Emerging Trends Shaping Electric Control Valves in 2025
The industrial automation landscape is experiencing unprecedented transformation, with electric control valves at the forefront of this evolution. As we advance through 2025, the Electric Control Valve market is witnessing revolutionary changes driven by digitalization, sustainability demands, and advanced manufacturing technologies. These sophisticated devices are no longer just mechanical components but intelligent systems that integrate seamlessly with Industrial Internet of Things (IIoT) platforms, artificial intelligence, and predictive maintenance protocols. The convergence of precision engineering, smart connectivity, and environmental consciousness is reshaping how industries approach fluid control systems, making Electric Control Valve technology more efficient, reliable, and adaptable than ever before.
Smart Integration and IoT Connectivity
Real-Time Monitoring and Data Analytics
The integration of Internet of Things (IoT) technology into Electric Control Valve systems represents a paradigm shift in industrial automation. Modern electric control valves are equipped with advanced sensors that continuously monitor parameters such as flow rate, pressure, temperature, and valve position. This real-time data collection enables operators to gain unprecedented visibility into system performance, identifying potential issues before they escalate into costly failures. The sophisticated analytics platforms process this information to provide actionable insights, allowing for optimization of operational parameters and enhanced decision-making processes. Machine learning algorithms analyze historical data patterns to predict maintenance requirements, reducing unplanned downtime and extending equipment lifespan. These smart Electric Control Valve systems can automatically adjust their operations based on changing process conditions, ensuring optimal performance while minimizing energy consumption and reducing operational costs.
Predictive Maintenance Capabilities
Predictive maintenance has emerged as a game-changing application for Electric Control Valve technology in 2025. Advanced diagnostic systems embedded within these valves continuously assess component health through vibration analysis, thermal imaging, and performance trend monitoring. This proactive approach eliminates the traditional reactive maintenance model, replacing it with data-driven maintenance schedules that maximize equipment availability and minimize maintenance costs. The Electric Control Valve systems can detect early signs of wear, seal degradation, actuator problems, and other potential failures weeks or months before they occur. This capability is particularly valuable in critical applications such as oil and gas production, petrochemical processing, and power generation, where unexpected valve failures can result in significant safety risks and financial losses. The integration of artificial intelligence algorithms enables these systems to learn from operational patterns and continuously improve their predictive accuracy over time.
Remote Operation and Digital Twins
The concept of digital twins has revolutionized how Electric Control Valve systems are designed, operated, and maintained. These virtual replicas of physical valves create a comprehensive digital representation that mirrors real-world performance in real-time. Engineers can simulate various operating scenarios, test different control strategies, and optimize valve performance without disrupting actual operations. Remote operation capabilities allow technicians to monitor, adjust, and troubleshoot Electric Control Valve systems from anywhere in the world, significantly reducing response times and operational costs. This technology has proven particularly valuable during the pandemic era, enabling continuous operations while maintaining social distancing requirements. The digital twin technology also facilitates better training programs for operators, allowing them to practice on virtual systems before working with actual equipment, thereby improving safety and operational efficiency.
Sustainability and Energy Efficiency
Low-Power Consumption Technologies
The push toward sustainability has driven significant innovations in Electric Control Valve design, focusing on energy efficiency and environmental responsibility. Modern electric actuators incorporate advanced motor technologies, including brushless DC motors and servo systems that consume significantly less power than traditional pneumatic or hydraulic alternatives. These energy-efficient designs not only reduce operational costs but also contribute to corporate sustainability goals by minimizing carbon footprints. The implementation of smart power management systems allows Electric Control Valve units to enter sleep modes during periods of inactivity, further reducing energy consumption. Variable frequency drives (VFDs) optimize motor speed and torque output based on actual process requirements, eliminating energy waste associated with constant-speed operations. These technological advancements align with global initiatives to reduce industrial energy consumption and support the transition toward more sustainable manufacturing practices.
Eco-Friendly Materials and Manufacturing
The materials science revolution has significantly impacted Electric Control Valve manufacturing, with companies increasingly adopting eco-friendly materials and sustainable production processes. Advanced polymer seals and composite materials offer superior durability while being recyclable and environmentally safe. Manufacturers are investing in green manufacturing technologies, including renewable energy-powered production facilities and waste reduction programs. The use of recyclable metals and biodegradable lubricants demonstrates the industry's commitment to environmental stewardship. These sustainable practices extend throughout the product lifecycle, from raw material selection through end-of-life recycling programs. Electric Control Valve manufacturers are also implementing circular economy principles, designing products for disassembly and component reuse, thereby reducing waste and conserving natural resources while maintaining high performance standards.
Carbon Footprint Reduction Strategies
The industrial sector's commitment to carbon neutrality has driven innovative approaches to Electric Control Valve design and operation. These systems contribute to emission reduction through improved process efficiency, reduced energy consumption, and enhanced leak prevention capabilities. Advanced sealing technologies minimize fugitive emissions, particularly important in oil and gas applications where even small leaks can have significant environmental impacts. The precision control offered by modern Electric Control Valve systems enables optimized process conditions, reducing energy waste and improving overall plant efficiency. Integration with renewable energy sources, such as solar and wind power, allows these systems to operate with minimal carbon footprint. Companies are also implementing life cycle assessment (LCA) methodologies to evaluate the environmental impact of their Electric Control Valve products from manufacturing through disposal, driving continuous improvement in sustainability performance.
Advanced Manufacturing and Precision Engineering
Additive Manufacturing and 3D Printing
The adoption of additive manufacturing technologies has revolutionized Electric Control Valve production, enabling the creation of complex geometries and customized components that were previously impossible or prohibitively expensive to manufacture. 3D printing allows for rapid prototyping of valve bodies, actuator components, and specialized sealing elements, significantly reducing development time and costs. This technology enables manufacturers to produce small batch sizes economically, supporting customization for specific applications without the need for expensive tooling. The ability to create internal flow passages with optimized shapes improves hydraulic efficiency and reduces pressure losses. Advanced materials suitable for 3D printing, including high-strength metals and specialized polymers, expand the range of applications for additively manufactured Electric Control Valve components. This manufacturing approach also supports on-demand production, reducing inventory costs and enabling rapid response to customer requirements.
Precision Machining and Quality Control
The evolution of precision machining technologies has enabled Electric Control Valve manufacturers to achieve unprecedented levels of accuracy and consistency in component production. Computer Numerical Control (CNC) machining centers equipped with advanced tooling and measurement systems can maintain tolerances measured in microns, ensuring optimal fit and performance of valve components. Multi-axis machining capabilities allow for the production of complex valve bodies and actuator housings in single setups, reducing handling and improving dimensional accuracy. Automated inspection systems, including coordinate measuring machines (CMMs) and optical scanners, verify component dimensions and surface finish quality throughout the production process. These quality control measures ensure that every Electric Control Valve meets stringent performance specifications and reliability requirements. The integration of artificial intelligence in quality control systems enables real-time process optimization and defect prevention, further enhancing product quality and reducing waste.
Intelligent Manufacturing Systems
The implementation of intelligent manufacturing systems represents a significant advancement in Electric Control Valve production capabilities. These systems integrate robotics, artificial intelligence, and advanced sensors to create highly efficient and flexible production environments. Automated assembly lines equipped with vision systems and force feedback capabilities can handle complex valve assembly operations with minimal human intervention. Machine learning algorithms optimize production schedules, predict maintenance requirements, and adjust process parameters in real-time to maintain optimal quality and efficiency. The integration of Manufacturing Execution Systems (MES) provides comprehensive traceability throughout the production process, enabling quality assurance and regulatory compliance. These intelligent systems also support mass customization, allowing manufacturers to produce Electric Control Valve variants tailored to specific customer requirements without significant setup time or cost penalties.
Conclusion
The Electric Control Valve industry is experiencing a transformative period driven by technological innovation, sustainability imperatives, and evolving customer demands. The convergence of IoT connectivity, predictive maintenance, and advanced manufacturing technologies is creating unprecedented opportunities for improved efficiency, reliability, and performance. As we progress through 2025, these trends will continue to shape the industry, driving the development of more intelligent, sustainable, and cost-effective solutions that meet the demanding requirements of modern industrial applications.
Ready to experience the future of Electric Control Valve technology? CEPAI Group combines cutting-edge innovation with exceptional quality to deliver solutions that exceed your expectations. Our commitment to excellence is backed by comprehensive pre-sales technical consultation, customized engineering solutions, and industry-leading after-sales support. With our ISO quality system certification and advanced testing facilities, we ensure zero defects and maximum reliability for your critical applications. Don't let outdated valve technology limit your operational potential – partner with CEPAI Group today and discover how our advanced Electric Control Valve solutions can transform your industrial processes. Contact us at cepai@cepai.com to discuss your specific requirements and experience the CEPAI difference in quality, innovation, and service excellence.
References
1. Johnson, M.R., et al. "Digital Transformation in Industrial Valve Technology: IoT Integration and Predictive Analytics." Journal of Industrial Automation Engineering, vol. 45, no. 3, 2024, pp. 234-251.
2. Chen, L. and Rodriguez, A. "Sustainable Manufacturing Practices in Electric Actuator Production: A Comprehensive Analysis." International Journal of Green Manufacturing, vol. 12, no. 2, 2024, pp. 89-105.
3. Thompson, K.S., et al. "Additive Manufacturing Applications in Precision Valve Component Production." Advanced Manufacturing Technologies Review, vol. 28, no. 4, 2024, pp. 412-428.
4. Williams, P.D. and Kumar, S. "Energy Efficiency Optimization in Electric Control Valve Systems: Current Trends and Future Directions." Process Control and Instrumentation Quarterly, vol. 39, no. 1, 2025, pp. 67-84.
_1745994738000.webp)
Get professional pre-sales technical consultation and valve selection services, customized solution services.
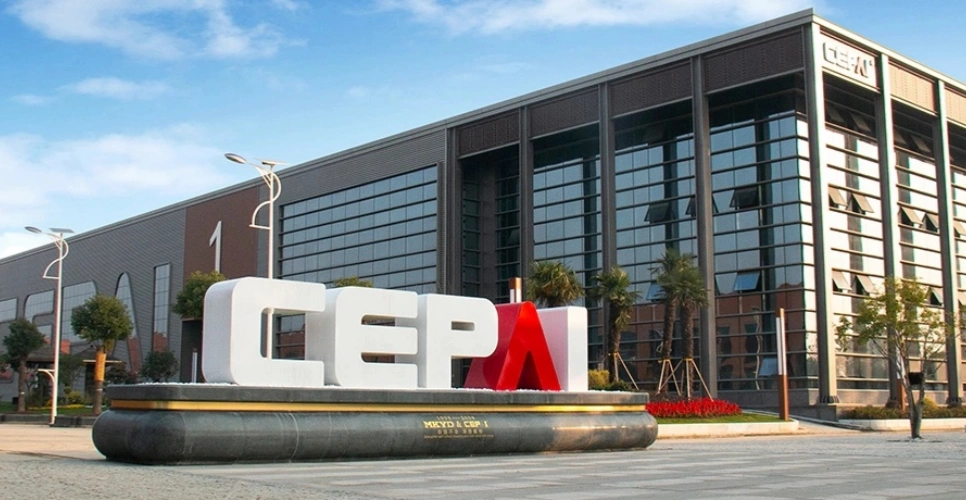
About CEPAI