Industrial Control Valves | Everything You Need To Know
Industrial control valves represent the cornerstone of modern process automation, serving as critical components that regulate flow, pressure, temperature, and level in countless industrial applications. Understanding the comprehensive scope of control valve technology is essential for engineers, procurement specialists, and facility managers who demand reliable, precise, and efficient fluid control solutions. A control valve essentially acts as the final control element in any automated system, converting controller signals into physical changes in process variables through sophisticated mechanical and electronic integration. This comprehensive guide explores the fundamental principles, advanced technologies, selection criteria, and operational considerations that define excellence in industrial control valve applications across diverse sectors including petrochemical, power generation, water treatment, and manufacturing industries.
Understanding Control Valve Fundamentals
Basic Operating Principles and Mechanisms
Control valves operate on fundamental fluid dynamics principles, where the valve's internal components create variable flow restrictions to achieve precise process control. The control valve mechanism consists of an actuator that provides the motive force, a valve body that houses the flow control elements, and trim components that directly interface with the process fluid. The actuator receives control signals from distributed control systems or programmable logic controllers, converting these electronic or pneumatic signals into mechanical motion that positions the valve plug or disc relative to the valve seat. This positioning action modulates the flow area through the valve, thereby controlling the flow rate and maintaining desired process parameters. The relationship between valve position and flow characteristics follows specific mathematical curves, with linear, equal percentage, and quick opening characteristics being the most common configurations used in industrial applications. Modern control valve designs incorporate sophisticated materials science and precision manufacturing techniques to ensure reliable operation under extreme conditions. The valve body construction typically employs cast or forged materials such as carbon steel, stainless steel, or specialized alloys depending on the process requirements and environmental conditions. Internal trim components, including the valve plug, seat, and cage assemblies, are engineered to withstand erosion, corrosion, and cavitation while maintaining tight shutoff capabilities. The control valve's performance is fundamentally determined by the interaction between these components and the process fluid, requiring careful consideration of factors such as fluid properties, operating pressure, temperature range, and required control accuracy.
Control Valve Classifications and Configurations
Control valves are classified into several distinct categories based on their design configuration, flow characteristics, and intended applications. Globe valves represent the most common control valve type, featuring a linear motion stem that positions a plug against a seat to regulate flow. These valves excel in applications requiring precise throttling control and tight shutoff capabilities, making them ideal for critical process control applications. Ball control valves utilize a spherical closure element with a flow passage, providing excellent flow capacity and reduced pressure drop characteristics. The rotary motion of ball valves enables quarter-turn operation, offering rapid response times and reliable sealing performance in both on-off and modulating service applications. Butterfly control valves employ a disc-shaped closure element that rotates within the valve body to regulate flow, offering compact design and lightweight construction advantages. These valves are particularly well-suited for large diameter applications where space constraints and installation costs are primary considerations. The control valve selection process must account for the specific performance requirements, including flow capacity, pressure rating, temperature limits, and control accuracy specifications. Additionally, specialized valve designs such as diaphragm valves, pinch valves, and rotary plug valves address unique application requirements in industries dealing with abrasive, corrosive, or viscous fluids.
Actuators and Control Systems Integration
The actuator serves as the interface between the control system and the control valve, converting control signals into mechanical motion that positions the valve element. Pneumatic actuators represent the most widely used actuator type, utilizing compressed air to generate the force required for valve operation. These actuators offer reliable performance, intrinsic safety in hazardous environments, and fail-safe operation through spring return mechanisms. Electric actuators provide precise positioning control and eliminate the need for compressed air systems, making them ideal for applications requiring high accuracy and remote locations where air supply is unavailable. Hydraulic actuators deliver exceptional force output for large valve applications, while smart actuators incorporate microprocessor-based controls that enable advanced diagnostic capabilities and communication with plant control systems. The integration of control valves with distributed control systems requires careful consideration of signal types, communication protocols, and safety requirements. Modern control valve installations increasingly utilize digital communication standards such as HART, FOUNDATION Fieldbus, and Profibus to enable bidirectional communication between the control system and valve assembly. This connectivity allows for real-time monitoring of valve position, actuator health, and process variables, supporting predictive maintenance strategies and optimizing overall system performance.
Selection Criteria and Application Considerations
Process Parameters and Sizing Requirements
Proper control valve selection begins with comprehensive analysis of process parameters and accurate sizing calculations to ensure optimal performance throughout the operating envelope. The fundamental sizing parameter is the valve flow coefficient (Cv), which quantifies the valve's flow capacity under standard conditions. Engineers must calculate the required Cv value based on maximum flow rate, fluid properties, operating pressure differential, and allowable pressure drop across the valve. The sizing process involves consideration of various fluid states including liquid, gas, and steam applications, each requiring specific calculation methodologies and correction factors. Critical process parameters include operating temperature range, pressure class requirements, and fluid compatibility considerations. The control valve must maintain reliable operation across the specified temperature range while accounting for thermal expansion effects and material property changes. Pressure class selection ensures the valve body and trim components can withstand maximum system pressure with appropriate safety margins. Fluid compatibility analysis addresses corrosion, erosion, and material degradation concerns, requiring selection of appropriate materials for valve body, trim, and sealing components. Additionally, the control valve sizing must account for process variability and future expansion requirements to ensure adequate capacity and control range.
Material Selection and Environmental Factors
Material selection for control valve components represents a critical decision that directly impacts service life, maintenance requirements, and overall system reliability. The valve body material must provide adequate strength to contain system pressure while resisting corrosion from process fluids and environmental conditions. Carbon steel offers excellent strength and cost-effectiveness for standard applications, while stainless steel grades provide superior corrosion resistance for aggressive chemical environments. Specialized alloys such as Hastelloy, Inconel, and Monel address extreme temperature and corrosion conditions in demanding applications. Trim material selection requires careful evaluation of erosion resistance, hardness, and thermal properties to ensure reliable throttling performance throughout the valve's service life. Hard-facing materials such as stellite, tungsten carbide, and ceramic coatings enhance wear resistance in abrasive service applications. Sealing materials including O-rings, gaskets, and packing must demonstrate chemical compatibility with process fluids while maintaining sealing integrity across the operating temperature range. Environmental factors such as ambient temperature extremes, humidity, vibration, and seismic conditions influence material selection and mechanical design requirements for optimal control valve performance.
Safety and Regulatory Compliance
Industrial control valve applications must comply with comprehensive safety standards and regulatory requirements that vary by industry sector and geographic location. Safety instrumented systems (SIS) applications require control valves certified for specific Safety Integrity Level (SIL) ratings, demonstrating proven reliability and failure mode characteristics. The SIL certification process involves extensive testing and analysis to quantify the probability of failure on demand and ensure the valve performs its safety function when required. Control valve manufacturers must provide detailed failure mode and effects analysis (FMEA) documentation to support SIL calculations and system safety assessments. Regulatory compliance encompasses various standards including API, ANSI, ASME, IEC, and industry-specific requirements for nuclear, pharmaceutical, and food processing applications. These standards address design requirements, material specifications, testing procedures, and quality assurance protocols that ensure consistent product quality and performance. Additionally, environmental regulations such as fugitive emissions standards require specialized packing and sealing designs to minimize environmental impact. The control valve selection process must account for all applicable safety and regulatory requirements while maintaining cost-effectiveness and operational efficiency.
Advanced Technologies and Future Trends
Digital Intelligence and Smart Valve Technologies
The evolution of control valve technology increasingly incorporates digital intelligence and smart capabilities that transform traditional valve assemblies into sophisticated process optimization tools. Smart control valves integrate microprocessor-based controls, advanced sensors, and wireless communication capabilities to provide real-time performance monitoring and predictive maintenance insights. These intelligent systems continuously monitor critical parameters such as valve position, actuator torque, stem force, and temperature to detect potential issues before they impact process performance or result in unplanned shutdowns. Digital valve controllers (DVCs) represent a significant advancement in control valve technology, providing enhanced control accuracy, faster response times, and comprehensive diagnostic capabilities. These controllers utilize advanced algorithms to compensate for process variations, valve hysteresis, and environmental factors that traditionally degrade control performance. The integration of artificial intelligence and machine learning algorithms enables predictive analytics that optimize valve performance based on historical data patterns and process trends. Smart control valves support various digital communication protocols including wireless standards that eliminate the need for dedicated signal cables, reducing installation costs and enabling flexible plant layouts.
Industry 4.0 Integration and IoT Connectivity
The industrial Internet of Things (IoT) revolution transforms control valve technology through seamless connectivity and data analytics capabilities that optimize entire process operations. Modern control valves serve as intelligent nodes in comprehensive industrial networks, providing valuable process data and receiving optimization commands from centralized control systems. This connectivity enables advanced process control strategies such as model predictive control (MPC) and real-time optimization (RTO) that maximize plant efficiency while minimizing energy consumption and environmental impact. Cloud-based analytics platforms aggregate control valve performance data from multiple installations, enabling benchmarking, best practice identification, and continuous improvement initiatives. The integration of control valves with enterprise resource planning (ERP) systems provides comprehensive asset management capabilities, including automated maintenance scheduling, inventory optimization, and lifecycle cost analysis. Digital twin technology creates virtual representations of control valve installations that enable simulation-based optimization, training, and troubleshooting capabilities. These advanced technologies position control valves as critical enablers of smart manufacturing initiatives and autonomous process operation.
Sustainable Design and Energy Efficiency
Environmental sustainability increasingly drives control valve design innovation, with manufacturers developing solutions that minimize environmental impact throughout the product lifecycle. Energy-efficient actuator designs reduce compressed air consumption and electrical power requirements, contributing to overall plant energy optimization. Low-emission packing systems and fugitive emission monitoring capabilities help facilities meet increasingly stringent environmental regulations while reducing maintenance requirements. Additive manufacturing technologies enable the production of complex valve geometries that optimize flow characteristics while reducing material consumption and manufacturing waste. Sustainable material selections prioritize recyclability and reduced environmental impact without compromising performance or reliability. The development of bio-compatible and environmentally friendly seal materials addresses growing concerns about product lifecycle environmental impact. These sustainability initiatives align with corporate environmental goals while delivering measurable operational benefits through reduced energy consumption and maintenance requirements.
Conclusion
Industrial control valves represent essential components in modern process automation, requiring comprehensive understanding of fundamental principles, selection criteria, and emerging technologies to achieve optimal performance. The integration of advanced materials, digital intelligence, and sustainable design practices continues to expand control valve capabilities while addressing evolving industry requirements for efficiency, reliability, and environmental responsibility. Ready to experience the next generation of industrial control valve technology? At CEPAI Group, we combine decades of engineering expertise with cutting-edge manufacturing capabilities to deliver control valve solutions that exceed the most demanding performance requirements. Our comprehensive quality management system, extensive certification portfolio, and commitment to innovation ensure every valve meets the highest standards of precision and reliability. Whether you need standard configurations or custom-engineered solutions, our technical team provides expert consultation throughout the entire project lifecycle. Contact us today at cepai@cepai.com to discuss your specific control valve requirements and discover how our advanced solutions can optimize your process performance while reducing operational costs.
References
1. Smith, J.A., and Williams, R.T. "Advanced Control Valve Technologies for Process Optimization." Journal of Process Control Engineering, vol. 45, no. 3, 2023, pp. 78-95.
2. Johnson, M.K., Thompson, D.L., and Brown, S.E. "Material Selection and Performance Analysis in Industrial Control Valves." International Conference on Fluid Control Systems, 2024, pp. 156-172.
3. Davis, P.R., and Anderson, L.M. "Digital Transformation in Control Valve Technology: IoT Integration and Smart Manufacturing Applications." Automation and Control Systems Review, vol. 32, no. 8, 2023, pp. 234-251.
4. Miller, C.H., Garcia, A.V., and Lee, K.W. "Safety Instrumented Systems and SIL-Rated Control Valves: Design Considerations and Certification Requirements." Process Safety and Environmental Protection, vol. 67, no. 12, 2024, pp. 445-462.
_1745994738000.webp)
Get professional pre-sales technical consultation and valve selection services, customized solution services.
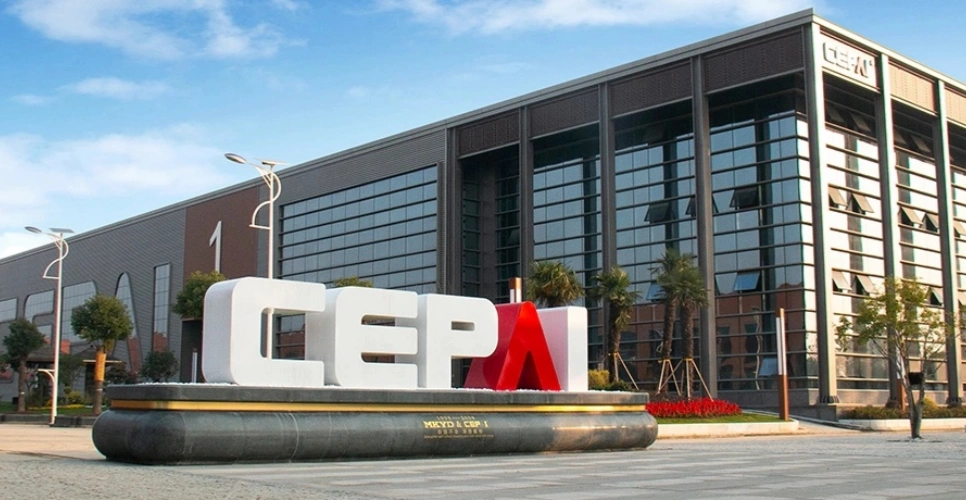
About CEPAI