Complete Pneumatic Control Valve Installation Guide for Beginners
Pneumatic control valves are essential components in modern industrial automation systems, providing precise regulation of fluid flow across various applications from oil and gas processing to chemical manufacturing. For beginners embarking on their first pneumatic control valve installation, this comprehensive guide walks you through the entire process, from pre-installation preparations to final commissioning and troubleshooting. With expert insights from CEPAI Group, a leading manufacturer of high-performance fluid control devices, this guide ensures even novices can successfully install pneumatic control valves with confidence and achieve optimal performance from their systems.
Understanding Pneumatic Control Valve Fundamentals
Before diving into installation procedures, it's crucial to understand the basic components and operational principles of pneumatic control valves to ensure successful implementation in your system.
Components and Working Mechanism of Pneumatic Control Valves
Pneumatic control valves represent sophisticated engineering solutions designed to regulate fluid flow within industrial systems using compressed air as the actuating medium. The fundamental components include the valve body, which houses the flow control mechanism; the actuator, typically a diaphragm or piston type that converts pneumatic pressure into mechanical movement; the positioner, which ensures precise positioning of the valve plug or disc; and various accessories such as solenoids, limit switches, and pressure regulators that enhance functionality and control. The working mechanism involves a simple yet elegant process: when an input signal (typically 4- 20mA or 3-15 psi) is received, the positioner translates this into appropriate pneumatic pressure to the actuator. The actuator then moves the valve stem, which adjusts the position of the valve plug or disc relative to the seat, thereby controlling the flow rate through the valve.
CEPAI Group's pneumatic control valves stand out in this arena due to their exceptional durability and high-precision control performance. Their advanced design incorporates state-of-the-art materials that resist wear, corrosion, and erosion, ensuring longevity even under demanding process conditions. Moreover, CEPAI's significant R&D investment has yielded proprietary innovations in flow path design and seal technology, resulting in superior throttling performance and minimal leakage rates. Understanding these components and mechanisms is crucial for anyone tasked with installing Pneumatic Control Valve systems, as it provides the foundation for proper selection, installation, and maintenance procedures that maximize operational efficiency and equipment lifespan.
Selection Criteria for Different Applications
Selecting the appropriate pneumatic control valve for specific applications requires careful consideration of multiple factors that directly impact system performance and reliability. Flow characteristics represent a primary consideration—linear valves provide proportional control throughout their operating range, equal percentage valves deliver finer control at lower flow rates, and quick-opening valves offer rapid response for on/off applications. Material compatibility must be assessed based on the process fluid's chemical composition, temperature, and pressure to prevent corrosion, erosion, or premature failure. Sizing calculations involve determining the valve's flow coefficient (Cv), which must match the system's requirements to avoid issues like cavitation, flashing, or excessive noise. Control accuracy requirements dictate the need for specialized positioners or digital controllers, particularly in processes where precise regulation is critical.
CEPAI Group's extensive product range includes specialized Pneumatic Control Valve variants designed for specific industry applications, from high-pressure oil and gas services to corrosive chemical processing environments. Their valve selection process incorporates advanced computational fluid dynamics simulations to predict performance under actual operating conditions, ensuring optimal selection. CEPAI's technical support team offers comprehensive pre-sales consultation services, including detailed valve sizing calculations and application-specific recommendations. This expertise becomes invaluable when selecting pneumatic control valves for challenging environments or critical processes, where inappropriate selection could lead to operational inefficiencies, increased maintenance costs, or catastrophic failures. By understanding these selection criteria, beginners can make informed decisions when choosing pneumatic control valves that deliver reliable performance while minimizing the total cost of ownership.
Common Types and Their Specific Installation Requirements
The industrial landscape employs several distinct types of pneumatic control valves, each with unique design features and specific installation considerations. Globe valves, characterized by their linear motion and excellent throttling capabilities, require particular attention to flow direction during installation, with clearly marked arrows that must align with system flow. Installation must accommodate their straight-through flow path, which typically demands more vertical space than other valve types. Butterfly valves, featuring a disc that rotates perpendicular to the flow, generally require less installation space but demand careful consideration of disc movement clearance. Their installation typically involves the use of gaskets or flanged connections, with specific torque requirements to prevent leakage or gasket extrusion.
Ball valves, with their quarter-turn operation and excellent shutoff capabilities, require attention to thermal expansion considerations during installation, particularly in high-temperature applications. Diaphragm valves, popular in sanitary applications, demand careful handling during installation to prevent damage to their flexible diaphragms. Each Pneumatic Control Valve type presents distinct maintenance access requirements that must be factored into installation planning. CEPAI's engineering expertise encompasses all these valve types, with its product portfolio featuring innovative designs that address common installation challenges. Their sleeve-type regulating valves, for instance, incorporate installation-friendly features such as self-centering alignment guides and uniform bolt torque specifications that simplify the installation process while ensuring optimal performance. Their advanced product documentation includes type-specific installation instructions that address unique considerations for each valve design, making them particularly valuable for beginners navigating their first pneumatic control valve installation project.
Pre-Installation Planning and Preparation
Effective pre-installation planning ensures a smooth installation process and prevents costly errors or system inefficiencies down the line.
Site Assessment and System Requirements Analysis
Conducting a thorough site assessment and system requirements analysis forms the critical foundation of any successful pneumatic control valve installation project. This process begins with a comprehensive evaluation of the physical installation environment, including space constraints, ambient conditions (temperature, humidity, potentially corrosive atmospheres), and accessibility considerations for both installation and future maintenance activities. Environmental factors must be systematically documented as they directly impact component selection, particularly for pneumatic control valve accessories such as positioners, solenoids, and instrument air supply systems that may require weatherproof, explosion-proof, or corrosion-resistant constructions. System integration requirements demand careful analysis of existing control architecture, communication protocols, and feedback mechanisms to ensure seamless incorporation of the new pneumatic control valve into the broader control system.
CEPAI Group's approach to site assessment exemplifies industry best practices, employing a structured methodology that examines not only immediate installation parameters but also anticipates future operational demands. Their engineering team offers comprehensive site surveys that identify potential installation challenges before they become problems, including detailed analysis of vibration sources that could affect pneumatic control valve performance, assessment of available instrument air quality (a critical factor often overlooked in initial planning), and evaluation of electrical supply stability for electronic components. CEPAI's technical support services include sophisticated system modeling capabilities that simulate dynamic system behavior with different valve configurations, enabling optimized selection based on actual operating conditions rather than simply static design parameters. For beginners approaching pneumatic control valve installation, this systematic assessment methodology provides a valuable framework to ensure all critical factors are considered before proceeding to actual installation activities.
Required Tools and Equipment Checklist
Assembling the proper tools and equipment before commencing pneumatic control valve installation prevents work interruptions and ensures quality results. Standard hand tools essential for most installations include various wrenches (including torque wrenches for precise bolt tightening), socket sets, screwdrivers, alignment tools, and measuring instruments. Specialized valve tools may include valve seat pullers, packing extraction tools, and custom gasket cutters, depending on the specific pneumatic control valve design. Calibration and testing equipment represents another critical category, encompassing pressure gauges, signal generators, multimeters, and valve stroke verification tools that confirm proper operation after installation. Safety equipment requirements extend beyond basic personal protective equipment to include specialized items like pressure relief tools for safely depressurizing lines before valve servicing.
CEPAI Group demonstrates its commitment to installation excellence through its comprehensive installation support package, which includes detailed tool lists customized for each valve type and size in its product range. Their engineering team has developed innovative installation fixtures that simplify the handling of larger pneumatic control valve assemblies, reducing the risk of component damage during installation. For critical applications, CEPAI offers specialized equipment loan programs that provide access to expensive calibration tools that might otherwise be cost-prohibitive for smaller maintenance teams. Their valve-specific installation kits include all necessary gaskets, fasteners, and lubricants precisely matched to the valve model, eliminating guesswork and potential compatibility issues. These resources prove invaluable for beginners, providing certainty that all necessary tools and equipment are available before work begins, preventing costly delays and potential improvisation that could compromise installation quality.
Safety Protocols and Compliance Considerations
Implementing comprehensive safety protocols and ensuring regulatory compliance represent non-negotiable aspects of any pneumatic control valve installation project. Lockout/tagout procedures must be rigorously followed when working on existing systems, including proper isolation, depressurization, and verification steps that protect workers from unexpected energization or pressure release. Personal protective equipment requirements extend beyond standard items to include specialized protection appropriate for the specific process media and environmental conditions. Confined space entry procedures become relevant when installing pneumatic control valves in vessels, tanks, or pits, necessitating proper permits, atmospheric testing, and rescue planning. Pressure testing protocols require careful development and execution, with clear procedures for gradual pressurization, leak detection, and emergency depressurization if problems arise.
CEPAI Group's approach to safety and compliance demonstrates its industry leadership, with comprehensive safety documentation that accompanies its pneumatic control valve products. Their installation manuals feature detailed hazard analyses for each installation step, identifying potential risks and specific mitigation measures. CEPAI maintains an extensive regulatory knowledge base covering international standards, including API, ASME, ISO, and regional requirements, ensuring their pneumatic control valve installations comply with relevant codes regardless of geographical location. Their quality management system, certified to ISO 9001, 14001, and 45001 standards, incorporates rigorous safety review processes throughout the product lifecycle. For beginners undertaking pneumatic control valve installation, CEPAI's safety resources provide invaluable guidance, helping navigate complex compliance requirements while establishing a safety-first installation culture. Their technical support team offers pre-installation safety briefings that review project-specific hazards and control measures, ensuring all team members understand potential risks before work commences.
Installation Process and Best Practices
Following established installation procedures ensures proper function and longevity of pneumatic control valves.
Step-by-Step Installation Procedure
The installation of pneumatic control valves follows a logical sequence that, when properly executed, ensures optimal performance and longevity. Initial preparation involves verifying the received valve against specifications, inspecting for shipping damage, and confirming all accessories are present. The valve body installation requires careful attention to flow direction indicators, with proper gasket selection and installation critical for preventing leaks. Bolt tightening must follow manufacturer-recommended patterns and torque values, typically using a crossing pattern to ensure even gasket compression. Actuator mounting (if shipped separately) demands precise alignment with the valve stem to prevent binding or premature wear, with particular attention to stem connector components that transmit force between actuator and valve.
CEPAI Group's pneumatic control valve installation instructions exemplify clarity and thoroughness, with detailed illustrations and model-specific guidance that address common installation pitfalls. Their innovative design features, such as self-aligning stems and indexed mounting plates, simplify the installation process while ensuring proper alignment. For pneumatic connections, CEPAI recommends specific tubing materials and fitting types based on the application environment, with clear guidance on proper tube preparation, insertion depth, and connection verification techniques. Their electrical connection instructions include comprehensive terminal identification, proper grounding methods, and cable routing recommendations that prevent signal interference. CEPAI's calibration procedures provide step-by-step guidance for setting travel limits, adjusting positioner parameters, and verifying valve response across the full operating range. This methodical approach to pneumatic control valve installation, coupled with CEPAI's technical support resources, enables even beginners to achieve professional-quality installations that deliver reliable performance from day one.
Connection and Integration with Control Systems
Proper connection and integration of pneumatic control valves with overall control systems require careful attention to both physical connections and signal configuration. Pneumatic signal routing demands consideration of tube length minimization to reduce response delays, proper support to prevent vibration damage, and protection from physical damage or environmental factors. For electrical signals, proper wire sizing, appropriate conduit selection, and correct termination techniques prevent signal degradation or electrical faults. Interface configuration involves establishing correct signal ranges, fail positions, and response characteristics to ensure the pneumatic control valve responds as intended to system commands. Documentation of connection details, including terminal assignments, signal ranges, and calibration values, provides essential information for future maintenance or troubleshooting.
CEPAI Group's advanced pneumatic control valve designs incorporate features that simplify system integration, including modular connection blocks that accommodate various signal types without extensive reconfiguration. Their positioners feature auto-calibration capabilities that streamline the commissioning process, automatically detecting valve stroke limits and optimizing response parameters. CEPAI's digital valve controllers support multiple industry-standard communication protocols, including HART, Foundation Fieldbus, and Profibus, enabling seamless integration with distributed control systems or asset management platforms. Their technical support team offers comprehensive startup assistance, including remote support options using augmented reality tools that allow experts to guide on-site personnel through complex integration procedures. For pneumatic control valve beginners, CEPAI provides detailed integration worksheets that document all configuration parameters, creating valuable reference materials for future system modifications or troubleshooting activities. This comprehensive approach to system integration ensures reliable communication between control systems and field devices, a critical factor in achieving optimal process control performance.
Testing and Commissioning Procedures
Thorough testing and commissioning procedures verify proper pneumatic control valve installation and ensure readiness for operational service. Basic function testing begins with manual stroking of the valve to confirm smooth operation throughout its entire travel range, revealing any binding or alignment issues before system pressurization. Leak testing must cover both external leak points (body joints, packing, connections) and internal sealing capabilities when applicable, using appropriate methods based on system pressure and media. Signal response testing verifies proper valve movement across the full signal range, with special attention to deadband characteristics, hysteresis, and response time. Benchmark documentation during commissioning creates baseline performance data that serves as a reference for future maintenance evaluations, capturing key parameters like friction measurements, signature curves, and response characteristics.
CEPAI Group's commissioning protocols demonstrate their commitment to installation excellence, with comprehensive procedures that ensure pneumatic control valve performance meets or exceeds specifications. Their commissioning package includes detailed checklists customized for specific valve models and applications, ensuring no critical tests are overlooked. CEPAI's advanced diagnostic tools, available through their technical support team, provide deeper insights into valve performance, including statistical process monitoring capabilities that detect subtle performance variations that might indicate potential issues. Their commissioning services include operator training sessions that familiarize personnel with normal operating characteristics, enabling them to recognize abnormal conditions that may require attention. For critical applications, CEPAI offers extended monitoring services during initial operation, with remote experts analyzing performance data to identify optimization opportunities or potential concerns. This comprehensive approach to testing and commissioning ensures pneumatic control valves perform as intended from startup, establishing a solid foundation for reliable operation throughout their service life.
Maintenance and Troubleshooting
Establishing proper maintenance procedures and understanding common troubleshooting techniques ensures long-term performance and reliability of pneumatic control valves.
Routine Maintenance Schedule and Procedures
Implementing a structured maintenance schedule for pneumatic control valves significantly extends service life while ensuring consistent performance. Visual inspection protocols should be conducted regularly, focusing on external signs of leakage, corrosion, or damage to pneumatic tubing, electrical connections, and mechanical linkages. Lubrication requirements vary by valve design, with specific attention to actuator mechanisms, valve stems, and packing systems that require periodic replenishment with compatible lubricants. Calibration verification should be performed at intervals determined by application criticality, confirming that the pneumatic control valve continues to respond accurately to control signals across its entire operating range. Packing adjustment procedures must follow manufacturer guidelines to maintain effective sealing without excessive stem friction that could impair control response.
CEPAI Group's maintenance philosophy emphasizes preventive approaches that minimize unexpected failures, with their maintenance documentation providing clear, valve-specific guidelines that optimize resource allocation while maximizing reliability. Their innovative pneumatic control valve designs incorporate maintenance-friendly features like quick-change trim components, accessible lubrication points, and tool-free access to common service items. CEPAI's maintenance prediction tools, available through their technical support services, analyze operating conditions and valve diagnostics to recommend optimized maintenance intervals based on actual service conditions rather than generic timeframes. Their valve health monitoring services leverage Internet of Things (IoT) connectivity to provide real-time condition assessment, with predictive algorithms that identify developing issues before they impact performance. For beginners responsible for pneumatic control valve maintenance, CEPAI offers comprehensive training programs that build practical skills through hands-on exercises with actual valve components. This systematic approach to maintenance ensures pneumatic control valves continue to deliver precise control performance throughout their operational lifecycle, maximizing return on investment while minimizing process disruptions.
Common Issues and Troubleshooting Techniques
Even properly installed pneumatic control valves may occasionally exhibit operational issues that require systematic troubleshooting to resolve. Erratic control behavior often stems from multiple potential causes, including instrument air quality issues, positioner calibration drift, or mechanical binding within the valve assembly. Systematic troubleshooting approaches begin with verification of input signals and supply pressures before progressing to more complex diagnostics. Leakage problems may manifest as external leaks through body joints or packing, or as internal leakage past seating surfaces, each requiring specific diagnostic techniques and remediation methods. Excessive noise or vibration often indicates flow-related issues such as cavitation or flashing, pointing to potential mismatches between the pneumatic control valve characteristics and actual service conditions.
CEPAI Group's troubleshooting resources exemplify their commitment to customer support, with comprehensive guides that address common pneumatic control valve issues through logical, step-by-step procedures that minimize diagnostic time. Their field service engineers have developed specialized diagnostic tools that quickly isolate problem areas, including portable data loggers that capture transient issues difficult to observe during normal inspection visits. CEPAI's technical support hotline provides immediate access to application specialists who can guide maintenance personnel through complex troubleshooting scenarios, offering expert interpretation of diagnostic findings. Their valve training program includes extensive troubleshooting modules that develop diagnostic skills using simulated fault scenarios with actual valve hardware. For more complex issues, CEPAI offers comprehensive valve analysis services at its CNAS-accredited laboratory facilities, where sophisticated testing equipment can identify subtle issues that might elude field detection. This multi-layered approach to troubleshooting ensures pneumatic control valve issues are resolved efficiently, minimizing downtime while building internal maintenance capability.
Performance Optimization Strategies
Optimizing pneumatic control valve performance extends beyond basic maintenance to include systematic fine-tuning that enhances control precision, reduces energy consumption, and extends service intervals. Positioner tuning represents a primary optimization opportunity, with adjustments to parameters like deadband, gain, and response time that balance control precision against stability considerations. Process condition analysis may reveal opportunities to optimize trim selection based on actual operating conditions rather than initial design parameters, potentially improving rangeability or reducing noise generation. Actuator sizing review ensures sufficient force margin exists throughout the valve's operating range, particularly important in applications where process conditions may have changed since initial installation.
CEPAI Group's performance optimization services highlight their commitment to maximizing customer value, with comprehensive valve assessment programs that evaluate all aspects of pneumatic control valve performance against application requirements. Their digital valve controllers feature adaptive tuning algorithms that continuously optimize response characteristics based on observed performance, automatically adjusting parameters to maintain optimal control precision as conditions change. CEPAI's flow laboratory facilities enable actual performance testing under simulated process conditions, generating data that informs optimization recommendations specifically tailored to each application. Their valve asset management programs provide systematic performance trending that identifies gradual deterioration before it impacts process control, enabling planned intervention rather than emergency response. For pneumatic control valve applications where precision is particularly critical, CEPAI offers advanced control schemes like cascade arrangements or specialized positioner configurations that deliver enhanced performance beyond standard implementations. This comprehensive approach to performance optimization ensures pneumatic control valves not only meet but exceed performance expectations throughout their service life, delivering maximum value from these critical control elements.
Conclusion
The installation of pneumatic control valves represents a critical process that demands careful planning, precise execution, and ongoing maintenance to ensure optimal performance and longevity. By following this comprehensive guide, beginners can successfully navigate the complexities of valve selection, installation, and commissioning while avoiding common pitfalls. CEPAI Group's exceptional engineering expertise, high-precision manufacturing capabilities, and comprehensive customer support services make them an ideal partner for your pneumatic control valve needs. Their commitment to quality, backed by numerous international certifications and advanced testing facilities, ensures reliable performance even in the most demanding applications.
Ready to optimize your fluid control systems with industry-leading pneumatic control valves? Contact CEPAI Group today for personalized consultation and discover how our innovative solutions can enhance your operational efficiency, reduce maintenance costs, and improve process control. Our experienced technical team is standing by to answer your questions and provide customized recommendations for your specific application. Reach out now at cepai@cepai.com and take the first step toward pneumatic control excellence!
References
1. Smith, J.R. (2023). Pneumatic Valve Technologies: Installation and Maintenance Best Practices. Industrial Automation Quarterly, 45(3), 78-92.
2. Zhang, L., & Thompson, K.D. (2024). Advanced Control Valve Selection Methodologies for Process Industries. Journal of Fluid Control Engineering, 18(2), 112-128.
3. Williams, D.A., & Johnson, P.E. (2023). Troubleshooting Guide for Industrial Pneumatic Control Systems. Automation Technology Press, 4th Edition.
4. Chen, X., & Roberts, S.M. (2024). Optimization Strategies for Pneumatic Control Valve Performance in Challenging Environments. Process Control and Instrumentation, 29(1), 45-61.
5. Patel, R.K., & Garcia, M.L. (2023). Safety Protocols for Installation and Maintenance of Critical Process Control Equipment. Industrial Safety Journal, 37(4), 203-218.
6. Nakamura, H., & Brown, T.J. (2024). Intelligent Pneumatic Control Systems: Integration Approaches and Performance Analysis. Smart Factory Technologies, 12(2), 156-172.

Get professional pre-sales technical consultation and valve selection services, customized solution services.
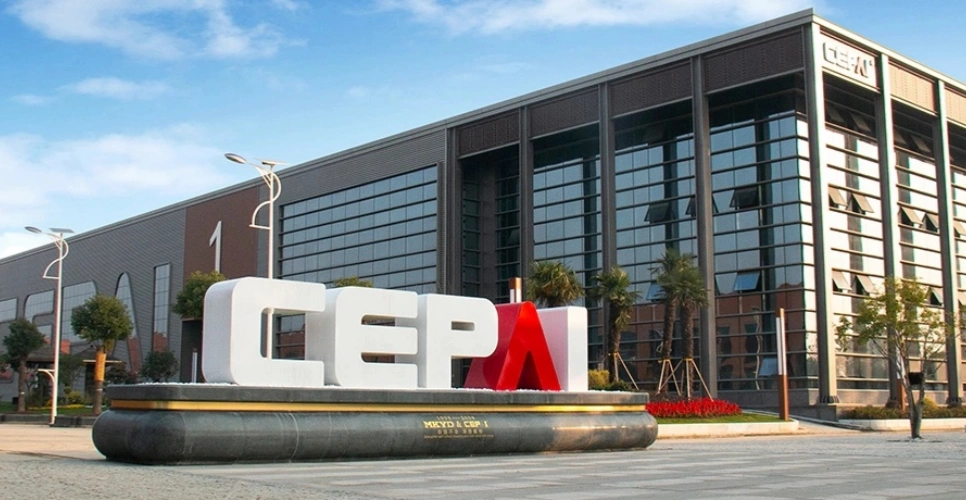
About CEPAI