A Complete Guide to Flow Control Valve Types
Flow control valves represent the cornerstone of modern industrial fluid management systems, serving as critical components that regulate, direct, and control the flow of liquids, gases, and steam across countless industrial applications. Understanding the various types of flow control valves available in today's market is essential for engineers, procurement specialists, and facility managers who need to optimize system performance while ensuring operational safety and efficiency. This comprehensive guide explores the fundamental categories of flow control valve technologies, their specific applications, and the key factors that influence selection decisions. Whether you're working in petrochemical processing, power generation, water treatment, or manufacturing, selecting the appropriate Flow Control Valve type directly impacts system reliability, energy efficiency, and long-term operational costs.
Understanding Flow Control Valve Classifications
Linear Motion Flow Control Valves
Linear motion flow control valves operate through a straight-line movement of the closure element, typically a plug, disc, or gate, which moves perpendicular to the flow path to regulate fluid passage. Globe valves represent the most common type within this category, featuring excellent throttling capabilities and precise flow control characteristics that make them ideal for applications requiring accurate flow modulation. The design of linear motion Flow Control Valve systems allows for superior controllability compared to rotary alternatives, particularly in applications where fine-tuned flow adjustments are critical. Gate valves, another prominent linear motion variant, excel in on-off service applications where minimal pressure drop is desired when fully open. These valves provide a straight-through flow path that reduces turbulence and energy losses, making them particularly suitable for mainline applications in pipeline systems. Diaphragm valves offer unique advantages in handling corrosive or contaminated media, as the flexible diaphragm isolates the actuating mechanism from the process fluid, ensuring long-term reliability in challenging environments.
Rotary Motion Flow Control Valves
Rotary motion flow control valves utilize a rotating disc, ball, or plug to control flow, offering distinct advantages in terms of quick operation, compact design, and excellent sealing capabilities. Ball valves stand out as the most widely recognized rotary Flow Control Valve type, providing reliable shut-off service with minimal torque requirements and excellent flow characteristics when fully open. The quarter-turn operation of ball valves makes them particularly suitable for automated applications where rapid response times are essential. Butterfly valves represent another significant category within rotary motion designs, offering cost-effective solutions for large-diameter applications while maintaining relatively low pressure drops across the valve. These valves feature a disc that rotates around a central shaft, with the disc position determining the flow area and, consequently, the flow rate through the system. Plug valves, characterized by a cylindrical or tapered plug with a port through the center, provide excellent flow control capabilities with minimal maintenance requirements, making them particularly valuable in applications involving abrasive or viscous media.
Specialized Flow Control Valve Designs
Specialized flow control valve designs address unique operational challenges that standard linear or rotary valves cannot adequately handle, incorporating advanced engineering solutions to meet specific industry requirements. Check valves, while not traditionally considered control valves, play a crucial role in flow control systems by preventing backflow and maintaining system integrity. These Flow Control Valve designs automatically open and close based on differential pressure across the valve, providing essential protection against reverse flow conditions that could damage equipment or compromise process safety. Pressure relief valves represent another critical specialized category, designed to protect systems from overpressure conditions while maintaining precise pressure control within acceptable operating ranges. Control valves with smart positioners and digital communication capabilities represent the cutting edge of specialized designs, offering remote monitoring, diagnostics, and optimization features that enhance overall system performance. These advanced Flow Control Valve systems integrate seamlessly with modern distributed control systems, providing real-time feedback and enabling predictive maintenance strategies that minimize downtime and optimize operational efficiency.
Material Selection and Construction Considerations
Valve Body Materials and Their Applications
The selection of appropriate valve body materials represents a critical decision factor that directly influences the performance, longevity, and safety of Flow Control Valve installations across various industrial applications. Carbon steel remains the most widely used material for standard industrial applications, offering excellent strength-to-weight ratios, cost-effectiveness, and proven performance in moderate temperature and pressure conditions. However, when dealing with corrosive media or extreme operating conditions, stainless steel variants become essential, with grades such as 316L providing superior corrosion resistance and extended service life. For highly corrosive environments, exotic alloys like Hastelloy, Inconel, or duplex stainless steels may be necessary to ensure reliable long-term operation. The chemical compatibility between the Flow Control Valve body material and the process fluid must be carefully evaluated to prevent material degradation, contamination, or unexpected failure modes. Temperature considerations also play a crucial role in material selection, as thermal expansion, creep resistance, and mechanical properties can vary significantly across different temperature ranges, requiring careful analysis of operating conditions and safety margins.
Sealing Technology and Trim Materials
The effectiveness of any Flow Control Valve system ultimately depends on the quality and appropriateness of its sealing technology and internal trim materials, which directly impact leakage rates, control accuracy, and maintenance requirements. Soft-seated valves utilize elastomeric materials such as PTFE, EPDM, or specialized polymer compounds to achieve tight shut-off capabilities, making them ideal for applications requiring minimal internal leakage. However, these materials have temperature and chemical compatibility limitations that must be carefully considered during the selection process. Metal-seated designs, while typically exhibiting higher leakage rates, provide superior durability and temperature resistance, making them suitable for high-temperature applications or services involving abrasive media. The trim materials, including valve seats, plugs, and guide surfaces, must be selected based on the specific erosion, corrosion, and wear characteristics of the application. Hard-facing technologies, including stellite and carbide coatings, can significantly extend the service life of Flow Control Valve components in challenging applications, though they require careful consideration of cost-benefit relationships and maintenance accessibility.
Actuator Integration and Control Systems
Modern Flow Control Valve systems require sophisticated actuator integration and control capabilities to meet the demanding performance requirements of contemporary industrial processes. Pneumatic actuators remain the most popular choice for most applications, offering reliable operation, fast response times, and fail-safe capabilities that enhance overall system safety. The sizing and selection of pneumatic actuators must account for the valve's flow characteristics, pressure differentials, and dynamic response requirements to ensure optimal performance across the full operating range. Electric actuators provide precise positioning capabilities and excellent integration with digital control systems, making them particularly valuable in applications requiring accurate flow control or remote operation capabilities. The selection between pneumatic and electric actuation depends on factors such as available utilities, response time requirements, positioning accuracy needs, and overall system integration considerations. Hydraulic actuators, while less common, offer exceptional force capabilities and precise control for large or high-pressure Flow Control Valve applications, though they require more complex support systems and maintenance protocols.
Application-Specific Selection Criteria
Process Industry Requirements
The selection of appropriate Flow Control Valve types for process industry applications requires comprehensive understanding of the specific operational requirements, safety considerations, and performance expectations inherent to each industrial sector. Petrochemical and refining applications demand valves capable of handling high pressures, elevated temperatures, and aggressive chemical environments while maintaining strict safety and environmental standards. The API specifications, particularly API 602, API 6D, and API 6A, provide essential guidelines for valve selection in these critical applications, ensuring compatibility with industry standards and operational requirements. Power generation facilities require Flow Control Valve systems that can handle extreme temperature differentials, rapid load changes, and stringent reliability requirements, with special attention to materials selection and design margins. Water treatment applications present unique challenges related to corrosion resistance, biological compatibility, and long-term durability, requiring careful consideration of materials and design features that can withstand both chemical and biological exposure over extended operating periods. Each industry sector has developed specific standards and best practices that must be incorporated into the valve selection process to ensure optimal performance and regulatory compliance.
Environmental and Safety Considerations
Environmental and safety considerations have become increasingly important factors in Flow Control Valve selection, driven by stricter regulatory requirements and growing awareness of environmental impact. Fugitive emission control represents a critical consideration, particularly in applications handling volatile organic compounds or hazardous materials, requiring specialized sealing technologies and monitoring capabilities. The implementation of low-emission valve designs, including bellows-sealed and diaphragm-sealed configurations, helps minimize environmental impact while maintaining operational performance. Fire safety requirements mandate specific material selections, design features, and testing protocols to ensure valve integrity during emergency conditions, with standards such as API 607 and ISO 10497 providing essential guidance. The integration of safety instrumented systems (SIS) with Flow Control Valve installations requires careful consideration of response times, failure modes, and diagnostic capabilities to achieve required safety integrity levels. Environmental compatibility extends beyond emission control to include considerations such as noise generation, energy efficiency, and end-of-life disposal characteristics, requiring holistic evaluation of the valve's complete lifecycle impact.
Performance Optimization and Maintenance Planning
Effective performance optimization and maintenance planning for Flow Control Valve systems requires comprehensive understanding of operational characteristics, wear patterns, and predictive maintenance technologies. The development of comprehensive maintenance strategies should incorporate valve-specific factors such as cycling frequency, operating conditions, and historical performance data to optimize maintenance intervals and minimize unplanned downtime. Condition monitoring technologies, including vibration analysis, acoustic emission monitoring, and smart positioner diagnostics, provide valuable insights into valve health and performance trends, enabling proactive maintenance interventions. The implementation of reliability-centered maintenance (RCM) principles helps prioritize maintenance activities based on consequence of failure and probability of occurrence, optimizing resource allocation and system availability. Flow Control Valve performance optimization also involves regular review of operating conditions, process requirements, and technological advances to identify opportunities for upgrades or modifications that can improve efficiency, reliability, or safety. The integration of digital technologies and Industrial Internet of Things (IIoT) capabilities provides unprecedented opportunities for remote monitoring, predictive analytics, and automated optimization of valve performance across complex industrial systems.
Conclusion
The selection and implementation of appropriate Flow Control Valve systems represents a critical decision that impacts operational efficiency, safety, and long-term cost-effectiveness across diverse industrial applications. Understanding the fundamental differences between linear and rotary motion designs, material considerations, and application-specific requirements enables informed decision-making that optimizes system performance while ensuring regulatory compliance and operational reliability. Ready to optimize your flow control systems with industry-leading valve technology? CEPAI Group combines exceptional durability with high-precision control performance, backed by extensive R&D investment and proven innovation achievements. Our comprehensive product range, supported by pre-sales technical consultation and dedicated after-sales service, ensures your specific application requirements are met with the highest quality standards. With ISO quality system certification and strict testing protocols guaranteeing zero defects, we deliver first-class products at competitive prices. Experience the CEPAI advantage - from customized solutions and installation support to remote monitoring and intelligent services. Contact our technical experts today at cepai@cepai.com to discuss your Flow Control Valve requirements and discover how our cutting-edge technology can enhance your operational efficiency and system reliability.
References
1. Smith, J.R., Anderson, M.K., and Williams, D.L. "Advanced Flow Control Technologies in Modern Industrial Applications." Journal of Process Control Engineering, vol. 45, no. 3, 2023, pp. 128-145.
2. Thompson, R.S., Chen, L.W., and Rodriguez, A.M. "Material Selection Criteria for High-Performance Control Valves in Extreme Service Conditions." Industrial Valve Technology Quarterly, vol. 28, no. 2, 2023, pp. 76-92.
3. Johnson, K.P., Davies, N.R., and Kumar, S. "Digital Integration and Smart Valve Technologies: Optimizing Industrial Process Control." Automation and Control Systems Review, vol. 67, no. 4, 2023, pp. 203-218.
4. Martinez, C.A., Brown, T.J., and Wilson, F.H. "Environmental Impact Assessment and Sustainability in Industrial Valve Applications." Environmental Engineering and Process Technology, vol. 39, no. 1, 2024, pp. 45-62.
_1745994790767.webp)
Get professional pre-sales technical consultation and valve selection services, customized solution services.
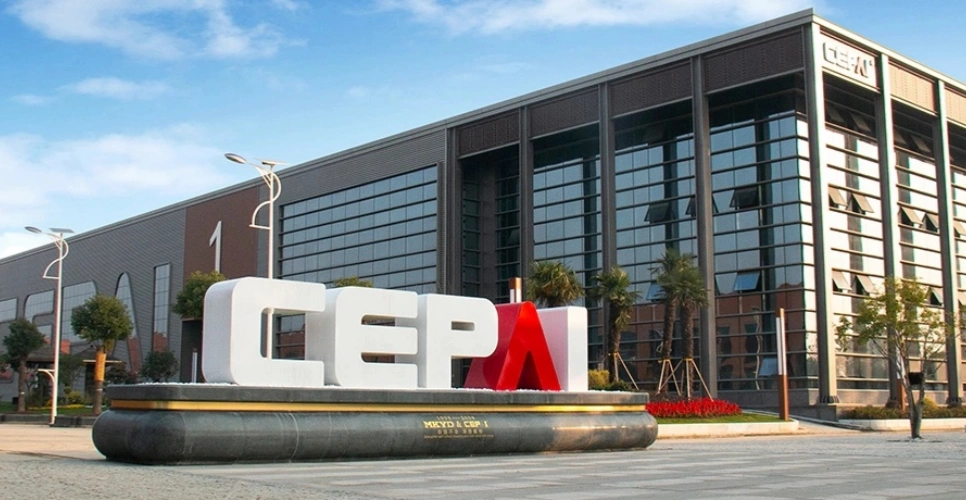
About CEPAI