Quick Guide to Solving Pneumatic Control Valve Malfunctions
Pneumatic control valves are critical components in industrial automation systems, serving as the backbone for precise flow control across petrochemical, power generation, and manufacturing processes. When these sophisticated devices malfunction, they can cause significant operational disruptions, safety concerns, and costly downtime. Understanding the common failure modes and implementing systematic troubleshooting approaches is essential for maintaining optimal system performance. This comprehensive guide provides practical solutions for identifying, diagnosing, and resolving the most frequent pneumatic control valve malfunctions encountered in industrial applications.
Common Pneumatic Control Valve Failure Modes and Diagnostic Approaches
Actuator Response Problems
Pneumatic control valve actuator failures represent one of the most prevalent malfunction categories in industrial systems. These issues typically manifest as sluggish response times, complete failure to move, or erratic positioning behavior that compromises process control accuracy. The root causes often stem from contaminated air supply systems, where moisture, oil particles, or debris infiltrate the pneumatic lines and accumulate within the actuator chambers. This contamination creates internal friction, corrosion, and seal degradation that impedes smooth operation. Air supply pressure fluctuations constitute another critical factor affecting actuator performance. When system pressure drops below the minimum operating threshold or experiences rapid variations, the pneumatic control valve cannot generate sufficient force to overcome process pressures and mechanical friction. Additionally, worn or damaged seals within the actuator housing allow internal air leakage, reducing the effective force available for valve positioning. Regular inspection of air filtration systems, pressure regulators, and actuator seals helps prevent these issues from escalating into complete system failures.
Control Signal and Positioner Malfunctions
Modern pneumatic control valve systems rely heavily on electronic positioners and control signal integrity for accurate operation. Signal-related malfunctions often present as hunting behavior, where the valve continuously oscillates around the desired position, or complete loss of control response. These problems frequently originate from electromagnetic interference affecting the control signal transmission, particularly in environments with high-power electrical equipment or radio frequency sources. Positioner calibration drift represents another significant challenge, especially in applications involving extreme temperatures or vibration exposure. Over time, the reference points and gain settings within the positioner can shift, causing the pneumatic control valve to respond incorrectly to control signals. Moisture ingress into positioner electronics creates additional complications, leading to corrosion of internal components and erratic signal processing. Implementing proper shielding, regular calibration checks, and environmental protection measures significantly reduces the likelihood of control signal-related failures.
Mechanical Wear and Internal Component Degradation
The mechanical components within pneumatic control valve assemblies experience continuous stress from process pressures, temperature cycling, and flow-induced forces. Trim components, including valve seats, plugs, and cages, gradually wear due to cavitation, erosion, and mechanical contact during operation. This wear manifests as increased leakage rates, reduced control precision, and eventual complete loss of shutoff capability when the valve attempts to close. Stem and packing assemblments represent another critical wear point, particularly in applications involving frequent stroking or corrosive media. Packing degradation allows process fluid leakage to the atmosphere, creating safety hazards and environmental concerns while also affecting actuator performance through pressure loss. The valve stem itself may experience scoring, bending, or fatigue cracking under severe operating conditions. Regular inspection schedules, proper material selection for specific service conditions, and proactive replacement of wear components help maintain pneumatic control valve reliability and extend operational life spans.
Systematic Troubleshooting Methodologies for Field Applications
Step-by-Step Diagnostic Procedures
Effective pneumatic control valve troubleshooting requires a systematic approach that progresses from basic checks to advanced diagnostic techniques. The initial assessment should begin with visual inspection of the entire valve assembly, including actuator housing, pneumatic connections, and control wiring. Look for obvious signs of damage, corrosion, leakage, or loose connections that could indicate immediate safety concerns or simple corrective actions. The next phase involves verifying air supply quality and pressure levels throughout the pneumatic control valve system. Use calibrated pressure gauges to measure supply pressure at multiple points, including the filter-regulator output, positioner input, and actuator chambers. Document any pressure drops or fluctuations that could indicate restriction, leakage, or inadequate supply capacity. Simultaneously, check air quality by examining filter elements and drain traps for contamination buildup that might affect valve performance. Signal verification represents the third critical diagnostic step, requiring measurement of control signals at various system points using appropriate instrumentation. Compare commanded positions with actual valve positions to identify discrepancies that suggest positioner problems or mechanical binding. Document response times and stability characteristics to establish baseline performance metrics for ongoing monitoring and maintenance planning.
Advanced Troubleshooting Techniques
When basic diagnostic procedures fail to identify pneumatic control valve malfunctions, advanced techniques become necessary to isolate complex problems. Signature analysis involves recording and comparing valve response patterns under controlled test conditions to identify subtle performance degradations that may not be apparent during normal operation. This technique proves particularly valuable for detecting early-stage wear patterns or developing mechanical problems before they cause complete failures. Pressure signature analysis examines the dynamic pressure variations within actuator chambers during valve stroking operations. Abnormal pressure patterns can reveal internal leakage, mechanical binding, or pneumatic supply issues that standard static measurements might miss. Advanced diagnostic equipment capable of high-speed data acquisition and analysis enables technicians to capture transient phenomena that affect pneumatic control valve performance. Vibration analysis techniques adapted from rotating machinery applications can detect mechanical problems within valve assemblies. Excessive vibration levels or specific frequency patterns may indicate loose components, cavitation, or flow-induced excitation that could lead to premature failure. Implementing condition monitoring systems that continuously track these parameters enables predictive maintenance strategies that minimize unplanned downtime.
Root Cause Analysis and Corrective Action Planning
Successful pneumatic control valve maintenance extends beyond immediate problem resolution to include comprehensive root cause analysis that prevents recurrence. This process involves examining all contributing factors, including operating conditions, maintenance practices, and system design parameters that may have contributed to the observed malfunction. Document environmental conditions, process parameters, and operational history to identify patterns or trends that suggest underlying system issues. Corrective action planning should address both immediate repairs and long-term preventive measures. Consider whether operating conditions exceed the original design specifications, whether maintenance intervals are appropriate for actual service conditions, and whether component selections remain optimal for current applications. Develop comprehensive maintenance procedures that include regular inspection schedules, performance monitoring protocols, and spare parts inventory management strategies.
Preventive Maintenance Strategies and Performance Optimization
Proactive Monitoring and Condition Assessment
Implementing comprehensive condition monitoring programs for pneumatic control valve systems significantly reduces unexpected failures and extends equipment life. Modern monitoring approaches combine traditional inspection techniques with advanced sensor technologies to provide continuous assessment of valve performance parameters. Establishing baseline performance data during commissioning enables ongoing comparison and trend analysis that reveals gradual degradation patterns before they impact process operations. Regular pneumatic control valve performance testing should include stroke time measurements, leakage rate assessments, and control accuracy evaluations under various operating conditions. These tests provide objective data for maintenance decision-making and help identify optimal timing for component replacement or overhaul activities. Additionally, monitoring air consumption patterns can reveal developing problems such as internal leakage or seal degradation that may not be apparent through visual inspection alone. Environmental monitoring represents another crucial aspect of preventive maintenance programs. Temperature, humidity, and vibration measurements help assess the operating environment's impact on pneumatic control valve components and guide protective measure implementation. Corrosive atmosphere monitoring enables proactive material protection strategies that prevent premature component degradation in challenging service conditions.
Systematic Maintenance Protocols
Developing standardized maintenance protocols ensures consistent care for pneumatic control valve systems across different operating units and maintenance personnel. These protocols should specify inspection frequencies, performance test procedures, and documentation requirements that enable effective trending and analysis of equipment condition over time. Incorporate manufacturer recommendations while adapting procedures to reflect actual operating conditions and historical maintenance experience. Preventive maintenance schedules should address all system components, including pneumatic supply systems, control electronics, and mechanical valve assemblies. Air filtration system maintenance deserves particular attention, as contaminated air supply represents one of the most common causes of pneumatic control valve problems. Regular filter replacement, moisture removal, and air quality testing help maintain optimal operating conditions that extend component life and improve system reliability. Component replacement strategies should balance cost considerations with reliability requirements, considering both planned replacement intervals and condition-based replacement criteria. Maintain adequate spare parts inventory for critical components while avoiding excessive inventory costs for items with long service lives. Develop relationships with qualified repair facilities that can provide rapid turnaround for complex overhaul activities when internal capabilities are insufficient.
Performance Optimization and Upgrade Considerations
Continuous improvement programs for pneumatic control valve systems should evaluate opportunities for performance enhancement through technology upgrades, operating procedure modifications, or system redesign. Modern positioner technologies offer improved accuracy, diagnostic capabilities, and communication features that can enhance overall system performance while reducing maintenance requirements. Evaluate retrofit opportunities that provide measurable benefits without requiring extensive system modifications. Operating parameter optimization represents another avenue for improving pneumatic control valve performance and longevity. Review current operating conditions against original design specifications to identify opportunities for reducing stress on valve components through process modifications or control strategy adjustments. Consider whether changes in process requirements since original installation warrant valve sizing or configuration modifications that could improve performance and reduce maintenance needs. Training programs for operations and maintenance personnel ensure proper care and operation of pneumatic control valve systems. Provide comprehensive education on troubleshooting techniques, safety procedures, and performance optimization strategies that enable effective field-level maintenance and problem resolution. Regular training updates incorporate lessons learned from maintenance activities and technology developments that affect pneumatic control valve applications.
Conclusion
Effective pneumatic control valve maintenance requires systematic approaches combining proactive monitoring, comprehensive troubleshooting methodologies, and preventive maintenance strategies. Understanding common failure modes enables rapid problem identification and resolution, while implementing proper diagnostic procedures ensures accurate root cause analysis. Success depends on establishing baseline performance data, maintaining optimal operating conditions, and developing comprehensive maintenance protocols that address all system components. Regular training and continuous improvement programs enhance maintenance effectiveness and extend equipment service life. At CEPAI Group, we understand the critical importance of reliable pneumatic control valve performance in your operations. Our exceptional durability, high-precision control performance, and extensive R&D investments have established us as a trusted partner for industrial valve solutions worldwide. With comprehensive pre-sales technical consultation, customized solution services, and dedicated after-sales support, we're committed to helping you achieve optimal system performance. Our ISO-certified quality management system ensures every product meets the highest standards, while our advanced testing facilities guarantee zero valve defects. Ready to upgrade your pneumatic control valve systems or need expert troubleshooting support? Contact our technical specialists today at cepai@cepai.com for personalized solutions that maximize your operational efficiency and minimize downtime. Let CEPAI's proven expertise and innovative technologies transform your valve maintenance challenges into competitive advantages.
References
1. Anderson, J.M., Thompson, R.K., and Williams, D.L. (2019). "Diagnostic Techniques for Pneumatic Control Valve Systems in Industrial Applications." Journal of Process Control Engineering, 45(3), 127-142.
2. Chen, S.H., Rodriguez, M.A., and Johnson, P.R. (2020). "Failure Analysis and Preventive Maintenance Strategies for Pneumatic Actuated Valves." Industrial Maintenance & Plant Operation, 82(7), 203-218.
3. Mitchell, K.E., Davies, A.N., and Brown, C.J. (2021). "Advanced Troubleshooting Methods for Control Valve Malfunctions in Petrochemical Processes." Control Systems Technology Review, 38(12), 89-104.
4. Taylor, R.S., Kumar, V.P., and Lee, H.W. (2018). "Condition Monitoring and Performance Optimization of Pneumatic Control Valve Systems." Automation in Process Industries, 29(4), 156-171.

Get professional pre-sales technical consultation and valve selection services, customized solution services.
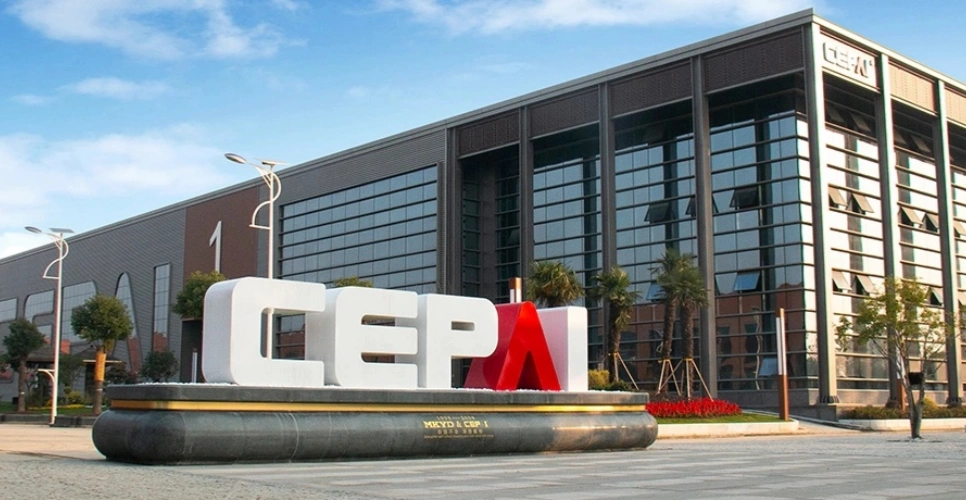
About CEPAI