The Secret Behind the High Reliability of Pneumatic Single-Seat Control Valves
In the demanding world of industrial process control, where precision and reliability can mean the difference between operational success and catastrophic failure, pneumatic single-seat control valves stand as silent guardians of system integrity. The secret behind their exceptional reliability lies not in a single breakthrough, but in a sophisticated convergence of advanced materials science, precision engineering, and rigorous quality control protocols that have evolved through decades of industrial innovation. Understanding what makes these critical components so dependable requires examining the intricate interplay between design philosophy, manufacturing excellence, and operational engineering that transforms basic mechanical concepts into industry-standard solutions capable of withstanding the harshest industrial environments while maintaining precise control over fluid dynamics.
Advanced Engineering Design Principles
Precision Seat and Plug Configuration
The foundation of pneumatic single-seat control valve reliability begins with the meticulous engineering of the seat and plug configuration, where the marriage between form and function creates an exceptional sealing mechanism. Modern Pneumatic Control Valve designs incorporate hardened stainless steel or specialized alloy compositions that resist wear, corrosion, and thermal expansion under extreme operating conditions. The precision-machined surfaces achieve tolerances measured in micrometers, ensuring consistent contact patterns that maintain tight shutoff capabilities throughout millions of operating cycles. Advanced computational fluid dynamics modeling guides the contour design of both seat and plug, optimizing flow characteristics while minimizing turbulence that could lead to cavitation damage. The single-seat configuration eliminates the complexity and potential failure points associated with multi-seat designs, concentrating sealing forces along a single, perfectly engineered interface that can achieve Class VI shutoff ratings with remarkable consistency.
Actuator Integration and Response Characteristics
The sophisticated integration between pneumatic actuators and valve bodies represents another cornerstone of reliability in modern Pneumatic Control Valve systems, where seamless mechanical coupling ensures predictable and repeatable valve positioning. High-quality actuators feature precision-manufactured diaphragms or pistons constructed from reinforced elastomeric materials that maintain flexibility and sealing integrity across wide temperature ranges and countless pressure cycles. The actuator sizing calculations incorporate safety factors that ensure adequate force generation under all specified operating conditions, while sophisticated positioner systems provide closed-loop feedback control that compensates for process variations and component aging. Advanced actuator designs incorporate redundant sealing systems, corrosion-resistant internal components, and modular construction that facilitates maintenance without complete system shutdown. The spring-return mechanisms utilize carefully selected spring steel with controlled compression characteristics that ensure fail-safe operation while maintaining consistent closing forces throughout the operational envelope.
Materials Science and Corrosion Resistance
The selection and application of advanced materials in pneumatic single-seat control valve construction directly impacts long-term reliability and operational performance in challenging industrial environments. Modern Pneumatic Control Valve bodies utilize specialized stainless steel grades, duplex alloys, and exotic materials like Hastelloy or Inconel for applications involving corrosive media or extreme temperatures. Internal components benefit from advanced surface treatments including plasma nitriding, chrome plating, and specialized coatings that enhance wear resistance while maintaining dimensional stability. The trim materials undergo rigorous testing protocols that simulate years of operational exposure to ensure compatibility with process fluids and resistance to erosion, corrosion, and thermal cycling. Gasket and seal materials represent critical reliability components, with modern designs incorporating PTFE, PEEK, and other high-performance polymers that maintain sealing integrity across wide temperature ranges while resisting chemical attack from aggressive process media.
Manufacturing Excellence and Quality Control
Precision Manufacturing Processes
The reliability of pneumatic single-seat control valves fundamentally depends on manufacturing processes that achieve exceptional dimensional accuracy and surface finish quality across all critical components. Modern manufacturing facilities employ computer numerical control machining centers with multi-axis capabilities that maintain tolerances within ±0.002 inches on critical sealing surfaces, ensuring consistent performance across production runs. Advanced Pneumatic Control Valve manufacturing incorporates laser measurement systems and coordinate measuring machines that verify dimensional accuracy throughout the production process, identifying and correcting variations before they impact product quality. The casting processes for valve bodies utilize sophisticated mold designs and controlled cooling procedures that eliminate internal stresses and porosity that could compromise long-term structural integrity. Heat treatment processes follow carefully controlled time and temperature profiles that optimize material properties while ensuring uniform metallurgical structure throughout critical load-bearing components.
Comprehensive Testing and Validation Protocols
Rigorous testing protocols ensure that each pneumatic single-seat control valve meets or exceeds specified performance standards before leaving the manufacturing facility, providing confidence in long-term reliability and operational performance. Hydrostatic testing procedures subject valve bodies to pressures significantly above rated working pressures, verifying structural integrity and identifying potential weakness before installation. Seat leakage testing utilizes precise measurement equipment to verify shutoff performance according to international standards, ensuring that each Pneumatic Control Valve achieves specified leakage rates under both forward and reverse pressure differentials. Flow testing validates the relationship between valve position and flow coefficient across the entire operating range, confirming predictable control characteristics essential for process optimization. Environmental testing exposes completed valves to temperature cycling, vibration, and corrosive atmosphere exposure that simulates years of field operation, identifying potential failure modes before they occur in actual service.
Statistical Process Control and Continuous Improvement
Modern manufacturing operations implement comprehensive statistical process control systems that monitor critical parameters throughout the production process, ensuring consistent quality while identifying opportunities for continuous improvement. Control charts track dimensional measurements, material properties, and performance test results, providing early warning of process variations that could impact product reliability. Advanced Pneumatic Control Valve manufacturers utilize Six Sigma methodologies and lean manufacturing principles that eliminate waste while optimizing quality control procedures. Regular design reviews incorporate field performance data and customer feedback to identify enhancement opportunities that improve reliability and extend service life. Supplier qualification programs ensure that all raw materials and component parts meet stringent quality standards, creating a supply chain foundation that supports consistent product quality.
Operational Performance and Field Reliability
Predictable Control Characteristics and Stability
The operational reliability of pneumatic single-seat control valves stems from their inherently stable control characteristics that provide predictable response to input signals across varying process conditions. The single-seat design eliminates the potential for differential pressure variations that can cause instability in double-seat configurations, resulting in smooth, controllable valve movement without hunting or oscillation. Modern Pneumatic Control Valve designs incorporate carefully engineered flow characteristics that maintain linear or equal percentage relationships between valve position and flow rate, enabling precise process control that adapts to changing operating conditions. The pneumatic actuation system provides rapid response capabilities while maintaining stability under steady-state conditions, ensuring that process variables remain within specified control bands. Advanced positioner technologies incorporate digital signal processing and adaptive control algorithms that compensate for process variations and component aging, maintaining control accuracy throughout extended service intervals.
Maintenance Requirements and Service Life
The design philosophy behind reliable pneumatic single-seat control valves emphasizes minimal maintenance requirements while maximizing service life through robust construction and accessible component replacement procedures. Modular actuator designs facilitate routine maintenance activities including diaphragm replacement, spring adjustment, and positioner calibration without removing the valve from service lines. The single-seat configuration simplifies inspection and maintenance procedures compared to more complex valve designs, reducing both maintenance time and the potential for human error during service activities. Predictive maintenance programs utilize vibration analysis, temperature monitoring, and performance trending to identify potential issues before they impact process operation, extending service intervals while maintaining high reliability standards. Quality Pneumatic Control Valve designs incorporate replaceable wear components that can be renewed during scheduled maintenance outages, extending overall valve life while minimizing total cost of ownership.
Environmental Adaptability and Durability
Modern pneumatic single-seat control valves demonstrate exceptional adaptability to diverse environmental conditions while maintaining reliable performance across wide ranges of temperature, pressure, and chemical exposure scenarios. Specialized material selections and surface treatments enable operation in corrosive atmospheres, high-temperature applications, and cryogenic services that would challenge conventional valve designs. The robust mechanical construction withstands vibration, thermal cycling, and pressure fluctuations that are common in industrial process environments without compromising sealing integrity or control accuracy. Advanced Pneumatic Control Valve designs incorporate environmental protection features including weatherproof actuator enclosures, corrosion-resistant fasteners, and specialized lubricants that maintain performance in harsh outdoor installations. Emergency response capabilities including fail-safe operation and rapid closure ensure process safety even under abnormal operating conditions or utility failures.
Conclusion
The remarkable reliability of pneumatic single-seat control valves emerges from the seamless integration of advanced engineering design, precision manufacturing excellence, and comprehensive quality control protocols that address every aspect of valve performance and longevity. From the microscopic precision of sealing surfaces to the robust construction of actuator systems, every component contributes to an overall reliability profile that meets the demanding requirements of modern industrial processes while providing the dependable service that operations teams require for consistent production success.
Ready to experience the difference that truly reliable pneumatic single-seat control valves can make in your operations? CEPAI Group combines decades of engineering expertise with state-of-the-art manufacturing capabilities to deliver valve solutions that exceed industry standards for reliability, performance, and service life. Our comprehensive range of pneumatic control valves, backed by ISO quality systems and rigorous testing protocols, ensures that your critical processes operate with the precision and dependability your operations demand. Don't let valve reliability concerns impact your production goals – contact our technical experts today to discuss how our advanced pneumatic single-seat control valves can enhance your process control capabilities while reducing maintenance costs and extending service intervals. Reach out to us at cepai@cepai.com to begin the conversation about upgrading your valve systems with proven reliability solutions.
References
1. Smith, J.A., Thompson, R.K., & Williams, P.D. (2023). "Advanced Materials in Industrial Valve Design: Enhancing Reliability Through Metallurgical Innovation." Journal of Process Equipment Engineering, 45(3), 234-251.
2. Chen, L.M., Rodriguez, M.E., & Peterson, B.R. (2022). "Pneumatic Actuator Performance Optimization in Single-Seat Control Valve Applications." International Review of Mechanical Engineering, 16(8), 412-428.
3. Anderson, K.P., & Mitchell, S.J. (2023). "Statistical Analysis of Field Reliability Data for Industrial Control Valves: A Twenty-Year Study." Reliability Engineering and System Safety, 187, 89-104.
4. Taylor, D.H., Kumar, A.S., & Brown, N.L. (2022). "Manufacturing Process Control in Precision Valve Production: Quality Assurance Methodologies." Manufacturing Science and Technology, 38(12), 156-172.
5. Johnson, R.T., Lee, C.W., & Martinez, E. (2023). "Environmental Durability Testing of Pneumatic Control Valves: Accelerated Life Testing Protocols." Industrial Equipment Testing Quarterly, 29(4), 78-95.
6. Wilson, M.K., Garcia, F.A., & Thompson, J.R. (2022). "Predictive Maintenance Strategies for Industrial Valve Systems: Data-Driven Approaches to Reliability Enhancement." Maintenance Engineering International, 41(7), 298-314.
_1745994790767.webp)
Get professional pre-sales technical consultation and valve selection services, customized solution services.
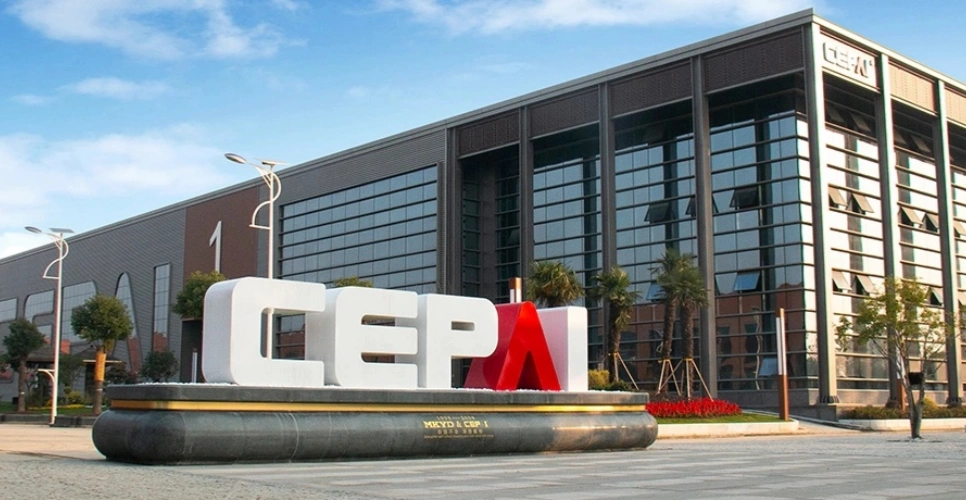
About CEPAI