How to Choose the Right Control Valve for Your Process?
Selecting the appropriate Control Valves for your industrial process is a critical decision that directly impacts operational efficiency, system performance, and long-term reliability. Control valves serve as the final control element in process systems, regulating flow rates, pressures, temperatures, and liquid levels by responding to signals from controllers. The right control valve selection ensures optimal process control, minimizes maintenance costs, extends equipment lifespan, and enhances overall system safety. This comprehensive guide will walk you through the essential considerations and methodologies for selecting the perfect control valve tailored to your specific industrial application requirements.
Understanding Control Valve Fundamentals
Control Valve Types and Their Applications
Control Valves come in various designs, each optimized for specific applications and operating conditions. Globe valves, with their linear motion, are excellent for precise throttling applications and are commonly used in steam systems and high-pressure drop scenarios. Their design allows for excellent control characteristics across various flow rates, making them indispensable in processes requiring fine adjustments. Ball valves offer quick quarter-turn operation and provide tight shutoff capabilities, making them ideal for on-off applications and situations requiring minimal pressure drop. Their full-bore design ensures minimal flow restriction when fully open, which is crucial for applications where pressure loss must be minimized. Butterfly valves feature a disc that rotates around a central axis, offering economical flow control for large diameter applications where space and weight constraints exist. These Control Valves are particularly valuable in water treatment facilities, HVAC systems, and processes involving slurries or large volumes of fluid where precise control isn't the primary concern but reliable operation under challenging conditions is essential. Understanding the inherent characteristics of each valve type is fundamental to making an informed selection that aligns with your process requirements and operational parameters.
Critical Performance Parameters
When selecting Control Valves, several critical performance parameters must be carefully evaluated to ensure optimal system operation. The flow coefficient (Cv) is perhaps the most fundamental parameter, indicating the valve's capacity to pass flow under specific pressure conditions. Properly sized valves with appropriate Cv values prevent issues like cavitation, flashing, and excessive noise while ensuring the valve operates within its optimal control range. Rangeability—the ratio between maximum and minimum controllable flow rates—determines the valve's ability to handle varying process conditions. High-performance Control Valves typically offer a rangeability of 50:1 or greater, allowing them to maintain precise control across wide operational spans. Response time measures how quickly the valve reacts to control signals, which is crucial in processes requiring rapid adjustments to maintain product quality or safety parameters. Additionally, characteristic curves (linear, equal percentage, or quick-opening) define how the valve's flow capacity changes relative to its position. Selecting the appropriate characteristic ensures stable process control by matching the valve's behavior to the process gain, particularly important in systems with varying pressure differentials or in cascade control loops where Control Valves must respond predictably across their entire operational range.
Installation and Environmental Considerations
The proper installation and environmental compatibility of Control Valves significantly impact their performance and longevity. Valve orientation must follow manufacturer recommendations, with consideration given to gravity effects, process fluid properties, and actuator requirements. Upstream and downstream straight pipe lengths are critical for stable flow profiles and accurate control, with most valve manufacturers specifying minimum requirements to prevent turbulence-induced issues. Environmental factors, including ambient temperature ranges, humidity levels, and exposure to corrosive atmospheres, must be carefully assessed when selecting valve materials and actuator types. Control Valves operating in extreme environments may require special materials, coatings, or enclosures to maintain reliability. Space constraints often dictate valve selection, particularly in retrofit applications where compact designs might be necessary despite potentially compromising on ideal performance characteristics. Additionally, vibration conditions require special attention, as excessive vibration can lead to premature component failure, loose connections, and control instability. Properly anchored piping systems, vibration dampeners, and robust valve designs help mitigate these risks. For Control Valves deployed in hazardous areas, compliance with explosion-proof requirements and appropriate certification becomes mandatory, necessitating specially designed actuators, positioners, and accessories that meet relevant safety standards while maintaining precise control functionality.
Process Compatibility and System Integration
Material Selection and Compatibility
Selecting appropriate materials for Control Valves requires a thorough understanding of process fluids and operating conditions to ensure longevity and reliable performance. Material compatibility with process media is paramount—corrosive chemicals may necessitate exotic alloys like Hastelloy or titanium, while food and pharmaceutical applications often require FDA-approved stainless steel with specific surface finishes. Temperature extremes significantly impact material selection, as certain metals lose strength at elevated temperatures or become brittle in cryogenic applications. High-temperature applications may require special alloys like Inconel or ceramic components, while low-temperature services need materials that maintain ductility and impact resistance even in sub-zero conditions. Erosion resistance becomes critical when handling slurries or fluids containing abrasive particles, potentially requiring hardened surfaces, stellite facings, or ceramic components to maintain acceptable service life. Control Valves handling clean fluids can utilize standard materials, while those exposed to erosive media benefit from hardened components and streamlined flow paths that minimize impingement damage. Additionally, consideration must be given to potential galvanic corrosion when dissimilar metals interact in the presence of an electrolyte, requiring careful selection of compatible materials or appropriate isolation techniques. CEPAI Group's Control Valves incorporate advanced material science with options ranging from standard carbon steel to highly specialized alloys engineered specifically for challenging applications in the petrochemical, power generation, and water treatment industries.
Integration with Control Systems
Modern Control Valves must seamlessly integrate with automated control systems to deliver optimal process performance and facilitate comprehensive monitoring capabilities. Communication protocols play a crucial role in this integration—traditional analog 4- 20mA signals provide robust, simple connectivity while digital protocols like HART, Foundation Fieldbus, and Profibus enable advanced diagnostics and remote parameterization. These digital communications allow operators to access valve position, actuator status, and diagnostic information from central control rooms, enhancing system visibility and facilitating predictive maintenance strategies. Smart positioners equipped on advanced Control Valves provide precise positioning accuracy while continuously monitoring valve performance parameters, including cycle count, total travel, and deviation from setpoint. This data enables condition-based maintenance approaches that optimize maintenance intervals based on actual valve condition rather than arbitrary schedules. Fail-safe configurations—including fail-open, fail-closed, and fail-last position—must align with process safety requirements to ensure appropriate system response during power or signal loss. Control Valves in emergency shutdown applications may require SIL certification to comply with functional safety standards, with documentation verifying their reliability in safety-critical applications. CEPAI's Control Valves feature advanced positioners compatible with multiple communication protocols, allowing seamless integration with distributed control systems while providing comprehensive diagnostic data that enhances operational visibility and facilitates predictive maintenance strategies essential for modern industrial operations.
Sizing and Selection Methodology
Proper sizing methodology is fundamental to selecting Control Valves that provide stable, accurate process control across all operating conditions. The process begins with gathering comprehensive application data, including flow rates (normal, maximum, and minimum), inlet and outlet pressures, temperature ranges, fluid properties, and required control precision. These parameters serve as inputs to sizing calculations that determine appropriate valve dimensions and characteristics. Accurate sizing prevents common issues like oversizing, which leads to poor control resolution and hunting, and undersizing, which restricts flow capacity and reduces system efficiency. Control Valves must accommodate both steady-state conditions and transient operations such as startup, shutdown, and process disturbances without compromising control stability. Computational methods have evolved from traditional manual calculations to sophisticated software tools that account for complex fluid behaviors, pressure recovery factors, and noise prediction. These advanced sizing programs incorporate international standards, including IEC 60534 and ISA-75.01, to ensure consistent, reliable results across diverse applications. Control valve authority—the ratio of pressure drop across the valve to the total system pressure drop—should ideally fall between 0.3 and 0.7 to ensure the valve has sufficient influence over the process while avoiding excessive energy consumption. CEPAI's engineering team employs proprietary sizing software incorporating decades of field experience and empirical data to ensure their Control Valves are precisely matched to application requirements, optimizing control performance while minimizing energy consumption and operational costs across diverse industrial applications.
Maintenance Considerations and Lifecycle Costs
Preventive Maintenance Strategies
Implementing effective preventive maintenance strategies for Control Valves significantly extends service life while reducing unplanned downtime and operational disruptions. Regular inspection routines should include visual examinations for leakage, corrosion, and mechanical damage, alongside periodic functional testing to verify proper operation across the valve's full travel range. Diagnostic technologies have revolutionized maintenance approaches—acoustic emission analysis can detect internal leakage before it becomes severe, while signature analysis provides comprehensive insights into actuator performance, friction profiles, and potential mechanical issues. These non-intrusive diagnostic methods allow maintenance personnel to assess valve condition without process interruption, enabling condition-based maintenance strategies that optimize maintenance intervals based on actual equipment health rather than arbitrary schedules. Proper lubrication regimens tailored to specific valve designs and operating conditions prevent premature wear and ensure smooth, consistent operation. For Control Valves in critical applications, establishing spare parts inventories with essential components such as trim sets, seals, and actuator components minimizes repair times and reduces the financial impact of unplanned failures. Comprehensive maintenance documentation, including baseline performance data, repair history, and configuration changes, provides valuable context for troubleshooting activities and helps identify recurring issues that might indicate underlying system problems. CEPAI's Control Valves are designed with maintenance considerations in mind, featuring modular components that facilitate quick replacement of wear items, accessible lubrication points, and compatibility with leading diagnostic systems that support modern predictive maintenance programs essential for maximizing asset availability in demanding industrial environments.
Total Cost of Ownership Analysis
When selecting Control Valves, evaluating the total cost of ownership (TCO) provides a comprehensive economic perspective that extends far beyond initial procurement costs. Purchase price typically represents only 15-25% of lifetime costs, with energy consumption often constituting the largest expense over the valve's service life. High-performance Control Valves may command premium prices but deliver substantial lifetime savings through reduced energy consumption, lower maintenance requirements, and extended service intervals. Maintenance costs include routine service, emergency repairs, spare parts inventory, and associated labor—all directly influenced by valve design quality and material selection. Premium Control Valves with robust construction and optimized flow paths typically require less frequent maintenance and component replacement, reducing lifetime maintenance expenses despite higher initial costs. Production losses during valve-related downtime often represent the most significant hidden cost, particularly in continuous process industries where unplanned shutdowns can cost thousands of dollars per hour. Control Valves designed for reliability and equipped with diagnostic capabilities help minimize these costly disruptions by identifying potential issues before they cause failures. Environmental compliance costs related to fugitive emissions and leakage must also be considered, particularly in industries facing stringent regulatory requirements. CEPAI's engineering team assists customers in conducting comprehensive TCO analyses that quantify lifetime benefits of their premium Control Valves, demonstrating how advanced design features, superior materials, and integrated diagnostics deliver substantial economic advantages despite potentially higher acquisition costs—a value proposition particularly compelling for critical applications where reliability and performance directly impact production economics.
Upgrading and Retrofitting Considerations
As industrial processes evolve and operational requirements change, upgrading and retrofitting existing Control Valves often presents a cost-effective alternative to complete replacement. Retrofit opportunities include upgrading mechanical components such as trim sets, seals, and actuators to enhance performance characteristics while retaining the existing valve body. These targeted upgrades can significantly improve control precision, rangeability, and shutoff capability without the expense and disruption of complete valve replacement. Digital upgrades represent another valuable retrofit path—replacing conventional positioners with smart, communicating versions enables advanced diagnostics and integration with digital control systems without valve body replacement. These control upgrades bring older valves into compliance with modern automation standards while providing valuable diagnostic capabilities that enhance maintenance efficiency. Standardization initiatives often drive retrofit projects, with facilities seeking to reduce spare parts inventories and standardize maintenance procedures across diverse valve populations. Retrofit kits designed for compatibility across multiple valve models help achieve these standardization goals while optimizing maintenance efficiency. Assessing retrofit feasibility requires careful evaluation of existing valve condition, expected remaining service life, and potential performance improvements achievable through upgrades. This analysis must consider direct costs, installation complexity, potential process disruptions, and expected benefits, including improved control performance, reduced maintenance requirements, and enhanced diagnostic capabilities. CEPAI offers comprehensive retrofit solutions for both their Control Valves and competitors' products, with standardized upgrade kits and conversion packages that extend equipment life while bringing legacy valves up to current performance standards—a particularly valuable service for facilities seeking to maximize return on existing assets while gradually transitioning to newer technologies without wholesale replacement programs.
Conclusion
Selecting the right Control Valves for your process requires careful consideration of technical requirements, system integration, maintenance implications, and lifecycle costs. CEPAI Group's comprehensive range of high-performance control valves combines exceptional durability with high-precision control performance and is backed by extensive R&D investment and innovative engineering solutions. Our pre-sales technical consultation ensures optimal valve selection while our customized solutions address your unique process challenges. With ISO-certified quality management systems and rigorous testing protocols, we deliver unmatched reliability and performance. Ready to optimize your process control? Contact our expert team at cepai@cepai.com to discover how our advanced Control Valves can enhance operational efficiency and system reliability.
References
1. Smith, J.R. & Thompson, A.L. (2023). Advanced Control Valve Selection for Process Industries. Journal of Fluid Control Engineering, 45(3), 128-142.
2. Martinez, R.B. (2024). Materials Science in Modern Control Valve Applications. Industrial Process Control, 18(2), 67-85.
3. Chen, W.T. & Patel, V.K. (2023). Integration Challenges of Smart Control Valves in Legacy Systems. Automation Technology Review, 29(4), 213-229.
4. Wilson, D.G. (2024). Lifecycle Cost Analysis of High-Performance Control Valves. Journal of Industrial Maintenance & Reliability, 37(1), 42-58.
5. Johnson, E.M. & Rodriguez, L.P. (2023). Preventive Maintenance Strategies for Critical Control Valve Applications. Plant Engineering Quarterly, 56(2), 98-114.
6. Anderson, S.K. & Yamamoto, H. (2024). Digital Transformation in Fluid Control Systems: The Role of Intelligent Control Valves. Engineering Innovation Review, 12(3), 175-191.

Get professional pre-sales technical consultation and valve selection services, customized solution services.
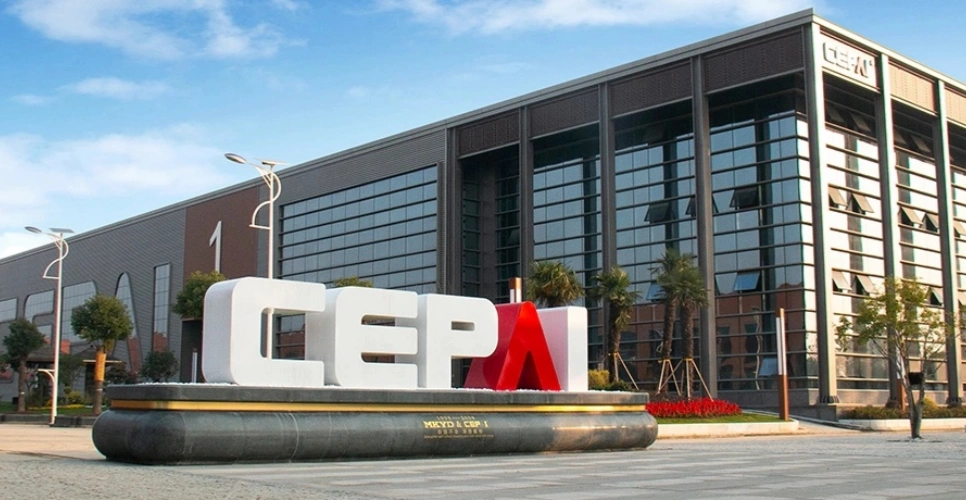
About CEPAI