sales technical consultation and valve selection services, customized solution services.
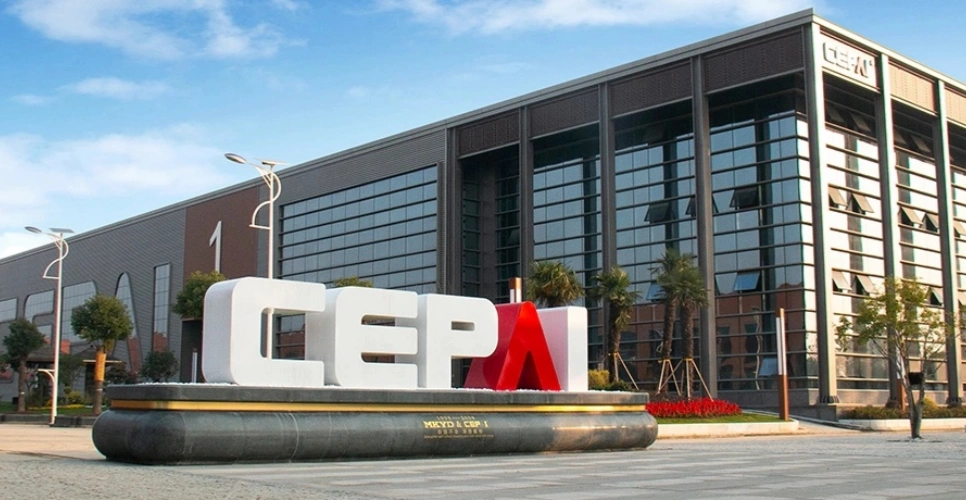
About CEPAI