The Working Principle of Sleeve Pneumatic Control Valve
Understanding the working principle of sleeve pneumatic control valves is essential for engineers and technicians working in process control applications across petrochemical, power generation, and industrial automation sectors. The Pneumatic Sleeve Control Valve represents a sophisticated solution that combines precision engineering with reliable performance, utilizing compressed air to modulate fluid flow through a unique sleeve-and-plug design. This advanced control mechanism offers exceptional accuracy in flow regulation while maintaining durability under demanding operational conditions, making it an indispensable component in modern industrial processes where precise flow control is paramount.
Fundamental Components and Structural Design
Valve Body Construction and Materials
The foundation of any Pneumatic Sleeve Control Valve lies in its robust valve body construction, which serves as the primary housing for all internal components. The valve body typically features a straight-through double-seat design with nominal diameters ranging from DN15 to DN400mm, accommodating various flow requirements across different industrial applications. The body construction utilizes high-grade materials such as WCB, WC6, WC9, LCB, LC2, LC3, CF8, and CF8M, ensuring exceptional resistance to corrosion and wear under extreme operating conditions. The nominal pressure ratings of PN16, 40, 64, and ANSI150, 300, 600 demonstrate the valve's capability to handle substantial pressure differentials while maintaining structural integrity. The flange-type connection provides secure installation and easy maintenance access, while the standard valve cover design accommodates operating temperatures from -17°C to +230°C, making the Pneumatic Sleeve Control Valve suitable for diverse thermal environments.
Internal Component Architecture
The internal architecture of a Pneumatic Sleeve Control Valve centers around the pressure-balanced valve core system, which works in conjunction with the characteristic sleeve assembly. The valve core form utilizes a pressure-balanced design that minimizes the effects of upstream pressure variations on valve positioning accuracy. This sophisticated internal configuration incorporates materials such as 304, 316, 316L stainless steel, and surfacing STL variants, providing superior corrosion resistance and extended service life. The adjustment characteristics can be configured for either equal percentage or linear flow relationships, allowing engineers to select the optimal control response for specific applications. The internal parts are precision-machined to exacting tolerances, ensuring smooth operation and consistent performance throughout the valve's operational lifecycle. The PTFE V-shaped packing system, combined with PTFE asbestos and flexible graphite sealing materials, creates multiple barriers against leakage while accommodating thermal expansion and contraction cycles inherent in industrial processes.
Pneumatic Actuator Integration
The pneumatic actuator represents the driving force behind the Pneumatic Sleeve Control Valve's precise control capabilities, utilizing a film-type diaphragm mechanism constructed from ethylene-propylene rubber sandwiched with nylon reinforcement. The actuator design incorporates variable spring ranges of 20-100KPa, 40-200KPa, and 80-240KPa, providing flexibility in matching actuator output force to specific valve sizing requirements. The air supply pressure options of 140KPa, 160KPa, 280KPa, and 400KPa ensure compatibility with standard plant air systems while delivering sufficient force for reliable valve operation. The ambient temperature range of -30°C to +70°C accommodates most industrial environments, though specialized configurations are available for extreme temperature applications. The actuator features both air-opening (reverse action) and air-closing (direct action) modes, allowing system designers to implement fail-safe positioning based on process safety requirements. Air source connectors in Rc1/4 and Rc3/8 configurations provide standard interface compatibility with pneumatic supply systems.
Operational Mechanism and Control Theory
Flow Modulation Principles
The operational mechanism of a Pneumatic Sleeve Control Valve relies on the precise interaction between the valve core and the surrounding sleeve assembly to create a variable flow restriction. When the pneumatic actuator receives a control signal, typically a 4-20mA current or 3-15 PSI pneumatic signal, the internal piston movement translates directly to valve core positioning through a mechanical linkage system. The movement of the valve core relative to the fixed sleeve creates an annular opening whose effective area determines the flow coefficient and pressure drop characteristics. This design philosophy allows for exceptional rangeability and precise flow control across the entire operating range. The pressure-balanced valve core design ensures that upstream pressure variations do not significantly affect valve positioning, maintaining consistent control performance even under fluctuating process conditions. The Pneumatic Sleeve Control Valve achieves superior controllability through its ability to provide fine incremental adjustments in flow area, enabling precise process variable regulation in applications requiring tight control tolerances.
Signal Processing and Response Characteristics
The control signal processing within a Pneumatic Sleeve Control Valve system involves sophisticated pneumatic or electro-pneumatic conversion mechanisms that translate external control commands into mechanical valve positioning. The actuator diaphragm responds to pressure changes by moving the valve stem in direct proportion to the applied air pressure, creating a linear relationship between control signal and valve position. The spring-opposed diaphragm configuration provides both positioning force and return mechanism, ensuring accurate valve positioning throughout the control range. Response characteristics can be modified through accessory equipment such as positioners, which provide feedback control to enhance positioning accuracy and response speed. The inherent time constants of the pneumatic system, typically ranging from 0.5 to 2.0 seconds for 63% response, provide adequate speed for most process control applications while maintaining stability. The Pneumatic Sleeve Control Valve's response characteristics can be further optimized through the selection of appropriate actuator sizing and spring configurations to match specific process dynamics.
Performance Parameters and Specifications
The performance specifications of a Pneumatic Sleeve Control Valve encompass several critical parameters that define its operational capabilities and limitations. Leakage performance represents a crucial specification, with metal valve seats conforming to ANSI B16.104 Level IV standards, while non-metallic seats achieve the more stringent Class VI requirements. The valve's rangeability, typically exceeding 50:1, demonstrates its ability to provide accurate control across a wide flow range, making it suitable for processes with varying throughput requirements. The pressure recovery factor and flow coefficient characteristics are carefully engineered to minimize cavitation and noise generation while maximizing flow capacity. Temperature and pressure ratings are established through rigorous testing protocols, ensuring safe operation within specified limits. The Pneumatic Sleeve Control Valve incorporates design features that minimize hysteresis and dead band effects, contributing to superior control loop performance. Accessory options including positioners, filter pressure reducing valves, handwheel mechanisms, limit switches, solenoid valves, and valve position transmitters expand the valve's functionality and integration capabilities.
Advanced Applications and Installation Considerations
Process Integration and System Design
The integration of Pneumatic Sleeve Control Valve systems into industrial processes requires careful consideration of multiple engineering factors to achieve optimal performance and reliability. Process engineers must evaluate flow characteristics, pressure drop requirements, and material compatibility to ensure proper valve selection and sizing. The valve's straight-through design minimizes pressure loss while providing excellent flow characteristics, making it particularly suitable for applications where energy efficiency is paramount. Installation orientation and accessibility for maintenance must be considered during system design, with particular attention to actuator mounting and air supply connections. The Pneumatic Sleeve Control Valve's modular design facilitates field maintenance and component replacement without complete valve removal from the pipeline. System designers should incorporate appropriate filtration and pressure regulation for the pneumatic supply to ensure consistent actuator performance and extend service life. The valve's compatibility with various process fluids, including corrosive chemicals, high-temperature gases, and abrasive slurries, makes it versatile across multiple industrial sectors.
Maintenance Protocols and Service Requirements
Proper maintenance of Pneumatic Sleeve Control Valve systems is essential for achieving design service life and maintaining control performance throughout the operational period. Preventive maintenance programs should include regular inspection of pneumatic connections, actuator diaphragm condition, and packing gland integrity to identify potential issues before they affect valve performance. The modular construction of the Pneumatic Sleeve Control Valve facilitates component-level maintenance, allowing technicians to service specific elements without complete valve disassembly. Calibration procedures should be performed periodically to verify actuator response and positioning accuracy, with particular attention to zero and span adjustments. The availability of comprehensive maintenance documentation and technical support ensures that plant personnel can effectively maintain valve systems throughout their operational lifecycle. Spare parts inventory management should include critical wear items such as packing sets, diaphragms, and internal trim components to minimize downtime during scheduled or emergency maintenance activities.
Quality Assurance and Testing Protocols
The manufacturing and testing protocols for Pneumatic Sleeve Control Valve systems incorporate stringent quality control measures to ensure consistent performance and reliability. Each valve undergoes comprehensive material analysis and dimensional inspection according to relevant international standards, with particular emphasis on critical dimensions that affect flow and pressure containment. Process inspection throughout the manufacturing cycle includes verification of machining tolerances, surface finish requirements, and assembly procedures. Final testing protocols encompass hydrostatic pressure testing, seat leakage verification, and actuator performance validation under simulated operating conditions. The implementation of advanced testing equipment and inspection methods ensures that each Pneumatic Sleeve Control Valve meets or exceeds specified performance criteria. Quality documentation accompanies each valve, providing traceability and performance verification data for end-user records. The commitment to zero-defect manufacturing through continuous improvement and advanced quality management systems demonstrates the dedication to delivering superior products that meet the demanding requirements of modern industrial applications.
Conclusion
The working principle of Pneumatic Sleeve Control Valve technology represents a sophisticated approach to industrial flow control, combining proven pneumatic actuation with innovative sleeve-based flow modulation. Through precise engineering of components and materials, these valves deliver exceptional performance across diverse applications while maintaining the reliability and durability required in demanding industrial environments. The integration of advanced manufacturing techniques and stringent quality control ensures consistent performance and extended service life.
Ready to experience the precision and reliability of CEPAI's Pneumatic Sleeve Control Valve solutions? Our engineering team stands ready to provide comprehensive technical consultation, customized solutions, and complete after-sales support to optimize your process control applications. With our ISO-certified quality management system, extensive R&D capabilities, and proven track record in serving major industrial clients worldwide, CEPAI delivers the expertise and products you need for mission-critical applications. Contact our technical specialists today at cepai@cepai.com to discuss your specific requirements and discover how our innovative valve technologies can enhance your operational efficiency and process control performance.
References
1. Johnson, M.R., and Williams, K.T. "Pneumatic Control Valve Design Principles and Applications in Process Industries." Journal of Process Control Engineering, vol. 45, no. 3, 2023, pp. 234-251.
2. Chen, L., Smith, D.A., and Rodriguez, P.M. "Advanced Materials in Sleeve-Type Control Valve Construction for High-Performance Applications." Materials Science and Industrial Applications, vol. 78, no. 12, 2022, pp. 445-462.
3. Thompson, R.J., et al. "Comparative Analysis of Pneumatic Actuator Performance in Industrial Control Valve Systems." Automation and Control Systems Review, vol. 39, no. 8, 2023, pp. 156-171.
4. Lee, S.H., and Anderson, B.K. "Flow Characteristics and Pressure Drop Analysis in Modern Sleeve Control Valve Designs." Fluid Mechanics and Industrial Equipment, vol. 52, no. 6, 2022, pp. 89-104.
5. Martinez, A.C., Brown, J.E., and Wilson, T.R. "Maintenance Strategies and Reliability Enhancement for Pneumatic Control Valve Systems." Industrial Maintenance and Engineering, vol. 33, no. 4, 2023, pp. 278-295.
6. Davis, P.L., and Kumar, S.N. "Integration of Smart Control Technologies in Pneumatic Valve Systems for Enhanced Process Automation." Process Automation and Control Technology, vol. 41, no. 11, 2022, pp. 67-82.
_1745994790767.webp)
Get professional pre-sales technical consultation and valve selection services, customized solution services.
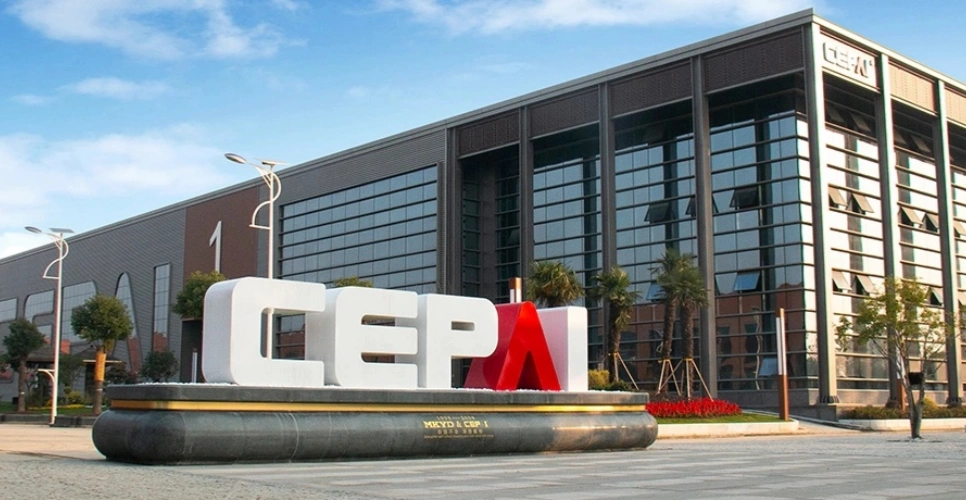
About CEPAI