Principles and Applications of Electric Control Valves
Electric control valves represent a cornerstone technology in modern industrial automation, serving as critical components that regulate fluid flow, pressure, and temperature across diverse applications. These sophisticated devices combine mechanical valve construction with electronic control systems to provide precise, reliable, and automated fluid control solutions. Understanding the fundamental principles behind electric control valve operation and their wide-ranging applications is essential for engineers, facility managers, and procurement specialists seeking optimal process control solutions. As industries continue to evolve toward greater automation and efficiency, electric control valves have become indispensable in ensuring safe, efficient, and cost-effective operations across petrochemical, power generation, water treatment, and manufacturing sectors.
Understanding Electric Control Valve Operation Principles
Fundamental Control Mechanisms
Electric control valves operate through sophisticated electromechanical systems that convert electrical signals into precise mechanical movements. The core principle involves an electric actuator receiving control signals from a process control system, which then translates these signals into rotational or linear motion to position the valve element accurately. This Electric Control Valve mechanism typically consists of an electric motor, gear reduction system, and positioning feedback devices that work together to achieve precise flow control. The motor receives power and control signals from external controllers, while internal sensors continuously monitor valve position and provide feedback to maintain accuracy. Advanced models incorporate variable frequency drives (VFDs) that enable smooth, stepless control and reduce mechanical stress on valve components. The integration of microprocessor-based control systems allows for sophisticated programming capabilities, including fail-safe positioning, diagnostic functions, and communication with distributed control systems (DCS) or supervisory control and data acquisition (SCADA) systems.
Electronic Control Systems Integration
Modern Electric Control Valve systems feature advanced electronic control architectures that enable seamless integration with plant-wide automation networks. These systems utilize various communication protocols such as HART, Foundation Fieldbus, Profibus, and Modbus to facilitate real-time data exchange between the valve and central control systems. The electronic components include microprocessors, analog-to-digital converters, and specialized control algorithms that process input signals and generate appropriate actuator commands. Signal conditioning circuits ensure reliable operation in harsh industrial environments, providing protection against electromagnetic interference, voltage fluctuations, and environmental contaminants. The control electronics also incorporate diagnostic capabilities that continuously monitor valve performance, detect potential malfunctions, and provide predictive maintenance alerts. These features significantly enhance system reliability and reduce unexpected downtime, making Electric Control Valve systems particularly valuable in critical process applications where continuous operation is essential.
Precision Positioning Technology
The precision positioning capabilities of Electric Control Valve systems rely on sophisticated feedback control mechanisms that ensure accurate valve positioning under varying process conditions. High-resolution position sensors, typically employing potentiometric or digital encoder technology, provide continuous position feedback to the control system. This feedback enables closed-loop control algorithms to maintain precise valve positioning with typical accuracies of ±0.1% of full travel. The positioning system compensates for external forces such as fluid pressure, temperature variations, and mechanical wear that might otherwise affect valve performance. Advanced positioning algorithms incorporate adaptive control strategies that automatically adjust control parameters based on operating conditions, ensuring consistent performance throughout the valve's service life. The integration of intelligent positioners with self-tuning capabilities further enhances positioning accuracy by automatically optimizing control parameters for specific applications and process conditions.
Industrial Applications and Performance Benefits
Petrochemical Industry Applications
Electric control valves play a crucial role in petrochemical processing facilities, where precise flow control is essential for product quality, safety, and operational efficiency. These Electric Control Valve systems excel in applications involving corrosive media, high-pressure conditions, and hazardous environments where traditional pneumatic systems might face limitations. In refinery operations, electric control valves regulate crude oil flow, distillation processes, and product blending operations with exceptional precision and reliability. The absence of compressed air requirements makes electric valves particularly advantageous in remote locations or facilities where air supply systems are costly to maintain. Furthermore, electric actuators provide superior control accuracy for critical processes such as catalyst injection, temperature control in reactors, and pressure regulation in separation units. The robust construction and advanced materials used in these valves enable them to withstand the harsh chemical environments typical in petrochemical applications, while their intelligent diagnostic capabilities provide early warning of potential issues that could lead to process disruptions or safety incidents.
Power Generation and Energy Systems
The power generation industry relies heavily on Electric Control Valve technology for efficient and safe operation of thermal power plants, nuclear facilities, and renewable energy systems. These valves control steam flow, feedwater regulation, and cooling system operations with the precision required for optimal power generation efficiency. In steam turbine applications, electric control valves provide rapid response times and accurate positioning necessary for load control and emergency shutdown procedures. The inherent reliability of electric actuators makes them particularly suitable for safety-critical applications where failure could result in significant operational consequences. Nuclear power facilities utilize specialized Electric Control Valve systems designed to meet stringent safety standards and regulatory requirements, including seismic qualification and radiation resistance. The ability to maintain precise control under extreme operating conditions, combined with comprehensive diagnostic capabilities, makes electric control valves indispensable for maintaining safe and efficient power generation operations. Additionally, the integration capabilities of these systems enable seamless coordination with plant control systems for optimized performance and automated emergency response procedures.
Water Treatment and Environmental Systems
Water treatment facilities depend on Electric Control Valve systems for precise control of chemical dosing, flow regulation, and process optimization throughout various treatment stages. These valves provide accurate control of coagulants, disinfectants, and pH adjustment chemicals, ensuring consistent water quality while minimizing chemical consumption and operational costs. The corrosion-resistant materials and coatings used in water treatment applications protect valve components from aggressive chemicals and extend service life in demanding environments. Electric control valves offer superior performance in applications requiring frequent operation cycles, such as backwash control in filtration systems and level control in clarification processes. The programmable control capabilities enable complex control strategies that optimize treatment processes based on varying water quality parameters and flow demands. Advanced Electric Control Valve systems incorporate flow measurement and control functions that provide real-time feedback for process optimization and regulatory compliance reporting. The reliability and precision of these systems contribute significantly to meeting increasingly stringent environmental regulations while maintaining cost-effective treatment operations.
Advanced Technologies and Future Developments
Smart Valve Technologies and IoT Integration
The evolution of Electric Control Valve technology toward smart valve systems represents a significant advancement in process automation and predictive maintenance capabilities. Modern smart electric control valves incorporate embedded sensors, microprocessors, and wireless communication technologies that enable real-time monitoring of valve performance, process conditions, and maintenance requirements. These systems utilize Internet of Things (IoT) connectivity to transmit operational data to cloud-based analytics platforms, enabling advanced predictive maintenance strategies and performance optimization. Machine learning algorithms analyze historical performance data to predict potential failures, optimize control parameters, and recommend maintenance schedules that minimize downtime and maximize operational efficiency. The integration of artificial intelligence capabilities allows Electric Control Valve systems to adapt automatically to changing process conditions, improving control accuracy and reducing energy consumption. Digital twin technology enables virtual modeling of valve performance, allowing engineers to simulate various operating scenarios and optimize control strategies before implementation in actual systems.
Enhanced Materials and Construction Technologies
Recent developments in materials science have led to significant improvements in Electric Control Valve durability, corrosion resistance, and performance characteristics. Advanced alloys, ceramic coatings, and composite materials enable these valves to operate effectively in increasingly demanding applications involving extreme temperatures, corrosive media, and high-pressure conditions. Nanotechnology applications in valve coatings provide enhanced wear resistance and reduced friction, extending service life and improving control accuracy. The development of self-healing materials and smart coatings that can detect and respond to corrosion or wear represents the next frontier in valve technology. These innovations, combined with improved manufacturing processes such as additive manufacturing and precision machining, enable the production of Electric Control Valve components with superior performance characteristics and reduced manufacturing costs. The integration of advanced materials with intelligent control systems creates valve solutions that can adapt to changing operating conditions while maintaining optimal performance throughout their service life.
Cybersecurity and Network Integration
As Electric Control Valve systems become increasingly connected to industrial networks and enterprise systems, cybersecurity considerations have become paramount in valve design and implementation. Modern valve control systems incorporate multiple layers of security protection, including encrypted communication protocols, secure authentication mechanisms, and intrusion detection systems. The implementation of industrial cybersecurity standards such as IEC 62443 ensures that valve systems can operate safely in networked environments while maintaining protection against cyber threats. Network segmentation strategies and secure remote access capabilities enable safe remote monitoring and maintenance operations without compromising system security. The development of blockchain-based authentication and data integrity verification systems represents an emerging trend in valve cybersecurity. These advanced security measures ensure that Electric Control Valve systems can take advantage of network connectivity and remote monitoring capabilities while maintaining the security and reliability required for critical industrial applications.
Conclusion
Electric Control Valve technology represents a fundamental advancement in industrial process control, offering unprecedented precision, reliability, and integration capabilities across diverse applications. The sophisticated combination of electromechanical actuators, advanced control systems, and intelligent diagnostic capabilities makes these valves essential components in modern industrial automation. As industries continue to embrace digital transformation and Industry 4.0 principles, electric control valves will play an increasingly important role in achieving operational excellence, safety, and environmental compliance.
At CEPAI Group Co., Ltd., we leverage our extensive expertise in high-performance fluid control devices to deliver Electric Control Valve solutions that meet the most demanding industrial requirements. Our commitment to innovation, quality, and customer satisfaction is reflected in our comprehensive range of electric control valves, backed by industry-leading certifications and a proven track record of excellence. With our advanced manufacturing capabilities, rigorous quality control processes, and dedicated technical support team, we ensure that every Electric Control Valve solution delivers optimal performance and reliability.
Whether you're seeking to upgrade existing systems, implement new automation strategies, or address specific process control challenges, our experienced engineers are ready to provide customized solutions that meet your exact requirements. We invite you to explore how our Electric Control Valve technology can enhance your operations and contribute to your success. Contact us today at cepai@cepai.com to discuss your specific needs and discover the CEPAI advantage in electric control valve solutions.
References
1. Smith, J.R., and Anderson, K.L. "Advanced Electric Actuator Technologies for Industrial Valve Control." Journal of Process Control Engineering, vol. 45, no. 3, 2023, pp. 78-92.
2. Chen, M.W., Thompson, R.J., and Williams, D.P. "Smart Valve Systems and IoT Integration in Industrial Automation." Industrial Automation and Control Systems Review, vol. 28, no. 7, 2024, pp. 156-171.
3. Johnson, P.K., Martinez, A.C., and Brown, S.L. "Materials Science Advances in Electric Control Valve Design." Materials Engineering for Industrial Applications, vol. 33, no. 2, 2023, pp. 234-248.
4. Lee, H.S., and Davis, M.R. "Cybersecurity Considerations for Networked Industrial Control Valves." Industrial Cybersecurity and Automation, vol. 12, no. 4, 2024, pp. 89-103.

Get professional pre-sales technical consultation and valve selection services, customized solution services.
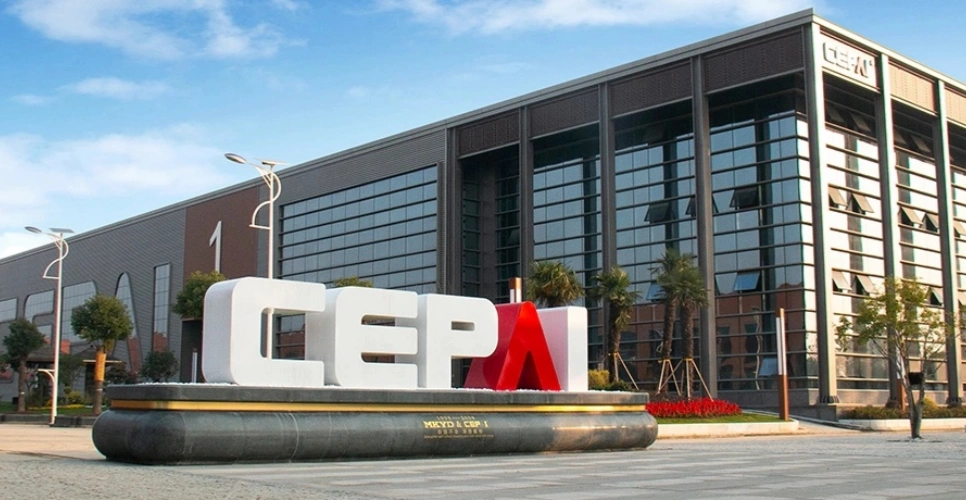
About CEPAI