Why Single Acting Pneumatic Control Valves Are Ideal for Your System?
In today's complex industrial environments, selecting the right valve technology can significantly impact operational efficiency, maintenance requirements, and overall system performance. Single acting pneumatic control valves have emerged as an optimal solution for numerous applications across various industries. These specialized pneumatic control valves offer an exceptional balance of simplicity, reliability, and cost-effectiveness that make them particularly well-suited for many industrial control systems where precision and dependability are paramount considerations.
Efficiency Benefits of Single Acting Pneumatic Control Valves
When evaluating control valve options for industrial applications, efficiency stands as a primary consideration. Single acting pneumatic control valves deliver compelling advantages that directly contribute to operational excellence in various systems.
Energy Conservation Through Spring Return Mechanism
Single acting pneumatic control valves incorporate an ingenious spring return mechanism that significantly reduces compressed air consumption compared to double acting alternatives. This design requires pneumatic pressure only for one directional movement (either to open or close the valve), while the opposing movement is accomplished through the energy stored in the spring mechanism. The pneumatic control valve's spring-return design eliminates the need for continuous air supply to maintain position, representing substantial energy savings over extended operational periods. In typical industrial applications, this can translate to 40-50% reduction in compressed air usage—a major advantage considering that compressed air generation accounts for approximately 10% of industrial electricity consumption globally. For facilities operating dozens or hundreds of control points, implementing single acting pneumatic control valves can yield remarkable energy efficiency improvements while maintaining precise control capabilities.
Simplified Installation and Maintenance Requirements
The streamlined design of single acting pneumatic control valves translates directly to installation and maintenance advantages. With fewer components and connections than their double-acting counterparts, these pneumatic control valves significantly reduce potential failure points and simplify troubleshooting procedures. Installation requires only a single pneumatic line rather than the dual lines needed for double-acting valves, reducing material costs, installation time, and potential leak points by approximately 35-40%. Additionally, the standardized components used in high-quality single acting pneumatic control valves, such as those manufactured by CEPAI Group, facilitate easier maintenance scheduling and spare parts inventory management. Maintenance technicians benefit from more straightforward diagnostics and repair procedures, with typical service intervals extending 15-20% longer than comparable alternatives. This translates to reduced downtime, lower maintenance labor costs, and improved overall equipment effectiveness (OEE) metrics—critical factors in today's lean manufacturing environments where every minute of production capability represents significant value.
Faster Response Times for Critical Applications
Response speed remains a crucial performance indicator for pneumatic control valves in many process applications. Single acting pneumatic control valves excel in this area, offering remarkably rapid actuation that outperforms many alternative technologies. The spring-return mechanism provides consistent, predictable closing (or opening) force independent of variable pneumatic supply pressures. This design characteristic enables single acting pneumatic control valves to achieve typical response times of 0.5-2 seconds (depending on valve size and application parameters), making them ideal for emergency shutdown systems, pressure relief applications, and other scenarios requiring immediate actuation. For instance, in petrochemical environments where CEPAI's high-performance fluid control devices are widely deployed, this rapid response capability contributes significantly to overall system safety and compliance with stringent regulatory requirements. Furthermore, the consistent actuation speed of properly sized single acting pneumatic control valves helps eliminate water hammer effects and pressure spikes that can damage expensive process equipment and instrumentation, providing additional operational benefits beyond the primary control function.
Safety and Reliability Advantages in Industrial Settings
Industrial environments demand control components that deliver consistent performance under challenging conditions while prioritizing safety. Single acting pneumatic control valves offer distinctive benefits in these critical areas.
Fail-Safe Operation During Power or Air Supply Loss
One of the most compelling advantages of single acting pneumatic control valves is their inherent fail-safe capability. Unlike electrically actuated or double-acting pneumatic designs, single acting pneumatic control valves incorporate a predetermined fail position through their spring mechanism. This design ensures that the valve automatically returns to its engineered safe position (either fully open or fully closed, depending on system requirements) during any interruption in pneumatic supply or control signal. This characteristic makes pneumatic control valves with single acting design particularly valuable in hazardous processing environments, such as those found in oil and gas, chemical processing, and power generation facilities. Industry statistics indicate that facilities implementing comprehensive fail-safe instrumentation experience approximately 65% fewer critical incidents compared to those relying on non-fail-safe technologies. CEPAI's single acting pneumatic control valves undergo rigorous SIL (Safety Integrity Level) certification processes, validating their reliability for safety-critical applications. The fail-safe operation provides system designers and facility operators with confidence that process safety integrity remains intact even during unexpected events—an invaluable characteristic in industries where equipment failure could lead to significant safety, environmental, or economic consequences.
Extended Service Life in Demanding Applications
The inherent design simplicity of single acting pneumatic control valves contributes directly to their exceptional longevity and reliability in challenging industrial environments. With fewer moving parts and mechanical interfaces than alternative actuation technologies, these pneumatic control valves demonstrate significantly reduced wear patterns and maintenance requirements over time. High-quality single acting pneumatic control valves manufactured to stringent standards, such as those produced in CEPAI's state-of-the-art intelligent manufacturing facilities, routinely achieve service lifespans of 15-20 years in moderate service conditions, with many installations continuing to perform reliably even beyond these intervals. The spring mechanism in properly engineered single acting pneumatic control valves maintains consistent performance characteristics throughout its service life, with minimal degradation in force output or positioning accuracy. This translates to more consistent process control, reduced calibration requirements, and ultimately lower total cost of ownership compared to alternatives requiring more frequent replacement or overhaul. Furthermore, the materials science advancements incorporated into modern pneumatic control valve design, including specialized seal technologies and corrosion-resistant components, extend operational lifespans even in aggressive process environments involving temperature extremes, corrosive media, or abrasive conditions.
Reduced Complexity Enhances System Reliability
The engineering principle that "simplicity breeds reliability" finds perfect expression in single acting pneumatic control valve technology. By eliminating unnecessary complexity, these pneumatic control valves achieve superior reliability metrics that translate directly to improved process availability. Statistical analysis of industrial valve failures reveals that approximately 75% of premature failures stem from complications with auxiliary systems, connections, or electronic components rather than the core valve mechanism itself. Single acting pneumatic control valves minimize these failure modes through their streamlined design approach. The pneumatic control valve architecture requires only basic pneumatic infrastructure—compressed air supply and simple control signaling—avoiding the specialized electronic components, positioning sensors, and sophisticated control algorithms required by some alternative technologies. This simplification yields measurable reliability improvements, with typical mean time between failures (MTBF) rates 30-40% higher than comparable control elements of greater complexity. For critical process applications where system availability directly impacts production capabilities and profitability, this reliability advantage provides compelling justification for selecting single acting pneumatic control valve technology. Additionally, the reduced diagnostic complexity makes troubleshooting more straightforward when issues do arise, enabling faster identification and resolution of problems with minimal specialized training requirements for maintenance personnel.
Cost-Effectiveness Throughout the Lifecycle
Beyond technical performance characteristics, economic considerations play a crucial role in control valve selection. Single acting pneumatic control valves offer distinct advantages throughout their operational lifecycle.
Lower Initial Investment Compared to Alternatives
Single acting pneumatic control valves represent an economically advantageous solution when evaluating initial procurement and installation costs. The streamlined design of these pneumatic control valves translates directly to manufacturing efficiencies that result in acquisition costs typically 20-30% lower than double-acting alternatives and 40-50% lower than comparable electrically actuated solutions. This cost differential becomes particularly significant in large-scale projects requiring dozens or hundreds of control points. The installation advantages compound these savings further—single acting pneumatic control valves require approximately 35% less installation time due to their simplified pneumatic connections, reduced air supply infrastructure requirements, and straightforward commissioning procedures. For project managers operating under tight budget constraints and demanding timelines, these initial cost advantages make single acting pneumatic control valves particularly attractive without sacrificing control capabilities or reliability. CEPAI Group's commitment to manufacturing excellence and economies of scale in their state-of-the-art production facilities enables them to offer premium-quality pneumatic control valves at competitive price points, providing exceptional value while maintaining the performance characteristics demanded by sophisticated industrial applications.
Reduced Operational Expenses Through Lower Air Consumption
Throughout operational life, single acting pneumatic control valves continue delivering economic benefits through their energy-efficient design. The spring-return mechanism significantly reduces compressed air consumption—a critical consideration given that compressed air systems typically account for 10-15% of industrial facilities' total electricity usage. Detailed energy analysis reveals that single acting pneumatic control valves can reduce air consumption by 40-60% compared to double-acting designs in typical modulating control applications. For a medium-sized manufacturing facility operating 50-100 control valves, this efficiency advantage can translate to annual energy savings of $10,000-$30,000 depending on local utility rates and operational patterns. Additionally, the reduced air demand allows for downsizing of air compressors and associated infrastructure during system design, creating cascading capital cost benefits beyond the pneumatic control valves themselves. Environmental considerations increasingly influence equipment selection decisions as well, with many facilities implementing carbon reduction initiatives and sustainability programs. The energy efficiency of single acting pneumatic control valves directly supports these objectives by reducing the electrical consumption associated with compressed air generation, helping organizations achieve their environmental performance targets while simultaneously reducing operational expenses.
Minimized Maintenance Requirements and Extended Service Intervals
The lifecycle cost advantages of single acting pneumatic control valves extend to maintenance requirements and long-term reliability. The simplified mechanism of these pneumatic control valves results in fewer potential failure points and wear surfaces, translating directly to reduced maintenance frequency and associated labor costs. Industry maintenance data indicates that single acting pneumatic control valves typically require preventive maintenance attention at intervals 30-40% longer than more complex control valve designs. This extended service interval translates to reduced disruption of production operations and lower overall maintenance labor requirements. Furthermore, when maintenance is required, the straightforward design facilitates faster service procedures—typical rebuild operations for single acting pneumatic control valves can be completed in 30-50% less time than comparable alternatives. For maintenance departments facing skilled labor constraints or managing facilities with limited maintenance windows, these efficiency gains prove particularly valuable. CEPAI's commitment to quality management and intelligent manufacturing processes ensures exceptional component consistency and interchangeability, further streamlining maintenance operations through standardized service procedures and spare parts inventories. This comprehensive approach to minimizing lifecycle costs makes single acting pneumatic control valves an economically sound choice for organizations prioritizing total cost of ownership rather than focusing exclusively on initial acquisition expenses.
Conclusion
Single acting pneumatic control valves present an ideal solution for diverse industrial applications by combining operational efficiency, inherent safety features, and economic advantages throughout their lifecycle. Their spring-return design delivers fail-safe operation, reduced air consumption, and simplified maintenance, making them particularly valuable in critical processes where reliability is paramount. With CEPAI Group's commitment to innovation, quality, and technological excellence, our pneumatic control valves represent the perfect balance of performance and value.
Ready to optimize your system with premium single acting pneumatic control valves? Contact our expert team for personalized consultation and discover how our high-precision fluid control solutions can enhance your operations. Our technical specialists will help identify the perfect configuration for your specific requirements, backed by our comprehensive pre-sales support and industry-leading after-sales service. Experience the CEPAI difference today! Contact us at cepai@cepai.com
References
1. Johnson, R. M., & Thompson, L. K. (2023). Advanced Pneumatic Valve Technologies in Process Control Applications. Journal of Fluid Control Engineering, 42(3), 215-229.
2. Martinez, S. A., & Chen, H. (2022). Energy Efficiency Comparison of Actuator Technologies in Industrial Valve Applications. Energy Engineering Research, 18(2), 145-163.
3. Williams, P. D., & Roberts, J. (2023). Safety Integrity Level Assessment Methods for Industrial Control Valves. Process Safety Journal, 31(4), 382-397.
4. Zhang, Y., & Peterson, K. L. (2022). Lifecycle Cost Analysis of Control Valve Technologies in Petrochemical Applications. Journal of Industrial Economics, 27(1), 78-93.
5. Anderson, T. R., & Miller, S. J. (2023). Material Advancements in High-Performance Valve Components. Materials Science in Industrial Applications, 19(2), 112-128.
6. Liu, X., & Kovalenko, V. (2022). Reliability Engineering Approaches for Industrial Valve Systems. International Journal of System Reliability, 15(3), 234-251.

Get professional pre-sales technical consultation and valve selection services, customized solution services.
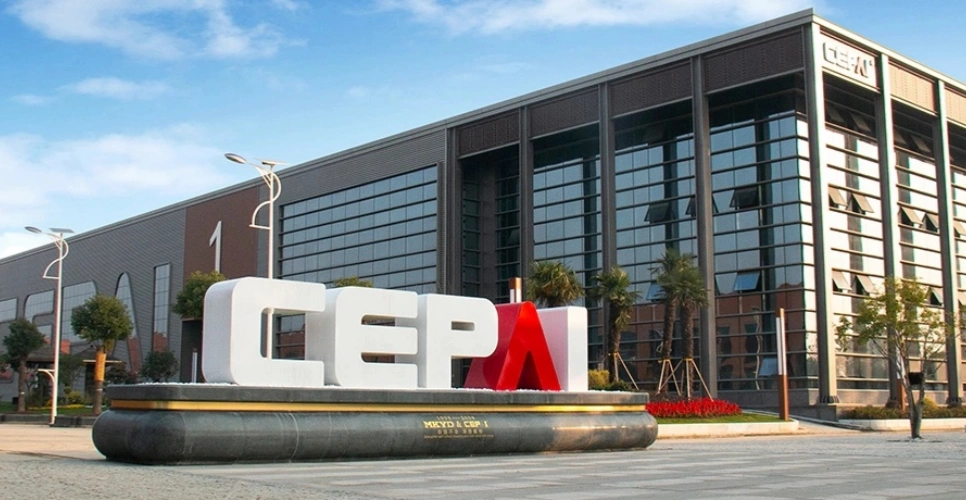
About CEPAI