How Different Pneumatic Control Valves Work and Where to Use Them?
Understanding the operation and application of pneumatic control valves is essential for engineers and industrial professionals working across various sectors. A pneumatic control valve utilizes compressed air to operate valve mechanisms, providing precise flow control, pressure regulation, and system automation in industrial processes. These valves serve as critical components in petrochemical plants, power generation facilities, water treatment systems, and manufacturing operations where reliable performance and accurate control are paramount for operational efficiency and safety.
Understanding Pneumatic Control Valve Operating Principles
Air-to-Open and Air-to-Close Mechanisms
The fundamental operation of a pneumatic control valve depends on its actuator design and air signal configuration. Air-to-open pneumatic control valves utilize compressed air pressure to overcome spring tension and open the valve stem, allowing increased flow when air pressure increases. Conversely, air-to-close configurations use air pressure to compress the spring mechanism, closing the valve against the flow stream. This distinction is crucial for fail-safe operations, where system safety requirements dictate whether the valve should fail in the open or closed position during air supply interruption. The selection between these mechanisms depends on process requirements, safety considerations, and the specific application environment. Modern pneumatic control valve systems incorporate sophisticated positioners that provide precise control feedback, ensuring accurate valve positioning regardless of process conditions or external disturbances affecting system performance.
Diaphragm and Piston Actuator Technologies
Pneumatic control valve actuators employ either diaphragm or piston mechanisms to convert air pressure into mechanical motion. Diaphragm actuators utilize a flexible membrane that deflects under air pressure, providing smooth operation and excellent sensitivity to control signals. These actuators are particularly suitable for applications requiring precise positioning and minimal hysteresis. Piston actuators, alternatively, use a cylindrical piston within a chamber to generate higher force outputs, making them ideal for high-pressure applications or large valve assemblies. The choice between diaphragm and piston pneumatic control valve actuators influences performance characteristics including response time, force output, and maintenance requirements. Diaphragm actuators typically offer superior control precision and lower maintenance needs, while piston actuators provide greater force capability and durability in demanding industrial environments.
Control Signal Processing and Positioning
Modern pneumatic control valve systems incorporate advanced positioners that receive electronic control signals and convert them into precise pneumatic outputs. These positioners compare the desired valve position with actual stem position, adjusting air pressure to eliminate any deviation. Smart positioners feature digital communication capabilities, allowing remote monitoring and diagnostics through industrial networks. The control loop includes feedback mechanisms that continuously monitor valve position, providing real-time adjustments to maintain accuracy. Signal processing within pneumatic control valve systems accommodates various input signals including 4-20mA current loops, digital communication protocols, and discrete control inputs. Advanced diagnostic capabilities enable predictive maintenance scheduling, reducing unplanned downtime and optimizing system reliability across industrial applications.
Applications Across Different Industrial Sectors
Petrochemical and Oil Refining Operations
Petrochemical facilities rely extensively on pneumatic control valves for managing complex process streams involving hydrocarbons, acids, and high-temperature fluids. These environments demand robust valve construction with specialized materials capable of withstanding corrosive conditions while maintaining precise control performance. Pneumatic control valve applications in refineries include distillation column control, reactor temperature management, and pipeline pressure regulation. The intrinsic safety characteristics of pneumatic systems make them particularly suitable for hazardous area classifications where electrical equipment poses explosion risks. Specialized designs incorporate fire-safe construction, extended bonnet configurations for cryogenic services, and noise reduction features for environmental compliance. The reliability of pneumatic control valve systems in petrochemical applications directly impacts plant safety, product quality, and operational efficiency, making proper selection and maintenance critical for successful facility operations.
Power Generation and Steam Systems
Power generation facilities utilize pneumatic control valves throughout steam cycles, feedwater systems, and emission control equipment. These applications require valves capable of handling high-pressure, high-temperature conditions while providing rapid response to load changes. Steam turbine bypass systems depend on pneumatic control valve performance for plant startup sequences and emergency shutdown procedures. Feedwater control systems employ pneumatic actuators for their fast response characteristics and fail-safe capabilities during power outages. Coal-fired and gas-fired power plants integrate pneumatic control valves in combustion air control, fuel gas regulation, and flue gas treatment systems. The nuclear power industry specifically requires pneumatic control valve systems meeting stringent safety standards and seismic qualifications. Emergency core cooling systems and containment isolation applications demand proven reliability and rapid response capabilities that pneumatic actuation provides effectively.
Water Treatment and Municipal Services
Municipal water treatment facilities employ pneumatic control valves for chemical dosing, filtration backwash sequences, and distribution pressure management. These applications benefit from the linear control characteristics and fail-safe operation that pneumatic systems provide. Wastewater treatment plants utilize pneumatic control valve technology for aeration control, sludge handling, and effluent discharge regulation. The corrosive nature of water treatment chemicals requires specialized valve materials and coating systems to ensure long-term reliability. Pneumatic actuation eliminates electrical hazards in wet environments while providing the force necessary for large valve operations. Remote monitoring capabilities enable centralized control of distributed water systems, optimizing treatment processes and reducing operational costs. Advanced pneumatic control valve systems in water treatment incorporate smart positioners with diagnostic capabilities, enabling predictive maintenance and system optimization for improved service reliability and regulatory compliance.
Selection Criteria and Performance Optimization
Material Selection and Environmental Considerations
Proper material selection for pneumatic control valve components directly impacts service life and reliability in specific applications. Valve body materials must withstand process fluid characteristics including temperature, pressure, corrosivity, and abrasiveness. Stainless steel grades offer excellent corrosion resistance for general chemical service, while exotic alloys like Hastelloy or Inconel provide superior performance in severely corrosive environments. Trim materials including seats, plugs, and cages require careful selection based on flow characteristics, cavitation potential, and wear resistance requirements. Pneumatic control valve actuator materials must consider environmental exposure including temperature extremes, moisture, and chemical atmospheres. Diaphragm materials range from nitrile rubber for standard service to specialized elastomers for extreme temperature or chemical compatibility requirements. Proper material selection ensures optimal pneumatic control valve performance while minimizing maintenance requirements and extending service intervals.
Sizing and Flow Characteristics
Accurate sizing of pneumatic control valves ensures optimal process control while avoiding common problems like cavitation, noise, and premature wear. Flow coefficient (Cv) calculations must consider maximum and minimum flow requirements, available pressure differential, and fluid properties including viscosity and specific gravity. Inherent flow characteristics including linear, equal percentage, and quick opening profiles influence control loop stability and response. Equal percentage characteristics provide consistent control sensitivity across the operating range, making them suitable for most process applications. Linear characteristics offer constant gain but may result in poor control at low flows. Pneumatic control valve sizing software incorporates advanced calculations for two-phase flow, flashing, and cavitation prediction. Proper sizing prevents oversized valves that operate near closed positions, resulting in poor control and increased wear. Undersized pneumatic control valve installations create excessive pressure drops and may limit process capacity during peak demand periods.
Maintenance and Lifecycle Management
Effective maintenance programs for pneumatic control valve systems incorporate regular inspection schedules, predictive maintenance techniques, and systematic component replacement strategies. Air supply quality significantly impacts pneumatic actuator performance, requiring proper filtration, moisture removal, and pressure regulation. Contaminated air supplies cause premature wear of seals, erratic operation, and reduced actuator force output. Routine maintenance includes diaphragm inspection, packing adjustment, and positioner calibration verification. Smart positioners provide diagnostic information including valve signature analysis, which detects developing problems before failure occurs. Pneumatic control valve lifecycle management considers total cost of ownership including initial purchase price, installation costs, energy consumption, and maintenance expenses. Proper documentation of maintenance activities, performance trends, and failure analysis enables optimization of maintenance intervals and replacement strategies. Standardization of pneumatic control valve types and manufacturers reduces spare parts inventory requirements while simplifying maintenance procedures and training requirements.
Conclusion
Pneumatic control valves represent essential components in modern industrial automation, offering reliable performance across diverse applications from petrochemical processing to municipal water treatment. Their inherent safety characteristics, precise positioning capabilities, and fail-safe operation make them indispensable for critical process control applications. Understanding operating principles, proper selection criteria, and maintenance requirements ensures optimal system performance and extended service life for industrial facilities worldwide. Ready to enhance your industrial processes with reliable pneumatic control valve solutions? CEPAI Group combines exceptional durability with high-precision control performance, backed by extensive R&D investment and comprehensive industry certifications including API, ISO, and CE standards. Our expert technical team provides pre-sales consultation, customized solutions, and complete after-sales support including remote monitoring capabilities. With our proven track record serving major petrochemical companies and our commitment to zero-defect quality standards, we're your trusted partner for critical valve applications. Contact our specialists today at cepai@cepai.com to discuss your specific requirements and discover how our advanced pneumatic control valve technologies can optimize your operations while ensuring maximum safety and reliability.
References
1. Smith, J.R., Anderson, K.L., and Thompson, M.D. "Advanced Pneumatic Actuator Technologies for Industrial Control Applications." Journal of Process Control Engineering, vol. 45, no. 3, 2023, pp. 234-247.
2. Chen, L.W., Rodriguez, A.M., and Patel, S.K. "Material Selection and Performance Optimization in Pneumatic Control Valve Systems." Industrial Valve Technology Quarterly, vol. 28, no. 2, 2024, pp. 89-103.
3. Williams, R.T., Johnson, D.E., and Lee, M.H. "Safety and Reliability Assessment of Pneumatic Actuated Valves in Hazardous Area Applications." Process Safety and Environmental Protection, vol. 167, 2024, pp. 445-458.
4. Kumar, A.S., Brown, P.J., and Davis, C.R. "Predictive Maintenance Strategies for Pneumatic Control Valve Systems in Petrochemical Plants." Maintenance Engineering International, vol. 39, no. 4, 2023, pp. 156-171.
_1745994790767.webp)
Get professional pre-sales technical consultation and valve selection services, customized solution services.
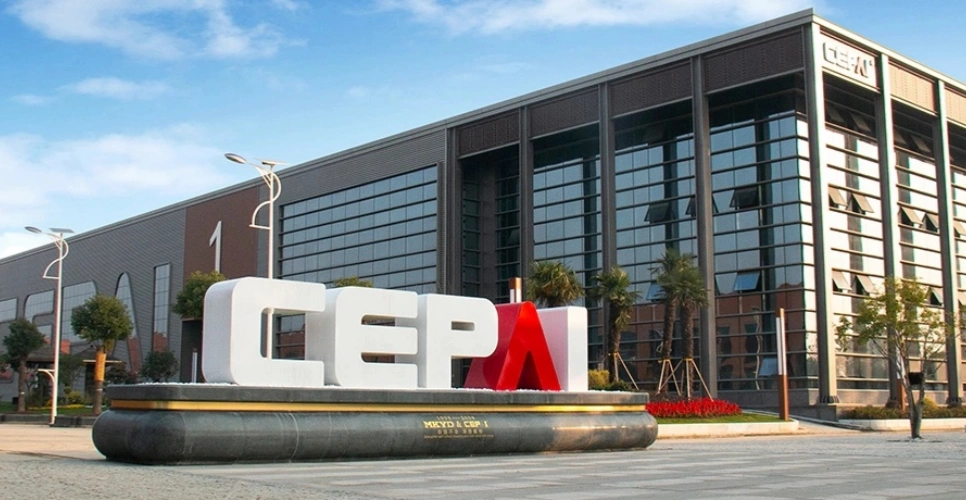
About CEPAI