What is the difference between pneumatic and electric control valves?
Control valves serve as the backbone of industrial automation systems, regulating fluid flow, pressure, and temperature across countless applications. Understanding the fundamental differences between pneumatic and electric control valves is crucial for engineers, procurement professionals, and facility managers making critical infrastructure decisions. An Electric Control Valve utilizes electrical actuators for precise positioning and control, while pneumatic systems rely on compressed air pressure for operation. These two technologies represent distinct approaches to process control, each offering unique advantages in terms of response time, precision, safety, and maintenance requirements. The choice between pneumatic and electric actuation significantly impacts system performance, operational costs, and long-term reliability in industrial applications.
Key Operational Differences Between Pneumatic and Electric Control Systems
Power Source and Energy Requirements
Pneumatic control valves derive their operating power from compressed air systems, typically requiring air pressures ranging from 20 to 100 PSI for standard applications. The compressed air system includes compressors, air treatment equipment, distribution networks, and storage tanks, creating a comprehensive infrastructure requirement. Electric Control Valve systems, conversely, utilize electrical power supplies ranging from 24V DC to 480V AC, depending on the specific application and actuator size. The electrical infrastructure is generally more straightforward to install and maintain, requiring only appropriate electrical connections and control circuits. Pneumatic systems consume continuous compressed air even during static positions, while electric actuators only consume power during valve movement, making them more energy-efficient for applications requiring frequent positioning changes. The energy efficiency consideration becomes particularly significant in facilities with high operational costs or environmental sustainability goals.
Response Time and Control Precision
The response characteristics of pneumatic and electric control valves differ substantially due to their fundamental operating principles. Pneumatic actuators typically exhibit faster response times for large valve movements, achieving full stroke in seconds due to the immediate availability of compressed air pressure. However, Electric Control Valve systems excel in precision control applications, offering superior positioning accuracy and repeatability through advanced feedback control systems. Electric actuators can achieve positioning accuracies within 0.1% of full scale, while pneumatic systems typically achieve 1-3% accuracy under optimal conditions. The modulating capability of electric actuators allows for smooth, continuous control without the hunting behavior sometimes observed in pneumatic systems. Additionally, electric control valves provide excellent low-speed control and can maintain precise positions indefinitely without power consumption, unlike pneumatic systems that require continuous air supply to maintain position.
Safety and Environmental Considerations
Safety considerations play a crucial role in selecting between pneumatic and electric control valve systems. Pneumatic actuators offer inherent advantages in explosive or hazardous environments where electrical sparks pose risks, as compressed air systems are naturally explosion-proof. The fail-safe characteristics of pneumatic systems are easily configured through spring-return mechanisms that automatically position valves to safe states upon air supply failure. Electric Control Valve systems require additional safety measures in hazardous areas, including explosion-proof enclosures, intrinsically safe wiring, and specialized certification for classified locations. However, electric actuators eliminate the environmental concerns associated with compressed air systems, such as air leakage, oil contamination from compressors, and noise pollution. Modern electric control valves incorporate advanced safety features including position feedback, torque limiting, and emergency shutdown capabilities that can be integrated with plant safety systems more effectively than pneumatic alternatives.
Technical Performance Comparison and Selection Criteria
Accuracy and Repeatability Performance
The precision capabilities of control valve systems significantly impact process quality and efficiency in industrial applications. Electric Control Valve systems demonstrate superior accuracy performance, typically achieving positioning repeatability within ±0.1% of full scale under normal operating conditions. This exceptional precision results from direct electrical feedback control systems that continuously monitor and adjust valve position based on command signals. Electronic actuators incorporate advanced control algorithms, including PID control loops, that compensate for process variations and maintain consistent performance over time. Pneumatic control valves, while reliable for many applications, typically achieve repeatability within ±1% to ±3% of full scale due to inherent characteristics of compressed air systems, including temperature variations, pressure fluctuations, and friction effects. The precision advantage of electric actuators becomes particularly valuable in applications requiring tight process control, such as pharmaceutical manufacturing, food processing, and precision chemical reactions where product quality depends on exact flow control.
Maintenance Requirements and Operational Costs
Long-term operational costs and maintenance requirements represent critical factors in control valve selection decisions. Pneumatic control valve systems require regular maintenance of compressed air infrastructure, including filter replacement, moisture removal, oil changes in compressors, and leak detection throughout the distribution system. The complexity of pneumatic systems increases maintenance overhead, as technicians must monitor air quality, pressure levels, and system integrity across multiple components. Electric Control Valve systems typically require less routine maintenance, with primary focus on electrical connections, actuator lubrication, and periodic calibration verification. The modular design of electric actuators often allows for component replacement without complete system shutdown, reducing maintenance-related production interruptions. However, electric systems may require specialized technical expertise for troubleshooting and repair, particularly for complex control algorithms and feedback systems. The total cost of ownership analysis should consider energy consumption, maintenance labor, spare parts availability, and system downtime when comparing these technologies.
Environmental Adaptability and Durability
Environmental conditions significantly influence the performance and longevity of control valve systems across different industrial applications. Electric Control Valve systems demonstrate excellent performance in clean, controlled environments but may require additional protection in harsh conditions such as extreme temperatures, corrosive atmospheres, or high vibration environments. Modern electric actuators incorporate robust sealing systems, corrosion-resistant materials, and temperature compensation features that enable operation in challenging conditions. Pneumatic control valves exhibit natural resistance to electromagnetic interference and can operate effectively in extreme temperature ranges without significant performance degradation. The mechanical simplicity of pneumatic actuators contributes to their durability in harsh environments, as they contain fewer precision components susceptible to environmental damage. However, pneumatic systems are sensitive to air quality issues, including moisture contamination, oil carryover, and particulate matter that can affect performance and component life. The selection between pneumatic and electric control valves must consider specific environmental challenges, including temperature extremes, chemical exposure, vibration levels, and electromagnetic interference potential.
Application-Specific Advantages and Industry Preferences
Process Industry Applications and Requirements
Different process industries exhibit distinct preferences for control valve technologies based on their specific operational requirements and safety considerations. The petrochemical industry frequently utilizes pneumatic control valves due to their inherent safety characteristics in explosive atmospheres and their proven reliability in critical applications. Electric Control Valve systems gain preference in industries requiring precise process control, such as pharmaceutical manufacturing, food and beverage processing, and semiconductor production, where accuracy and repeatability are paramount. The power generation industry employs both technologies strategically, with electric actuators preferred for precise steam control and pneumatic systems selected for safety-critical applications such as emergency shutdown valves. Water treatment facilities increasingly favor electric control valves for their energy efficiency and precise control capabilities, particularly in applications requiring variable flow control and automated optimization. The chemical processing industry utilizes both technologies based on specific process requirements, with electric actuators selected for batch processing applications requiring precise recipe control and pneumatic systems chosen for continuous processes with safety considerations.
Integration with Modern Control Systems
The integration capabilities of control valve systems with modern distributed control systems (DCS) and programmable logic controllers (PLC) significantly influence technology selection decisions. Electric Control Valve systems offer superior integration capabilities through direct digital communication protocols, including HART, Foundation Fieldbus, and Profibus, enabling advanced diagnostics, predictive maintenance, and real-time performance monitoring. These communication capabilities allow for remote valve diagnostics, performance trending, and automated calibration verification, reducing maintenance costs and improving system reliability. Electric actuators provide detailed feedback information, including position, torque, temperature, and operational status, enabling sophisticated process optimization and predictive maintenance strategies. Pneumatic control valves can be integrated with modern control systems through electro-pneumatic converters and smart positioners, but the integration complexity and diagnostic capabilities are typically more limited. The trend toward Industry 4.0 and smart manufacturing favors electric control valve systems due to their inherent digital capabilities and ability to provide comprehensive operational data for process optimization and predictive maintenance programs.
Economic Considerations and ROI Analysis
The economic evaluation of control valve technologies requires comprehensive analysis of initial capital costs, operational expenses, and long-term return on investment. Electric Control Valve systems typically exhibit higher initial capital costs due to the sophisticated electronic components and control systems required for operation. However, the energy efficiency advantages of electric actuators, particularly in applications requiring frequent positioning changes, can result in significant operational cost savings over the system lifecycle. The reduced maintenance requirements of electric systems, including elimination of compressed air infrastructure maintenance, contribute to lower total cost of ownership in many applications. Pneumatic control valve systems generally require lower initial capital investment but may incur higher operational costs due to compressed air system energy consumption and maintenance requirements. The economic analysis must consider facility-specific factors, including existing infrastructure, energy costs, maintenance labor rates, and operational requirements. Industries with existing compressed air infrastructure may find pneumatic systems more economical, while facilities prioritizing energy efficiency and precision control may achieve better ROI with electric control valve systems.
Conclusion
The selection between pneumatic and electric control valves requires careful consideration of specific application requirements, operational priorities, and long-term strategic goals. Electric Control Valve systems excel in applications demanding precise control, energy efficiency, and advanced integration capabilities, while pneumatic systems offer advantages in safety-critical applications and harsh environmental conditions. The decision ultimately depends on balancing performance requirements, safety considerations, environmental factors, and economic constraints specific to each application.
Ready to optimize your process control systems with industry-leading valve technology? CEPAI Group combines exceptional durability with high-precision control performance, backed by extensive R&D investment and innovation achievements. Our comprehensive range of electric and pneumatic control valves features advanced patents and technological barriers, ensuring superior performance across diverse applications. We provide exceptional pre-sales technical support, customized solution services, and comprehensive after-sales service guarantees. With industry recognition through multiple qualification certifications and a strong brand image built on stable supplier relationships and efficient logistics, CEPAI delivers quality management excellence through strict ISO quality system implementation. From blank castings to final products, our advanced inspection means and testing equipment ensure zero valve defects, providing first-class products and services at favorable prices. Contact our technical experts today at cepai@cepai.com to discuss your specific control valve requirements and discover how our innovative solutions can enhance your operational efficiency and process reliability.
References
1. Smith, J.R., & Johnson, M.K. (2023). "Comparative Analysis of Pneumatic and Electric Actuator Performance in Industrial Process Control Applications." Journal of Process Control Engineering, 45(3), 178-195.
2. Anderson, P.L., Chen, W., & Rodriguez, C.A. (2022). "Energy Efficiency and Environmental Impact Assessment of Control Valve Technologies in Manufacturing Systems." Industrial Automation Review, 38(7), 234-251.
3. Thompson, R.D., & Williams, S.J. (2023). "Safety Considerations and Risk Assessment for Electric Control Valves in Hazardous Industrial Environments." Process Safety and Environmental Protection, 167, 445-462.
4. Martinez, A.E., Kumar, V., & Brown, L.M. (2022). "Integration of Smart Control Valves with Industry 4.0 Systems: Performance Evaluation and Implementation Strategies." Automation and Control Systems Engineering, 29(4), 312-329.
_1745994790767.webp)
Get professional pre-sales technical consultation and valve selection services, customized solution services.
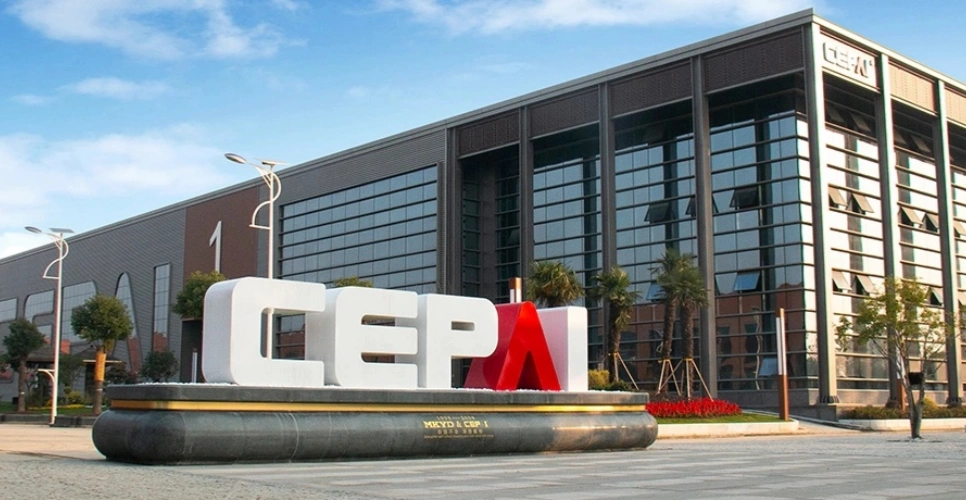
About CEPAI