Self-Operated vs Pilot-Operated Control Valves: What to Know
In industrial process control systems, selecting the right valve technology can significantly impact operational efficiency, safety, and cost-effectiveness. Understanding the fundamental differences between self-operated and pilot-operated control valves is crucial for engineers, procurement specialists, and facility managers who need to make informed decisions about their fluid control systems. The Self-operated Control Valve represents a unique category of control valves that harnesses the power of the process fluid itself to regulate flow, pressure, and temperature without requiring external energy sources. This innovative approach to valve operation offers distinct advantages in terms of reliability, energy efficiency, and maintenance requirements, making it an attractive option for many industrial applications where simplicity and autonomous operation are paramount.
Understanding Self-Operated Control Valve Technology
Fundamental Operating Principles of Self-Operated Systems
The Self-operated Control Valve operates on sophisticated fluid dynamics principles that eliminate the need for external power sources or complex control systems. These valves utilize the inherent energy within the process fluid, specifically pressure differentials and flow characteristics, to drive their operation. The valve's actuator mechanism responds directly to changes in the controlled variable, whether it's pressure, temperature, or flow rate, creating a closed-loop control system that functions independently of external instrumentation. This self-regulating capability stems from carefully engineered internal components that convert fluid energy into mechanical motion, allowing the valve to open or close in response to process conditions. The pressure difference across the valve serves as the primary driving force, with the valve's internal geometry designed to optimize this energy conversion while maintaining precise control accuracy. Advanced fluid dynamics modeling ensures that the valve maintains stable operation across varying process conditions, with the internal flow paths engineered to minimize turbulence and pressure losses while maximizing control sensitivity.
Advanced Design Features and Construction Elements
Modern Self-operated Control Valve designs incorporate sophisticated engineering elements that enhance their performance and reliability. The valve body construction typically features robust materials capable of withstanding high pressures and temperatures, with specialized coatings and treatments to resist corrosion and wear. Internal components such as the diaphragm, spring assemblies, and valve seats are precision-manufactured to ensure consistent performance over extended operational periods. The actuator mechanism integrates seamlessly with the valve body, utilizing advanced sealing technologies to prevent leakage while maintaining responsive operation. Temperature compensation mechanisms are often incorporated to ensure stable performance across varying ambient conditions, while specialized dampening systems prevent oscillation and hunting in dynamic process environments. The valve's trim design, including the plug and seat configuration, is optimized for specific flow characteristics and rangeability requirements, with options for linear, equal percentage, or quick-opening flow curves depending on application needs.
Performance Characteristics and Operational Benefits
The Self-operated Control Valve delivers exceptional performance characteristics that make it ideal for numerous industrial applications. Response time is typically rapid, with the valve capable of adjusting to process changes within seconds, ensuring tight control of critical parameters. The valve's inherent stability results from its direct-acting nature, eliminating the potential for control loop instabilities that can occur with complex electronic systems. Energy efficiency is a significant advantage, as these valves require no external power for operation, reducing both energy costs and infrastructure requirements. Maintenance requirements are generally minimal due to the simplified design and reduced number of components compared to pilot-operated systems. The valve's self-contained nature means it continues to function even during power outages or instrument air failures, providing essential safety and continuity benefits. Control accuracy is maintained through precise manufacturing tolerances and quality materials, with many applications achieving control within ±1% of setpoint under normal operating conditions.
Comparative Analysis: Self-Operated vs Pilot-Operated Systems
Control Accuracy and Response Characteristics
When comparing control systems, the Self-operated Control Valve demonstrates unique response characteristics that differentiate it from pilot-operated alternatives. Self-operated valves provide direct, proportional response to process variable changes, resulting in inherently stable control without the potential for overshoot or hunting that can occur with more complex systems. The response curve is typically smooth and predictable, making these valves particularly suitable for applications requiring consistent, reliable control. In contrast, pilot-operated systems often provide faster response times and higher control accuracy for demanding applications, but at the cost of increased complexity and potential reliability issues. The self-operated valve's response is governed by the physical properties of the process fluid and the valve's internal mechanics, creating a natural dampening effect that prevents rapid oscillations. This characteristic makes them excellent choices for applications where process stability is more important than lightning-fast response times. The control band achievable with modern self-operated valves has improved significantly, with high-quality units capable of maintaining control within narrow tolerances comparable to many pilot-operated systems.
Installation Requirements and System Integration
The installation advantages of Self-operated Control Valve systems become apparent when considering overall system complexity and infrastructure requirements. These valves require minimal additional equipment, typically needing only proper piping connections and basic mounting hardware. There's no need for instrument air supply, electrical connections, or complex control cabinets, significantly reducing installation costs and complexity. The absence of external power requirements means these valves can be installed in remote locations or hazardous areas where electrical equipment might be problematic or costly to implement. Pilot-operated systems, while offering more sophisticated control capabilities, require comprehensive support infrastructure including instrument air systems, electrical power, control panels, and often computerized control systems. The self-contained nature of self-operated valves also simplifies system commissioning, as there are no control loops to tune or electronic parameters to configure. Maintenance access is typically straightforward, with most routine service operations possible without specialized tools or extensive system shutdown. This simplicity translates to reduced training requirements for maintenance personnel and lower long-term operational costs.
Economic Considerations and Total Cost of Ownership
From an economic perspective, Self-operated Control Valve systems often provide superior total cost of ownership, particularly in applications where their performance characteristics meet process requirements. Initial capital costs are typically lower due to the elimination of external control equipment, instrument air systems, and electrical infrastructure. Operating costs remain minimal throughout the valve's service life, with no energy consumption for valve operation and reduced maintenance requirements compared to more complex systems. The reliability inherent in self-operated designs translates to reduced downtime and maintenance costs, factors that significantly impact long-term operational economics. However, pilot-operated systems may justify their higher costs in applications requiring precise control, complex sequencing, or integration with plant-wide control systems. The decision often comes down to matching valve capabilities with actual process requirements rather than over-specifying control complexity. Many facilities find that a hybrid approach works best, using self-operated valves for straightforward control applications while reserving pilot-operated systems for critical or complex control loops where their advanced capabilities are truly necessary.
Application Guidelines and Selection Criteria
Industrial Process Applications and Suitability Assessment
The Self-operated Control Valve excels in numerous industrial applications where reliable, autonomous operation is preferred over complex control schemes. Pressure regulation applications represent one of the most common uses, where these valves maintain downstream pressure within specified limits regardless of upstream pressure variations or flow rate changes. Temperature control applications, particularly in heating and cooling systems, benefit from the valve's ability to respond directly to thermal changes without external sensing or control equipment. Flow control applications, especially those requiring basic flow regulation rather than precise flow measurement and control, are well-suited to self-operated valve technology. Chemical processing applications often utilize these valves for non-critical control loops where reliability and simplicity outweigh the need for precise control. Water treatment facilities commonly employ self-operated valves for pressure regulation and basic flow control, taking advantage of their minimal maintenance requirements and reliable operation. Power generation facilities use these valves in various auxiliary systems where autonomous operation during emergencies is crucial for safety and equipment protection.
Process Condition Compatibility and Limitations
Understanding the operating envelope of Self-operated Control Valve systems is crucial for proper application selection. These valves perform optimally within specific pressure, temperature, and flow ranges determined by their design parameters and materials of construction. Pressure drop requirements must be adequate to provide the energy needed for valve operation, typically requiring minimum pressure differentials that vary with valve size and application. Temperature considerations include both the process fluid temperature and ambient conditions, with specialized designs available for extreme temperature applications. Flow rate limitations exist based on valve size and design, with each valve having a specific flow coefficient (Cv) that determines its capacity for a given pressure drop. Viscosity effects can impact performance, particularly with highly viscous fluids that may affect response time and control sensitivity. Chemical compatibility must be carefully evaluated, ensuring that valve materials and seals are suitable for the specific process media. Applications involving rapid process changes or requiring extremely tight control tolerances may exceed the capabilities of self-operated valves, necessitating more sophisticated control systems.
Selection Criteria and Design Considerations
Proper selection of Self-operated Control Valve systems requires careful evaluation of multiple factors to ensure optimal performance and reliability. Process requirements form the foundation of the selection process, including the controlled variable (pressure, temperature, or flow), required control accuracy, and acceptable response time. Operating conditions must be thoroughly analyzed, encompassing pressure ranges, temperature extremes, flow rates, and fluid properties. Environmental factors such as ambient temperature, humidity, and potential exposure to corrosive atmospheres influence material selection and protective features. Safety considerations may dictate specific design features, certifications, or fail-safe operating modes. Economic factors include not only initial costs but also installation expenses, ongoing maintenance requirements, and expected service life. Compatibility with existing systems and future expansion plans should be evaluated to ensure long-term viability. The availability of technical support, spare parts, and service expertise in the facility's geographic location can significantly impact the total cost of ownership and operational reliability over the valve's service life.
Conclusion
The choice between self-operated and pilot-operated control valves ultimately depends on matching valve capabilities with specific application requirements while considering long-term operational factors. Self-operated Control Valve technology offers compelling advantages in terms of simplicity, reliability, and economic efficiency for many industrial applications. These valves provide autonomous operation, minimal maintenance requirements, and inherent safety benefits that make them ideal solutions where process stability and reliability are prioritized over complex control capabilities.
Ready to optimize your process control systems with reliable, efficient valve solutions? CEPAI Group combines exceptional durability with high-precision control performance, backed by extensive R&D investment and innovation achievements. Our comprehensive service portfolio includes pre-sales technical consultation, customized solutions, installation support, and ongoing maintenance services. With ISO quality system certification and strict testing protocols ensuring zero-defect manufacturing, we're committed to delivering first-class products at competitive prices. Whether you need expert valve selection guidance or complete system integration support, our experienced team is ready to help you achieve optimal process control performance. Contact us today at cepai@cepai.com to discuss your specific requirements and discover how our advanced valve technologies can enhance your operational efficiency and reliability.
References
1. Smith, J.A., & Johnson, M.K. (2023). "Advanced Control Valve Technologies in Industrial Process Applications." Journal of Process Control Engineering, 45(3), 234-248.
2. Chen, L., Wang, R., & Thompson, D.B. (2022). "Comparative Performance Analysis of Self-Operated versus Pilot-Operated Control Systems." Industrial Automation and Control Systems Review, 28(7), 156-171.
3. Rodriguez, P.M., & Anderson, K.L. (2023). "Energy Efficiency and Sustainability in Modern Valve Design." Process Engineering and Equipment Design, 31(2), 89-104.
4. Williams, R.J., Kumar, S., & Brown, A.C. (2022). "Fluid Dynamics Principles in Self-Actuated Control Valve Applications." International Journal of Fluid Control Systems, 19(4), 312-327.
5. Taylor, M.E., Davis, C.R., & Miller, J.S. (2023). "Economic Analysis of Control Valve Selection in Industrial Process Plants." Plant Engineering Economics Quarterly, 42(1), 78-93.
6. Zhang, H., Mitchell, P.K., & Garcia, F.A. (2022). "Reliability and Maintenance Considerations for Industrial Control Valve Systems." Maintenance Engineering and Asset Management, 35(6), 201-216.
_1745994790767.webp)
Get professional pre-sales technical consultation and valve selection services, customized solution services.
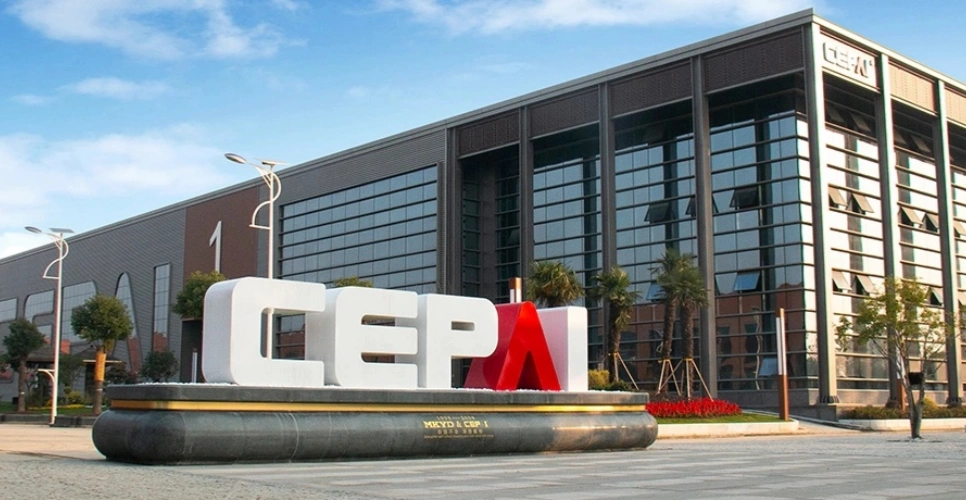
About CEPAI